Home \ International \ Benninghoven: First virtually carbon-neutral asphalt production in Germany
Benninghoven: First virtually carbon-neutral asphalt production in Germany
20/08/2024
Pubblicato da Ettore Zanatta
The asphalt mixing plant in Aichach was using around 600,000 l of heating oil to produce approx. 60,000 t of asphalt per year.
At the request of the operating company, an asphalt mixing plant in Aichach, Bavaria was to be powered exclusively by renewable energy and to be largely carbon-neutral. Asphalt mixing plant manufacturer Benninghoven was called in to implement the plan for green asphalt. Asphalt production now uses wood dust instead of heating oil.
The asphalt mixing plant in Aichach was using around 600,000 l of heating oil to produce approx. 60,000 t of asphalt per year. That meant emissions of 1,800 t of CO₂. As an expert in multi-fuel burners, Benninghoven recognised the great future potential of wood dust as a fuel early on. The processing technology required for producing high quality wood dust was provided by a specialist company.
The endeavour was designed to be a research and development project from the outset. First of all, grant applications and the expert’s reports for fire safety, noise and emissions had to be obtained from the operator of the plant. This was followed by a lengthy approval process, as the authorities had no experience figures to fall back on. Various requirements specified by the district administration had to be complied with, including continuous emissions measuring and the burner capacity. Taking into account the plant output, Benninghoven restricted the burner output to 12 MW/h. In the event of a future expansion of the plant, the burner has enough reserves to support the growth.
