Home \ International \ A Wirtgen Group machine train on a landfill construction project in Northern Hesse
A Wirtgen Group machine train on a landfill construction project in Northern Hesse
04/05/2022
Pubblicato da Ettore Zanatta
A Wirtgen Group machine train on a landfill construction project in Northern Hesse, Germany, with challenging construction of a 25,000-m² landfill liner.
In the course of an extension programme for a landfill site for demolition waste and contaminated soil in the north of the state of Hesse (Kassel District, Germany), the permanent sealing of the base was of vital importance. The construction of this impermeable liner prevents environmental damage due to contaminated water seeping through deposited waste. A train of Wirtgen Group machines, comprising tractor-towed stabilisers, soil compactors, asphalt pavers and John Deere motor graders, took up the challenge.
The site was split up into 13 separate strips for the construction of the 330 m x 80 m landfill liner. A layer of crushed limestone hardcore followed by four 25-cm layers of clay had to be placed on each of the strips and successively checked for impermeability. Following this, the liner was finished by paving two layers of a specially formulated landfill asphalt mix.
The team processed 52,800 t of the clay-sand mixture. The core element of the landfill liner is the four layers of clay. The material, a mixture of clay and sand, was transported to the landfill project from an extraction site 50 km away. In view of the one hour required for the haulage of this material from source to site and considering that the clay mustn’t be allowed to get wet, painstakingly organised site logistics were absolutely critical. As the scheduled placement of 1,200 t of clay-sand mixture a day could only take place in dry weather, the reliability, availability, quality and performance of the equipment deployed all played a decisive role. ‘We’ve had nothing but positive experience with Wirtgen Group machines for many years. On challenging jobs like this, it’s also a great advantage that we get the machines and the service from the same people’, said Michael Huthwelker, master of crafts in road construction from Wachenfeld, the lead contractor on the project.
After the material was unloaded on the site, it was spread by a bulldozer and a John Deere 622GP motor grader, which were then followed by a Wirtgen WS 250 tractor-towed stabiliser. Due to the aeration of the clay by the milling and mixing rotor of the WS 250, the ground needed no further improvement by pre-spreading with lime or cement. On completion of this step, a Hamm 3414 HT P soil compactor compacted the freshly homogenised clay layer. It enlarged the surface area with its padfoot drum – the P stands for Padfoot – to accelerate the evaporation of the moisture contained in the clay. The John Deere motor grader then took over and levelled the strip. After an appropriate pause for drying, a Hamm H 13i compactor with a smooth drum compacted the layers. The machine train repeated this sequence of earthworks for each of the four clay layers. In all, the train processed 52,800 t of the clay-sand mix in this manner.
A special aspect of landfill building projects is the construction of leachate drainage systems to minimise threats to the environment. Their task is to drain off contaminated water. At the landfill site in Hofgeismar, the leachate drainage system consists of a massive asphalt block. Here, a Vögele Super 1800-2 paver with a fixed width Vögele screed placed an asphalt package in six layers with an overall thickness of 36 cm at the exact centre of the extension area. The run-off channel for the leachate was then milled into this asphalt block.
A Vögele Super 1800-3i paver with an AB 500 extending screed was also in use on the site for the subsequent paving of several layers of specially formulated landfill asphalt mix over the clay package. Such mixes are characterised by a higher percentage of bitumen and more fines, which achieves particularly high impermeability. Thanks to the impermeable liner, the landfill is now ideally equipped for an environmentally friendly future with no leakage of harmful leachate.

Ultime notizie di Wirtgen Macchine
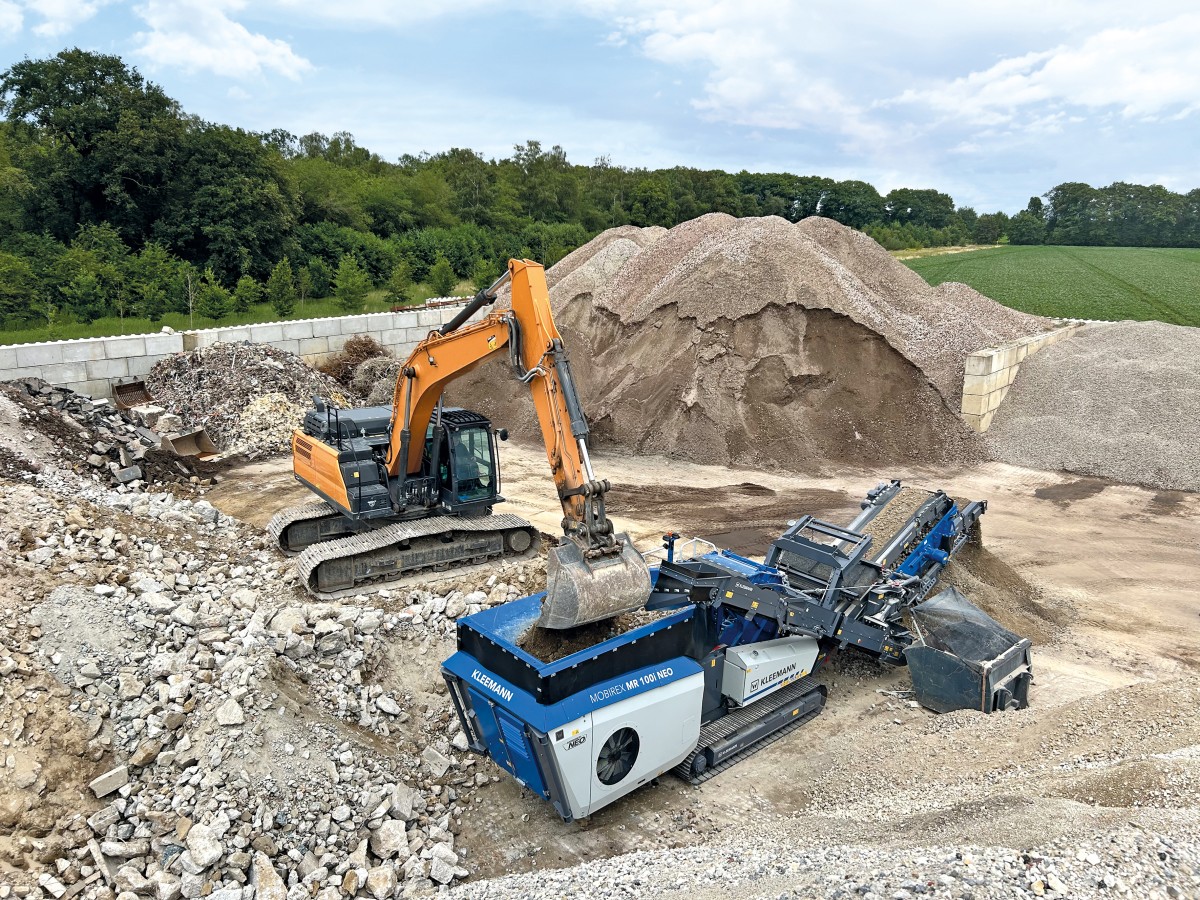
Earthmoving Machinery
21/11/2024
Kleemann: New compact crusher used for recycling
Impact crusher MOBIREX MR 100i NEO impresses during operatio...
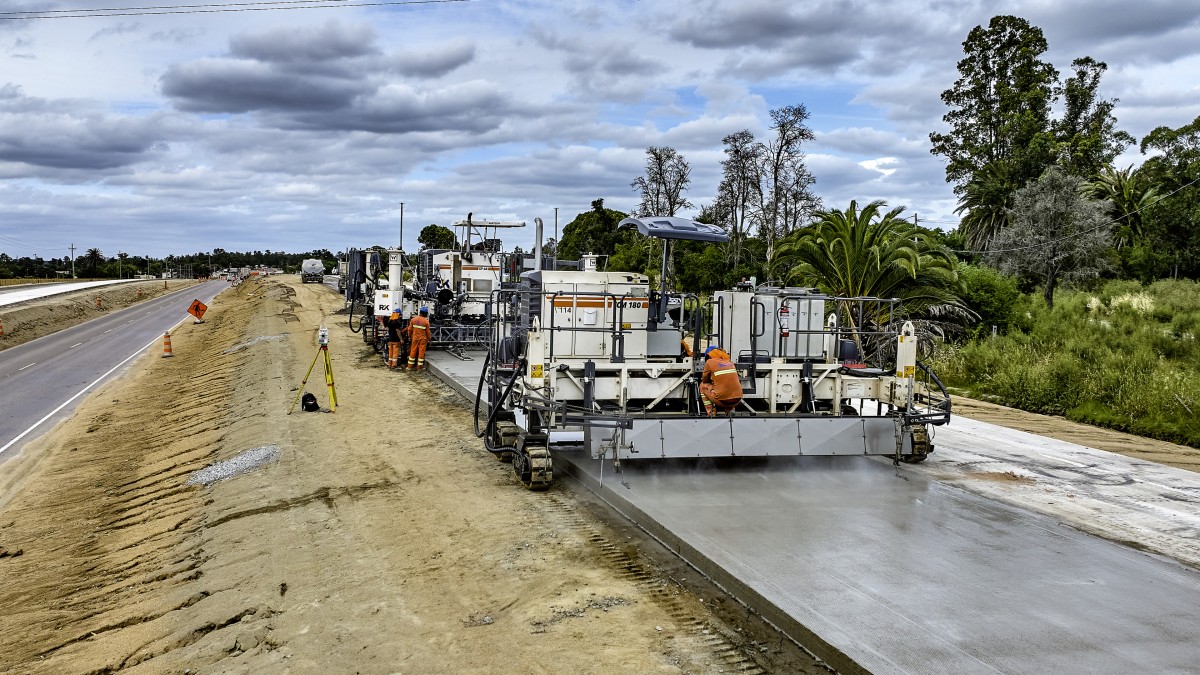
Road Machinery
04/11/2024
Wirtgen: Widening of the Ruta 5 highway from Montevideo to the Brazilian Border
Efficient concrete paving solutions from Wirtgen ensure the...