All requirements centred around complying with the German TA-Luft regulation which came into force in 2021. Only four weeks after installation of the burner, the Benninghoven design engineers were able to achieve levels 50% below the requirements of TA-Luft in continuous emissions measurements. Measurements carried out by the TÜV inspection association confirmed these values. Benninghoven is the only manufacturer who meets and can therefore guarantee the limits for the plant with a wood dust burner.
For Christian Schweiger, contractor and operator of the mixing plant in Aichach, the investment has been worthwhile – also financially, as the carbon tax on fossil fuels has increased significantly. “At the start of the project, we assumed that sustainability will be an important topic for the future. The fact that we are already saving around 20% of costs due to the switch to wood dust was a pleasant surprise.”

Ultime notizie di Wirtgen Macchine
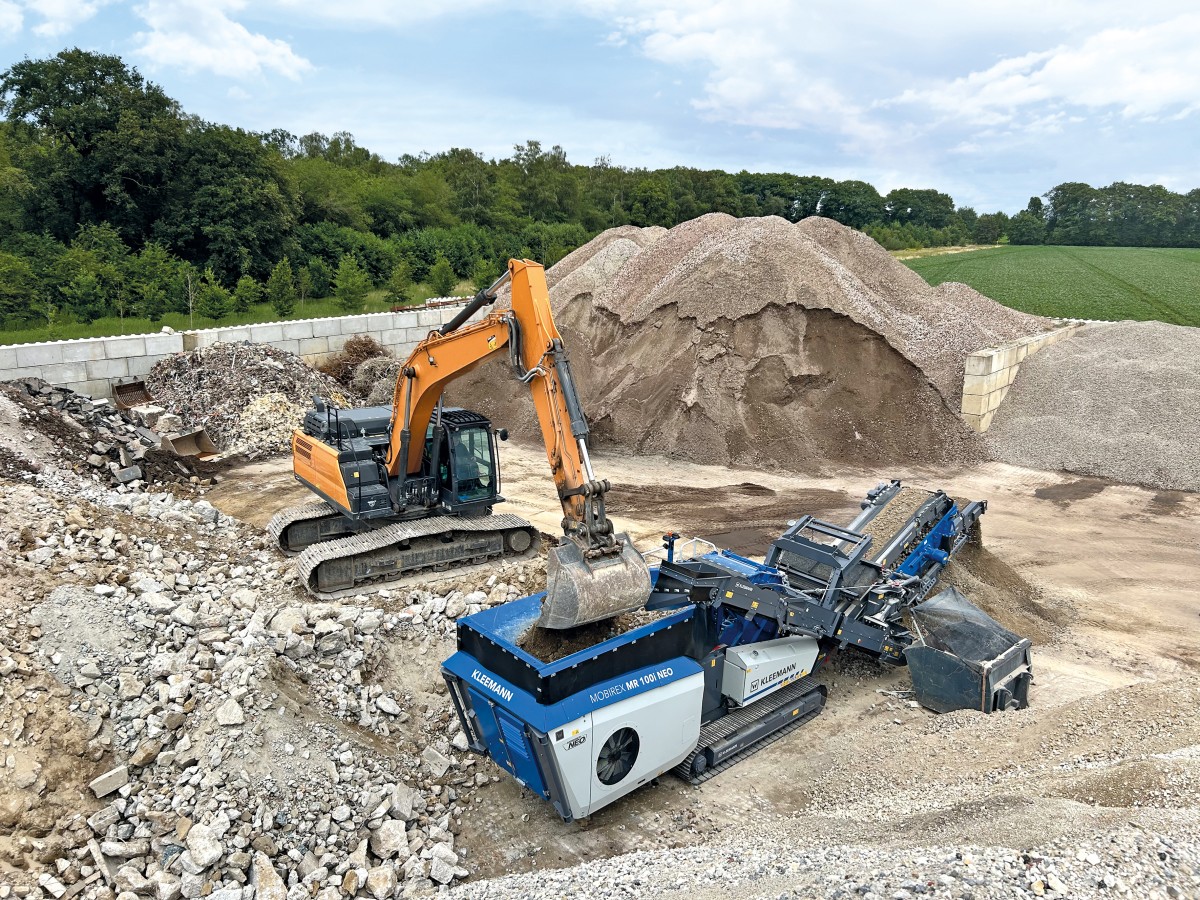
Earthmoving Machinery
21/11/2024
Kleemann: New compact crusher used for recycling
Impact crusher MOBIREX MR 100i NEO impresses during operatio...
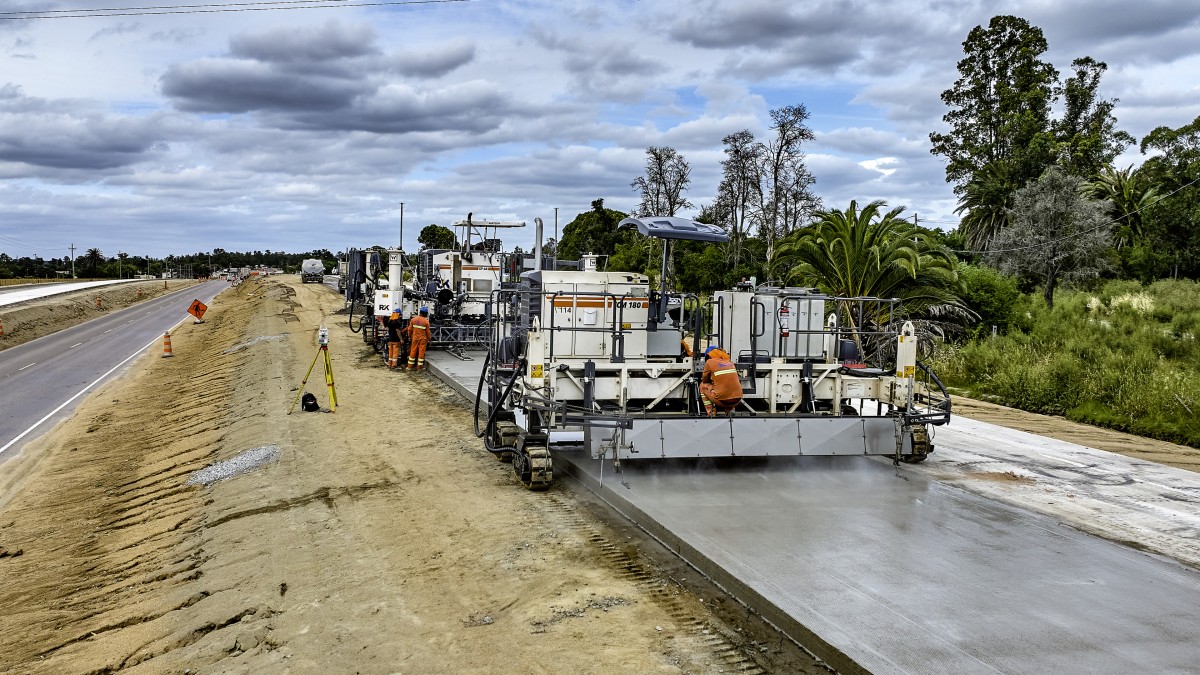
Road Machinery
04/11/2024
Wirtgen: Widening of the Ruta 5 highway from Montevideo to the Brazilian Border
Efficient concrete paving solutions from Wirtgen ensure the...