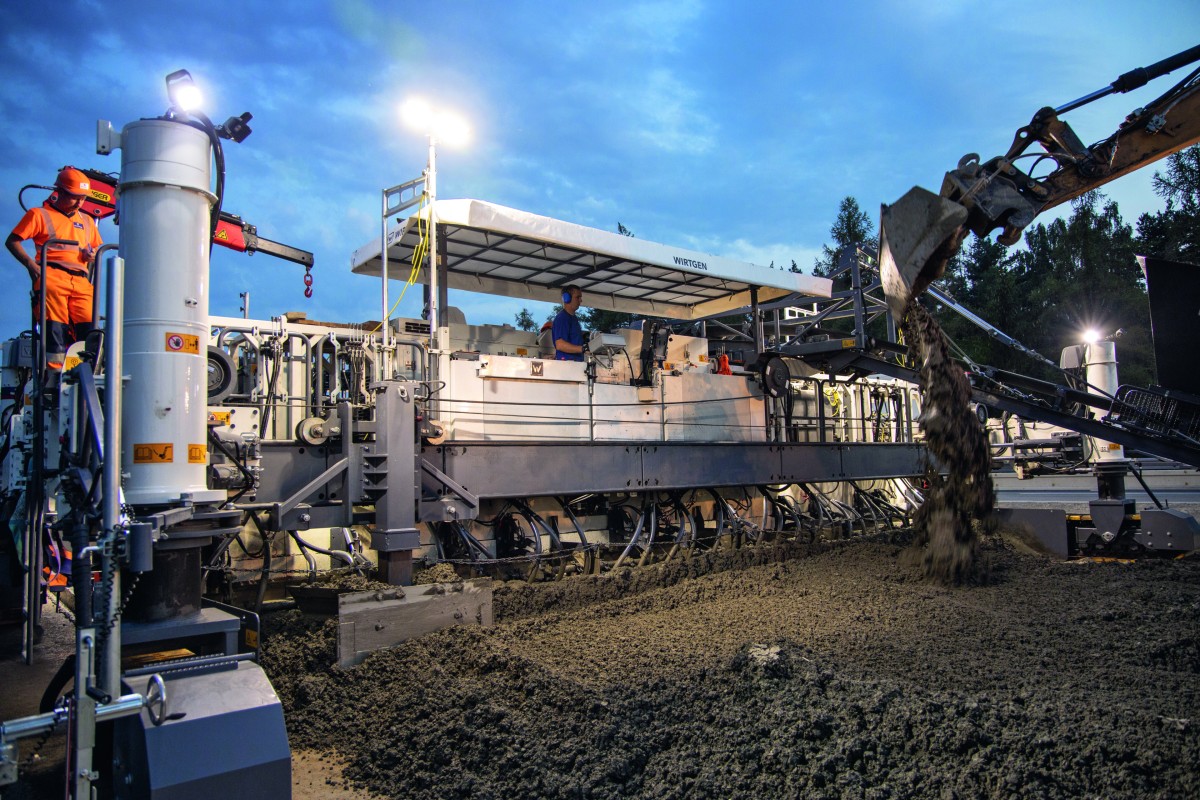
Road Machinery
31/10/2024
Wirtgen: Concrete paving with inset slipform pavers
Wirtgen has been offering machines for inset slipform paving...