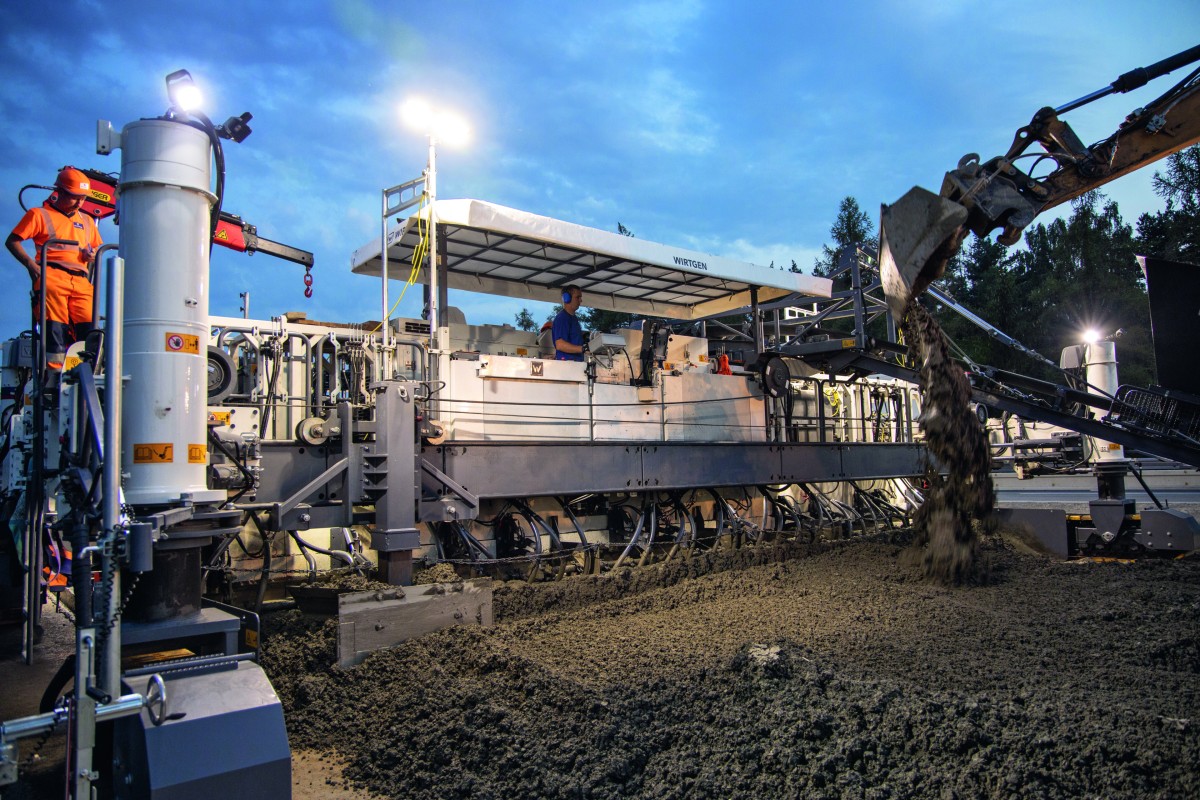
Road Machinery
31/10/2024
Wirtgen: Concrete paving with inset slipform pavers
Wirtgen has been offering machines for inset slipform paving...
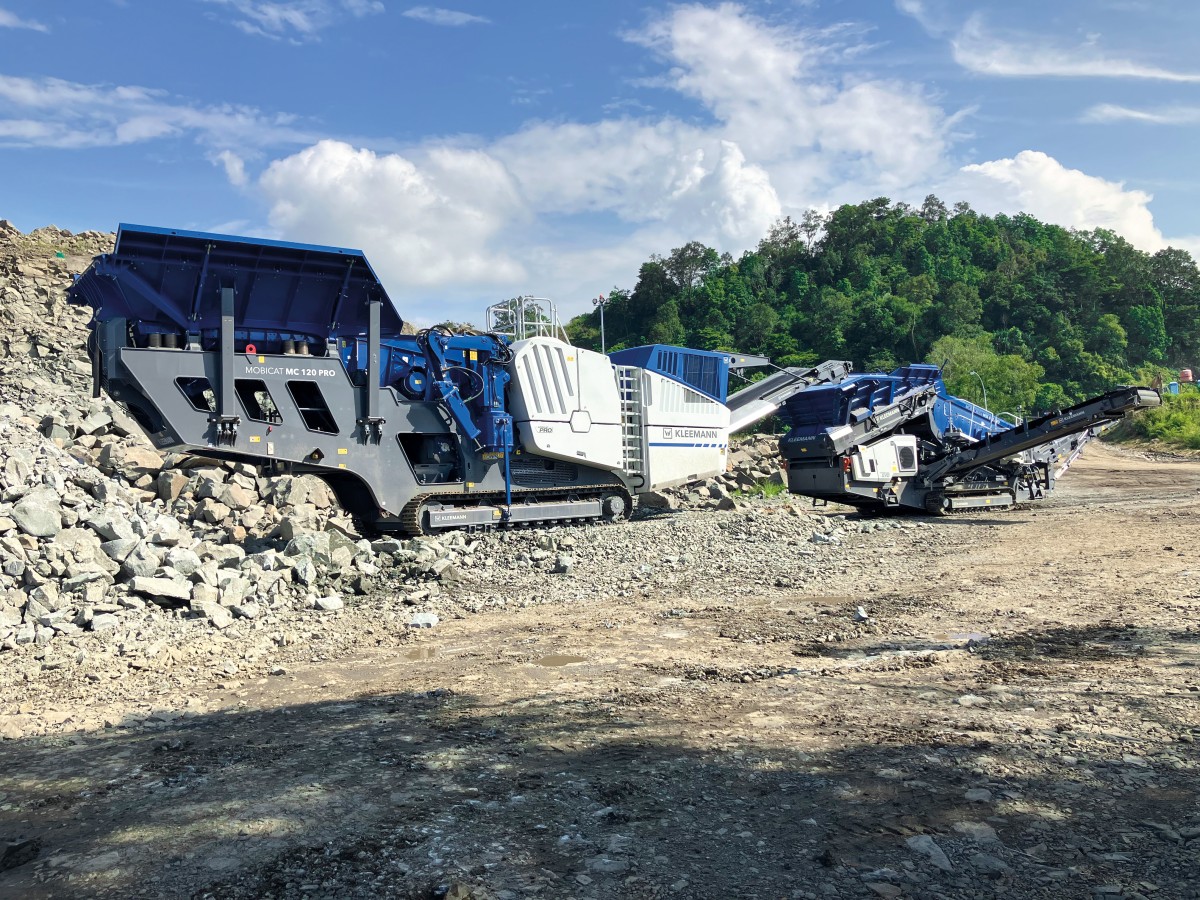
Earthmoving Machinery
28/10/2024
Kleemann: Andesite processing in Indonesia
A MOBICAT MC 120 PRO and a MOBISCREEN MSS 802 EVO are deploy...