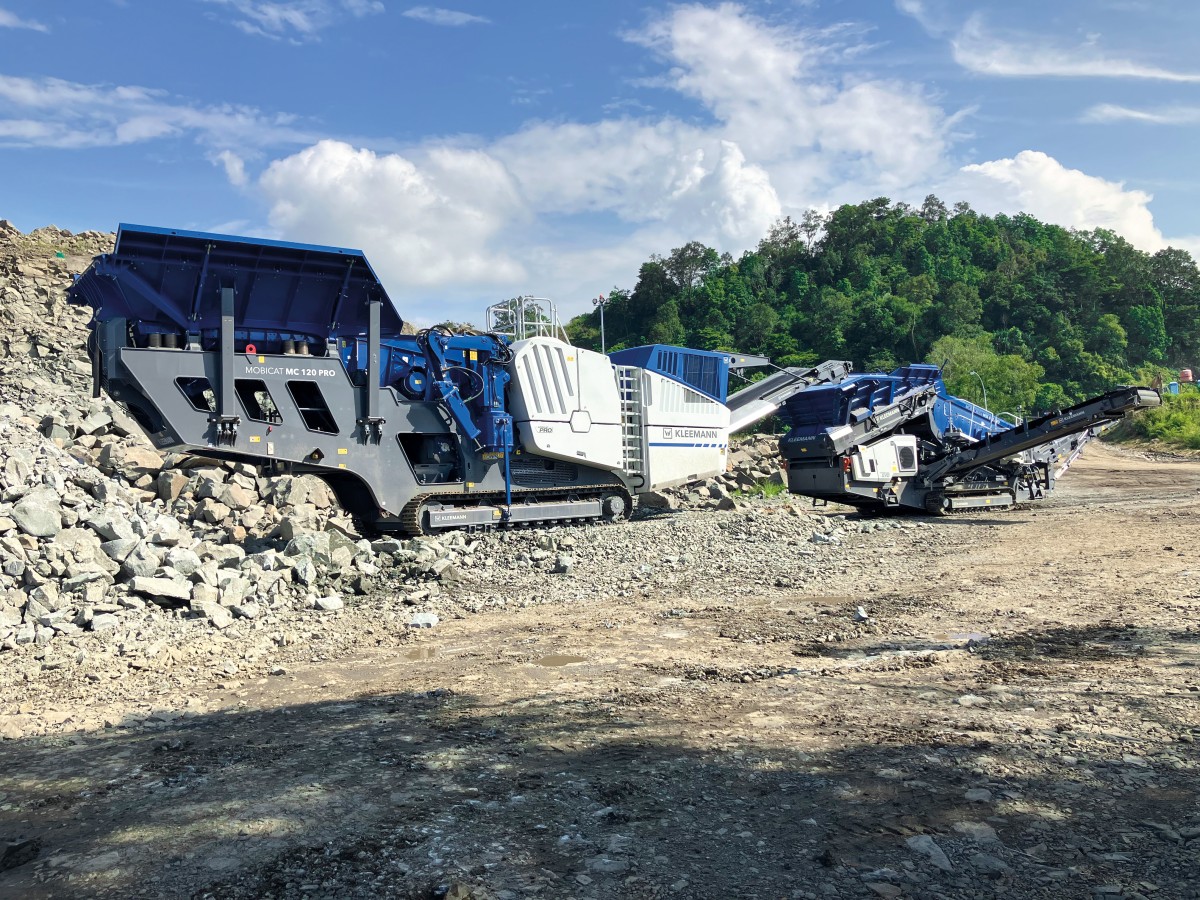
Earthmoving Machinery
28/10/2024
Kleemann: Andesite processing in Indonesia
A MOBICAT MC 120 PRO and a MOBISCREEN MSS 802 EVO are deploy...