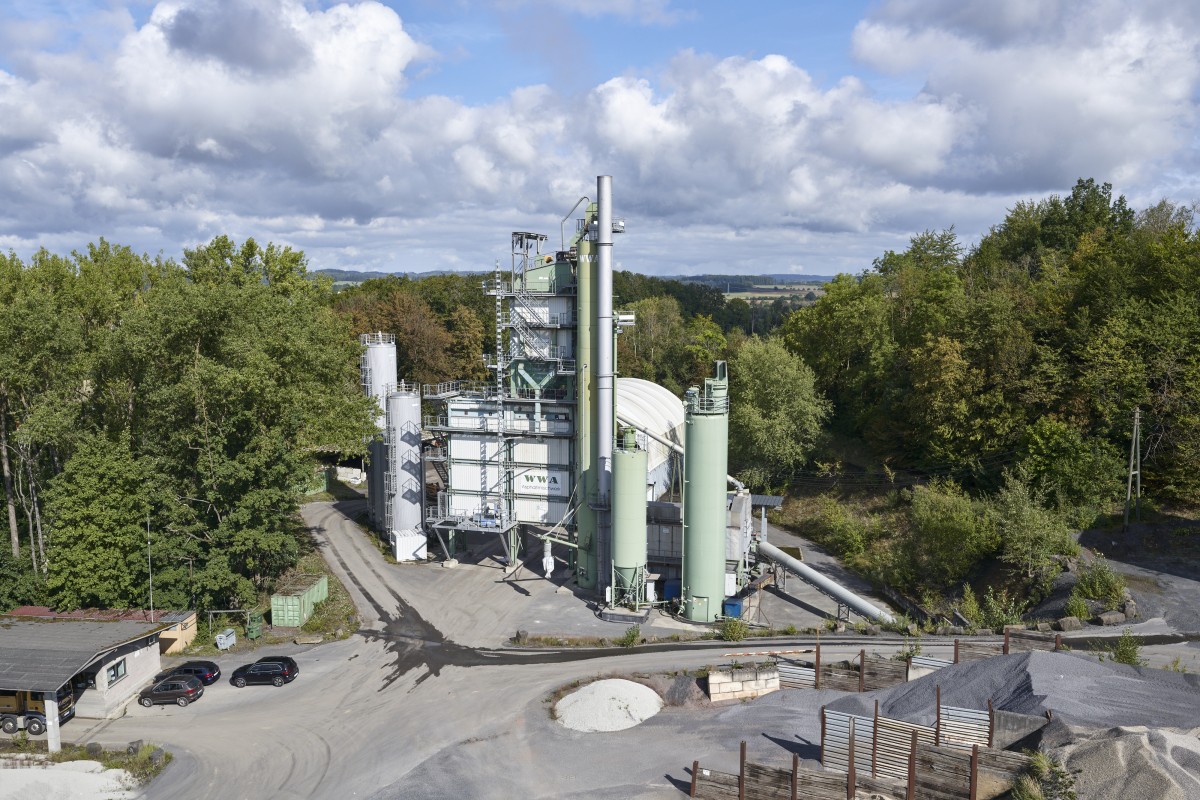
Earthmoving Machinery
24/10/2024
Benninghoven's REVOC system proven in practice
The REVOC Retrofit solution has been installed at an existin...
Road Machinery
01/10/2024
The Wirtgen Group at Paving Expo 2024
The Wirtgen Group presents groundbreaking technologies at Pa...
Altri International
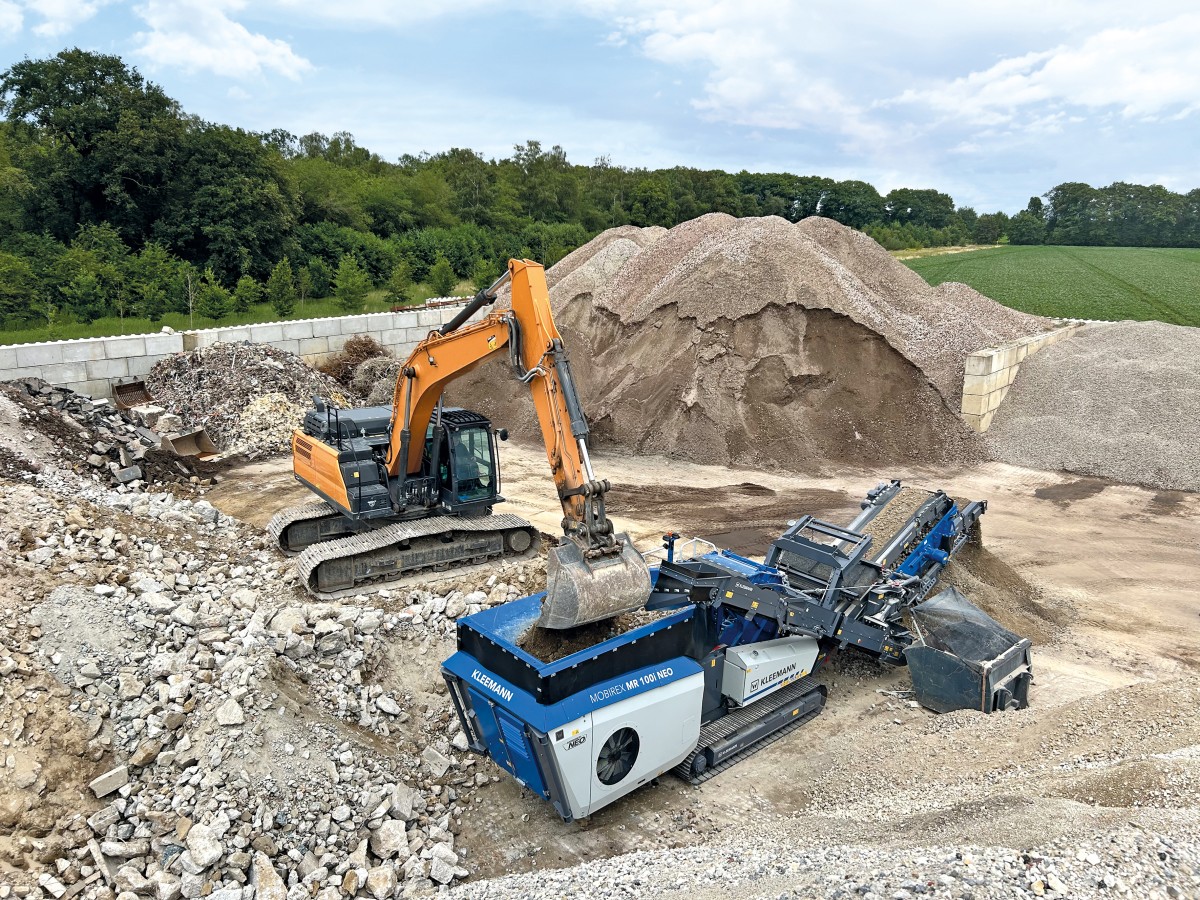
International
21/11/2024
Kleemann: New compact crusher used for recycling