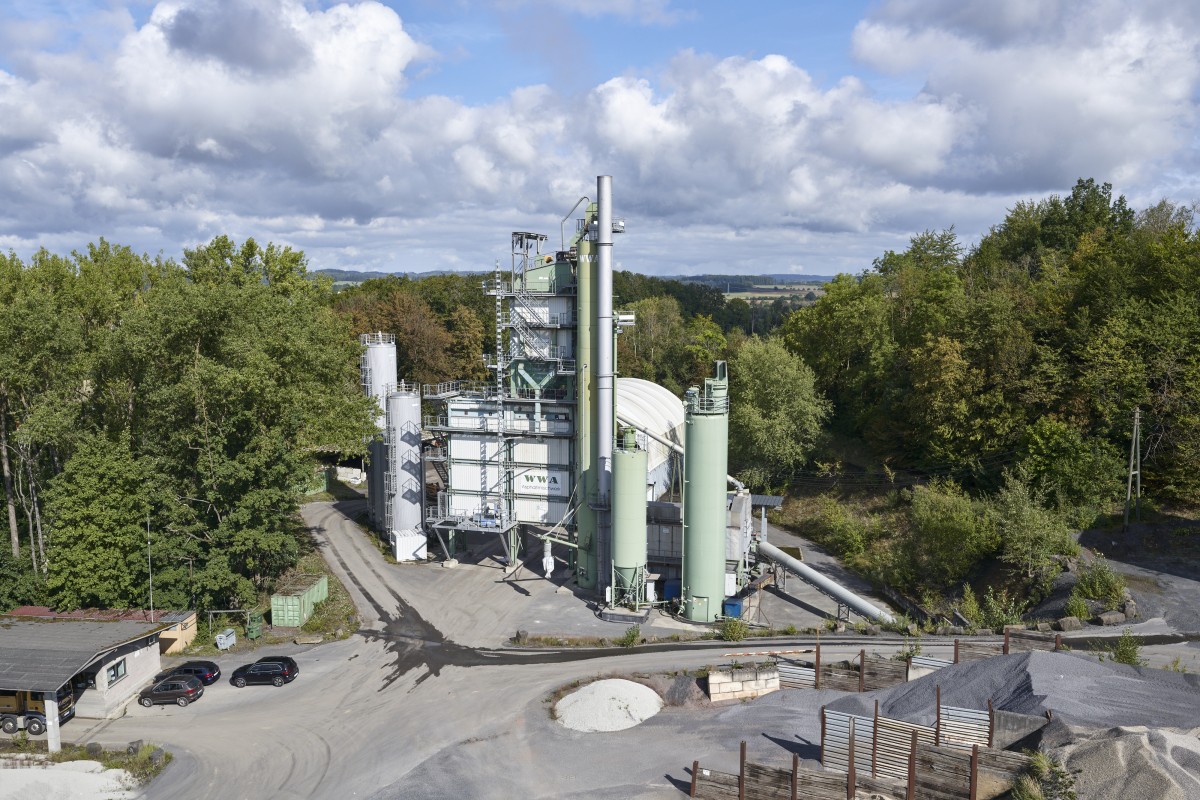
Earthmoving Machinery
24/10/2024
Benninghoven's REVOC system proven in practice
The REVOC Retrofit solution has been installed at an existin...
Road Machinery
01/10/2024
The Wirtgen Group at Paving Expo 2024
The Wirtgen Group presents groundbreaking technologies at Pa...
Altri International
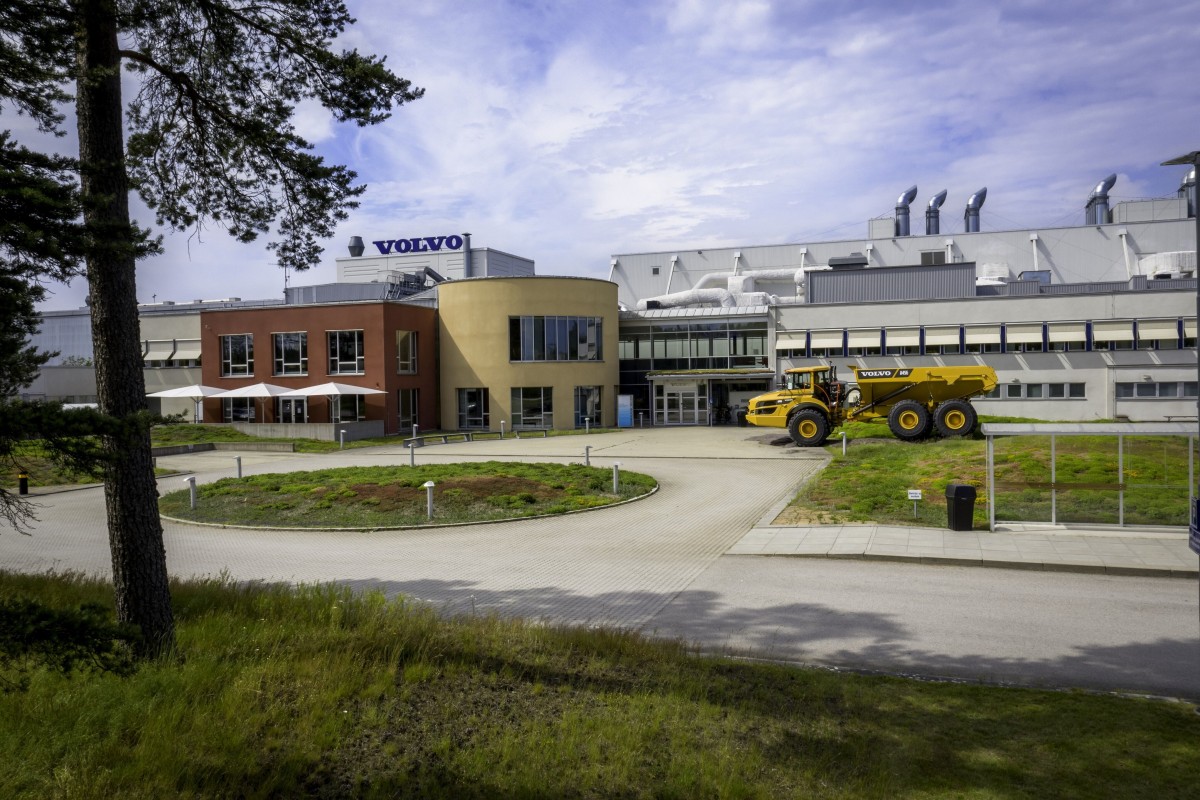
International
27/11/2024
Home of Volvo Construction Equipment’s pioneering articulated haulers advances to Climate Efficient Site
As one of the construction industry’s most active drivers of...
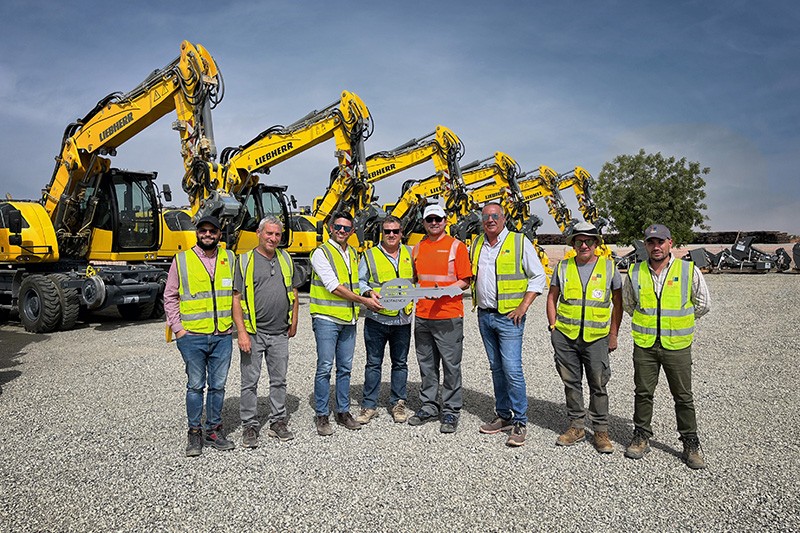
International
26/11/2024
Mota-Engil orders 10 Liebherr railroad excavators for a major project in West Africa
The Portuguese construction company Mota-Engil has once agai...
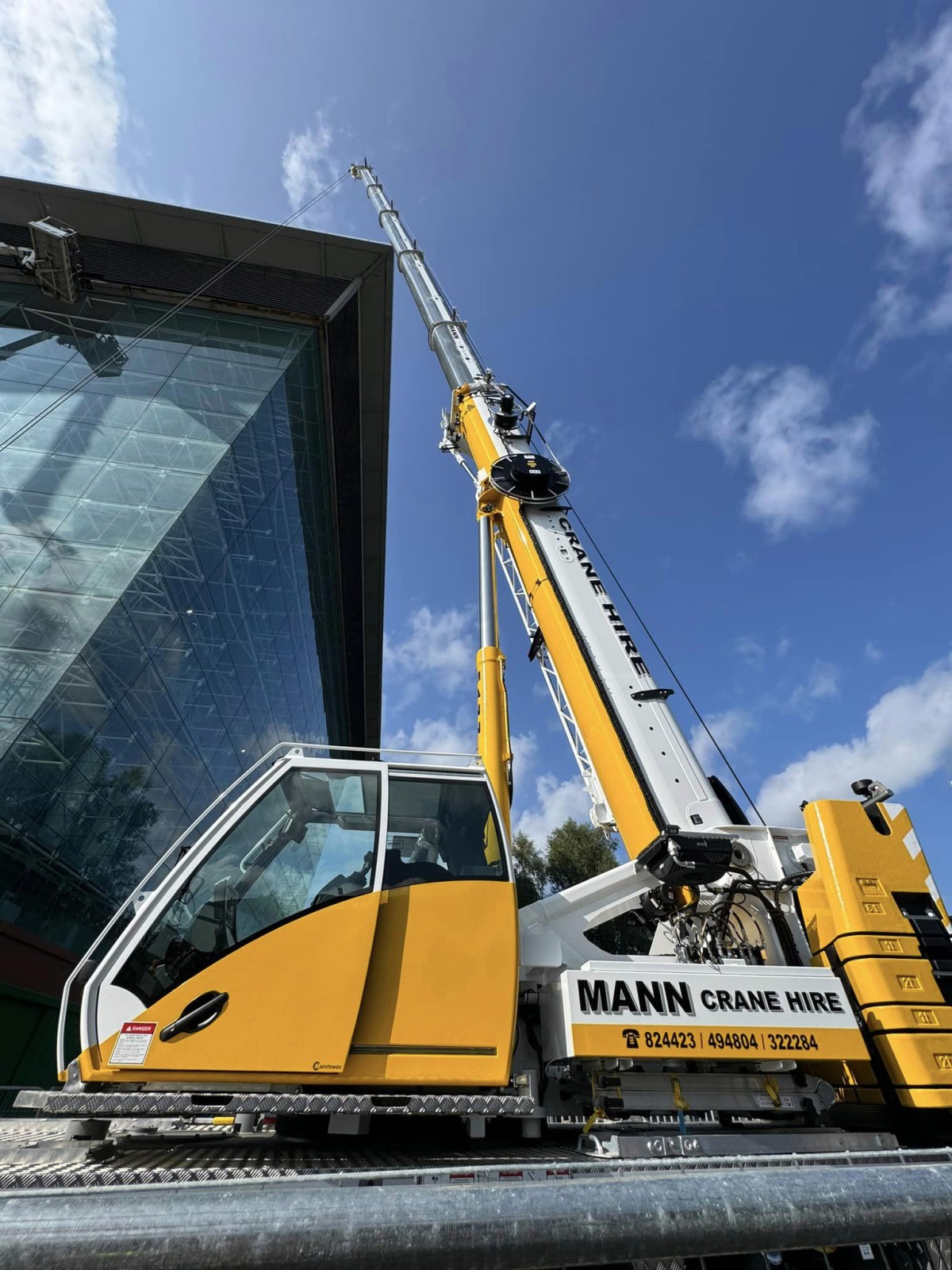
International
25/11/2024
New Grove GMK3060L-1 drives busy schedule for Mann Crane Hire
• Mann Crane Hire selected the GMK3060L-1 for its class-lead...