Impact crusher MOBIREX MR 100i NEO impresses during operatio...
International
21/11/2024
SITECH partners with Royal Engineers to create poppy and demonstrate tech offering
The demostration involved creating a ground-level poppy desi...
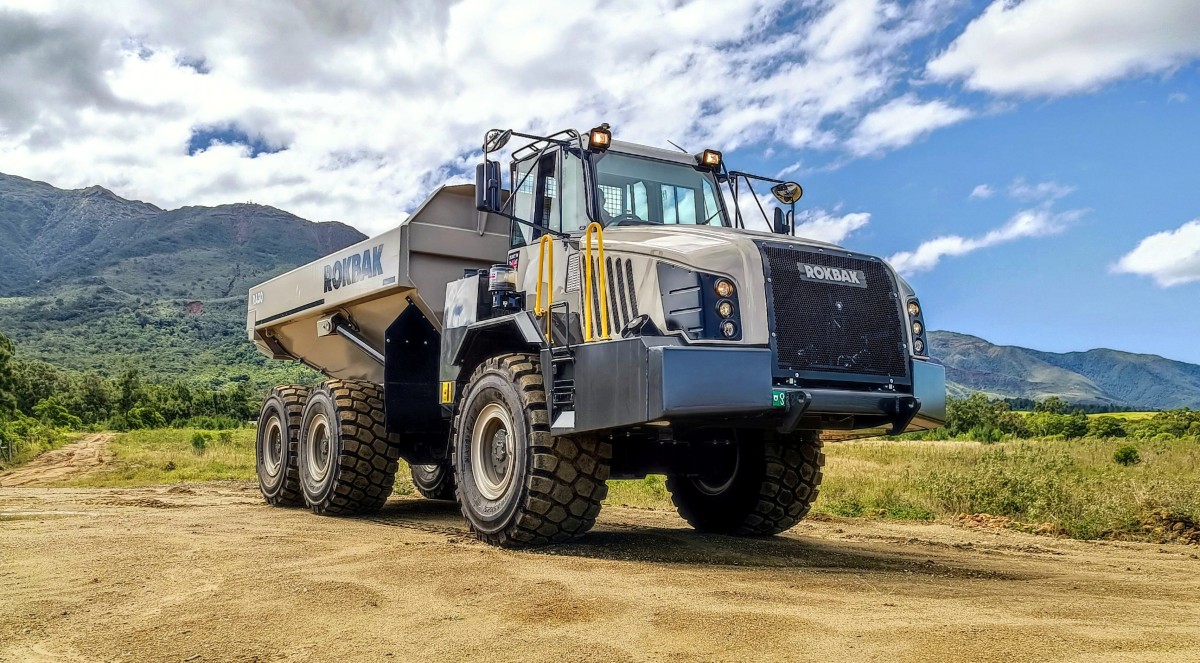
International
20/11/2024
Strong and stable RA30 trucks carry the weight at New Caledonian mine
Three Rokbak RA30 trucks are delivering exceptional durabili...