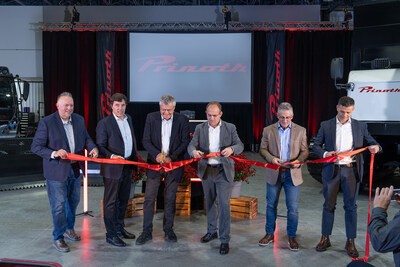
International
25/11/2024
Prinoth Unveils Expanded Production Facility in Granby, Canada
Prinoth held an event to announce the official opening of it...
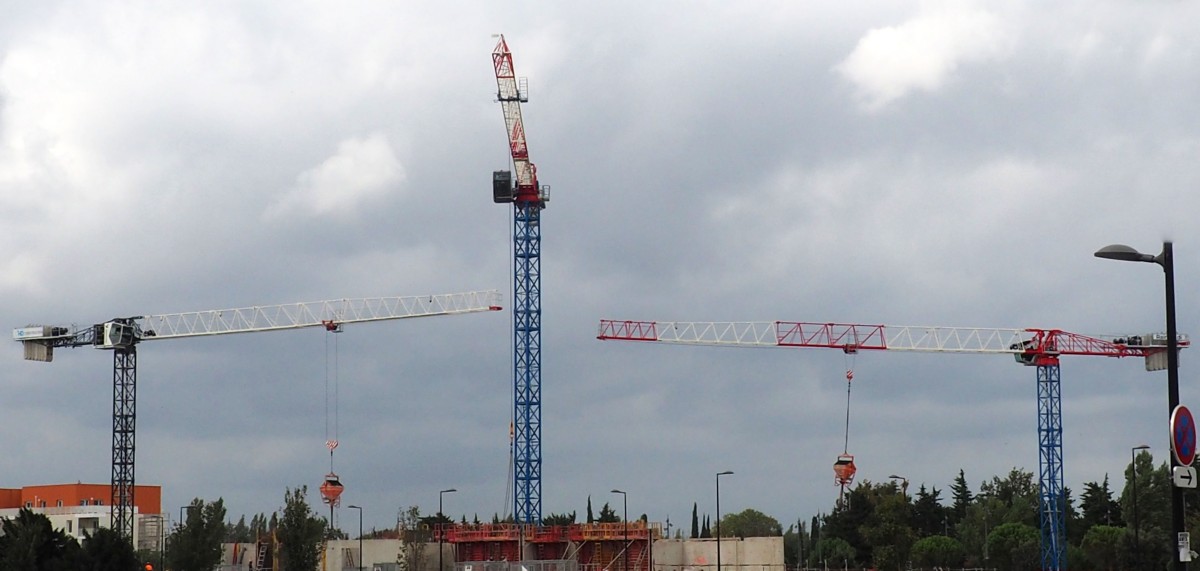
International
23/11/2024
GPMat International takes delivery of two Raimondi T147s residential development in the South of France
- Official agent of France expands its product lineup with t...