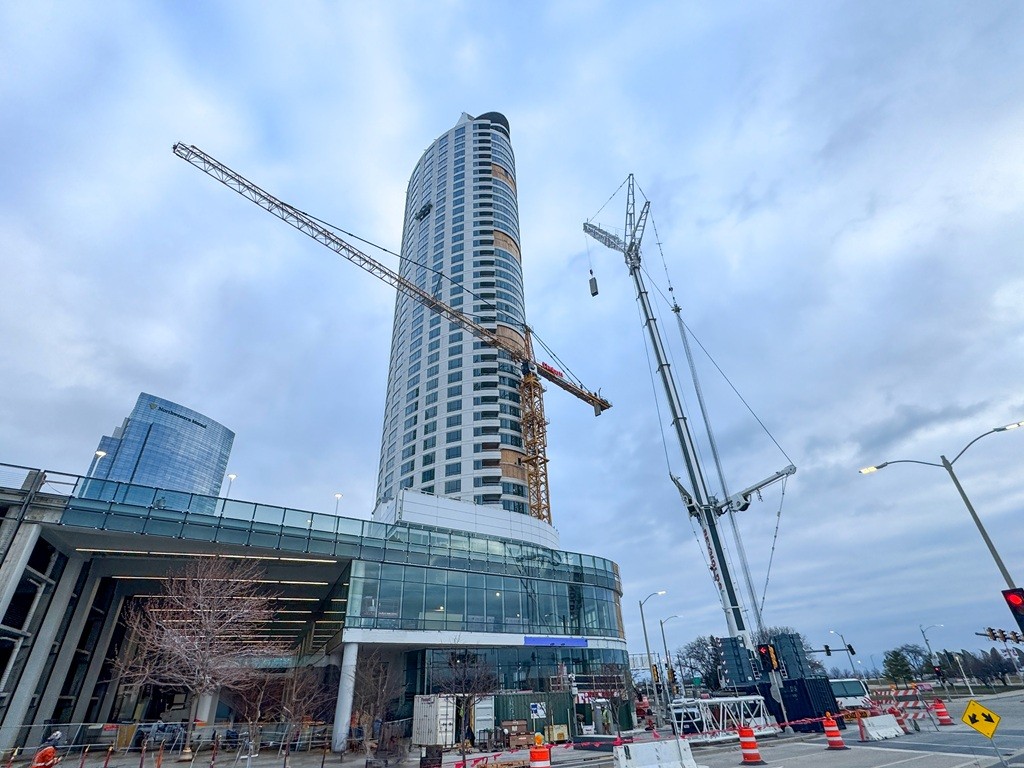
International
20/11/2024
Tadano AC 7.450-1 Performs Double Duty in Wisconsin
A cost-saving and versatile solution was already on site - a...
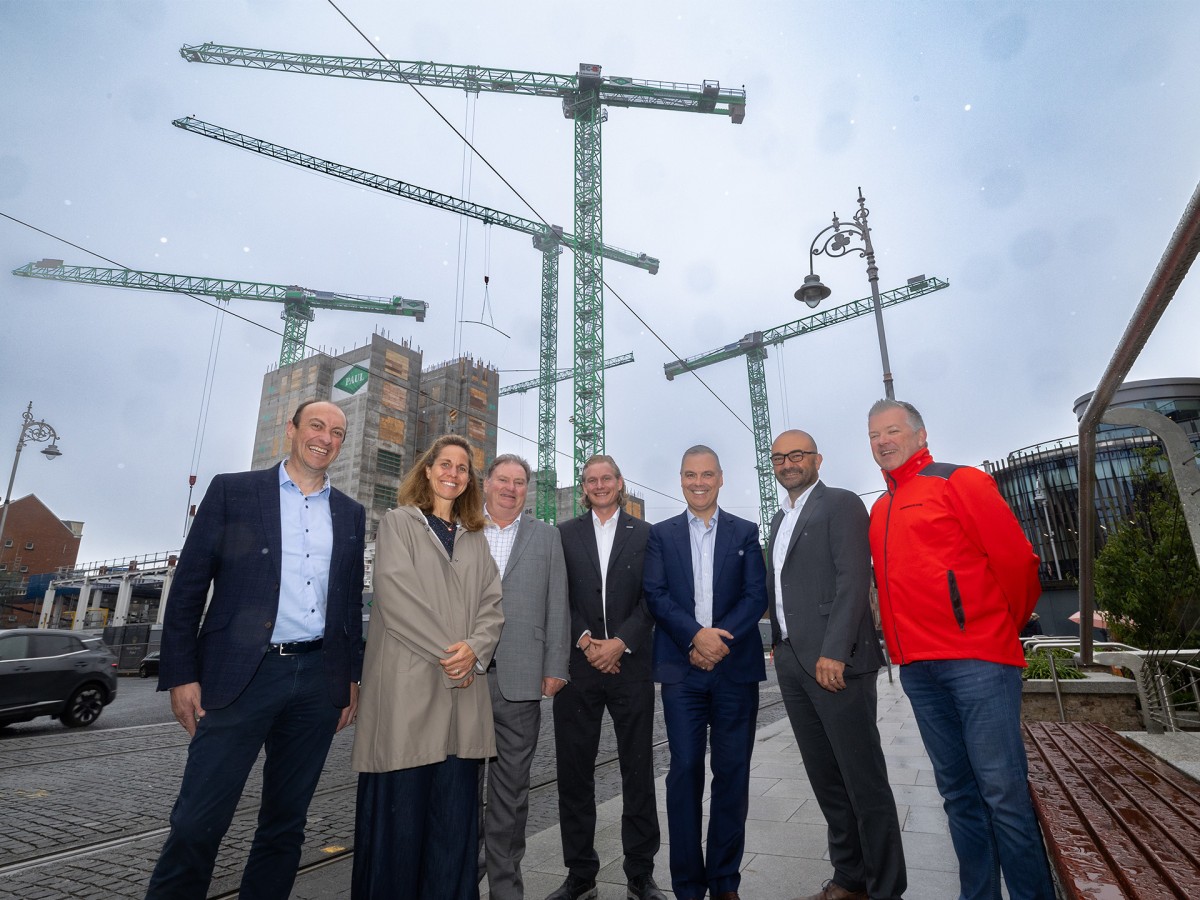
International
19/11/2024
Liebherr Tower Cranes and John Paul Construction celebrate 50 years of partnership
Irish construction company John Paul Construction is celebra...
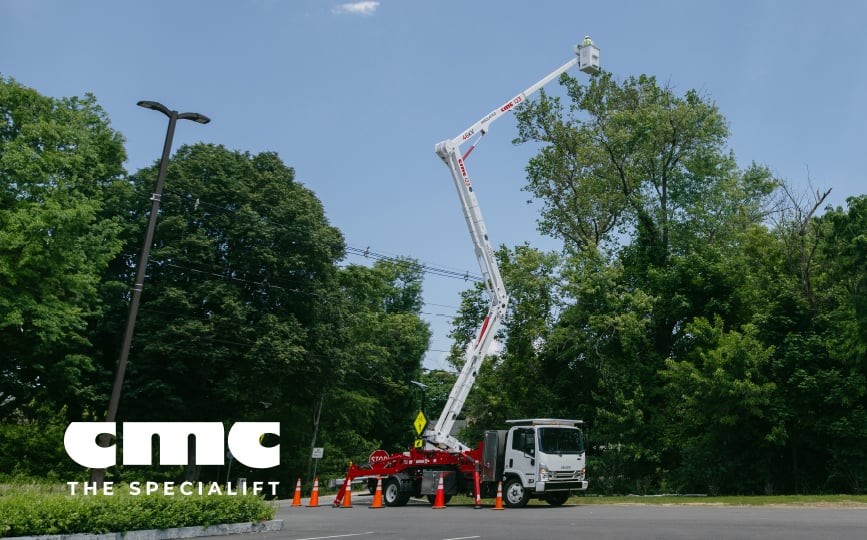
International
18/11/2024
The CMC i23 aerial platform: an example of high performances
CMC i23 is designed to maximise operational efficiency in al...