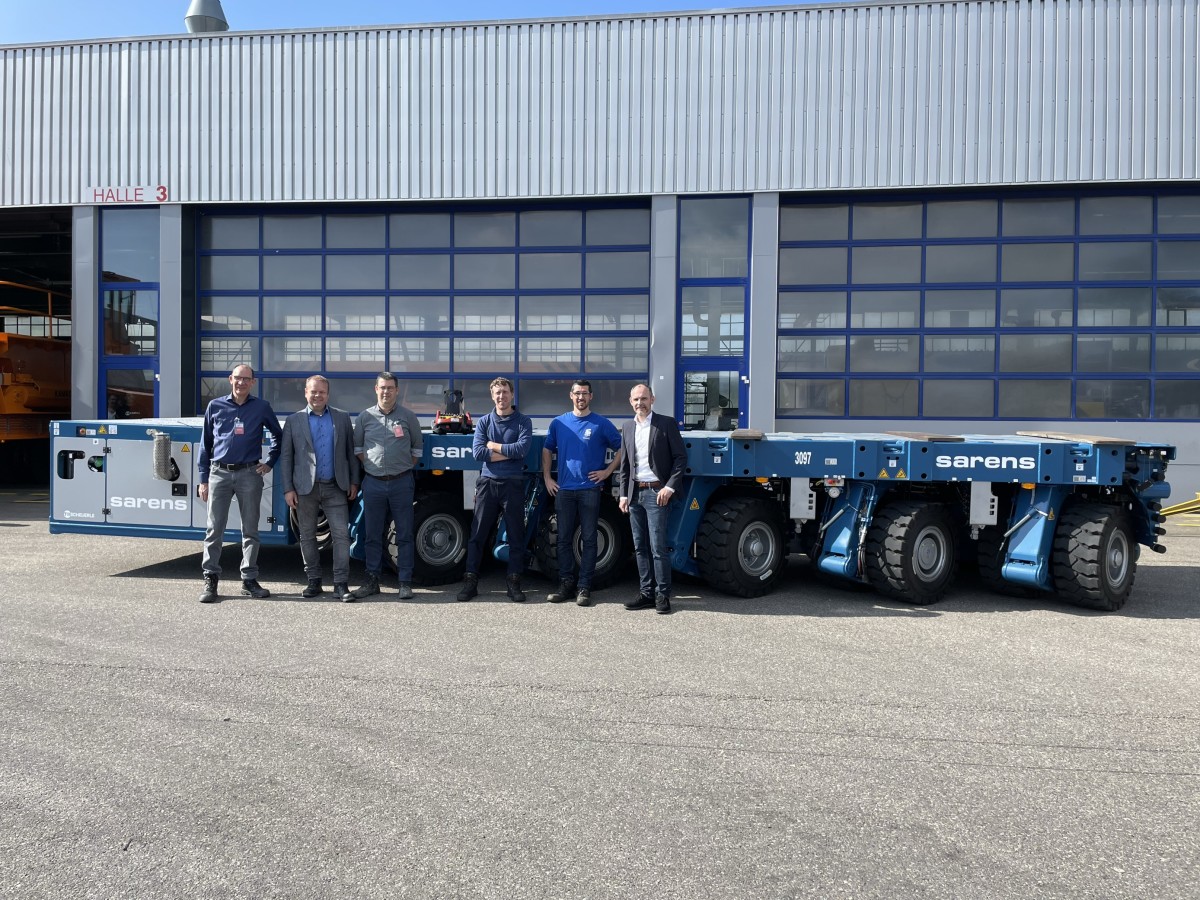
International
22/11/2024
Sarens acquires additional SCHEUERLE SPMT K24 modules
renowned for its expertise in crane rental services, heavy l...