Home \ International \ Efficient shoulder refurbishment with the Vögele MINI 500
Efficient shoulder refurbishment with the Vögele MINI 500
21/08/2024
Pubblicato da Ettore Zanatta
The representative of the Mini Class proved its worth when paving the shoulder on a road in the Swiss canton of Valais.
The representative of the Mini Class proved its worth when paving the shoulder on a road in the Swiss canton of Valais: the project foresaw the resurfacing and widening of the shoulder at the side of the T9 cantonal road. With Vögele‘s smallest paver, the paving crew was able to complete the project without interruption and in outstanding quality despite some particularly tight spaces.
Raron lies in the picturesque Alpine canton of Valais in southern Switzerland. The T9 cantonal road links the municipality to the A9 highway and serves as the connection to larger towns and villages in the region. As the shoulder was contaminated with mercury, the whole area at the side of the road had to be rehabilitated over a distance of 2.3 km. In the course of this, the lead contractor was also commissioned to widen the shoulder to enable the placement of crash barriers in the asphalt.
Contractor Pius Schmid AG from Visp was awarded the contract for this work and deployed the MINI 500, the smallest road paver from Vögele, on the project. ‘We often take on municipal road construction projects. Especially in cases where we have limited space and narrow pave widths, the realisation with the MINI 500 is significantly faster and delivers higher quality results than conventional manual paving with wheelbarrows, shovels, and a plate compactor’, says Michael Schmid, Member of the Executive Board at Pius Schmid AG.
With the MINI 500, construction contractors can realise small projects in particularly tight spaces by machine paving. The paver is extremely compact and agile and offers a base pave width of 0.9 m and working widths from only 0.25 m to 1.8 m. Its rubber-tracked undercarriage ensures optimum traction on unconsolidated ground and enables outstanding manoeuvrability in the tightest of spaces. The paving crew used a further Mini Class paver from Vögele, a SUPER 800i, for the paving of the base layer and the surface course of the shoulder at the side of the T9. On the 500 m section, the crew encountered numerous tight spots that forced them to pave at varying widths of between 0.9 and 1.35 m. Formerly, the paving crew would have had to pave these parts in a particularly time-consuming and labour-intensive manual paving process. In contrast, the MINI 500 and the AB 135 extending screed enabled the crew to pave the entire section by machine, in outstanding quality and without any interruptions.
The paver’s large material hopper with a capacity of up to 1.5 t also contributed to the efficiency of the workflow on the construction site. The wide, funnel-shaped opening enables uncomplicated feeding of the paving mix to the extra-compact paver by a wheel loader. The compact machine has another big advantage: thanks to its weight of only 1.6 t, it can be transported easily and cost-efficiently from place to place. ‘We can easily transport the MINI 500 to a new project site with a minimum of logistical effort on the back of a truck and, if we need to, can lift it on to elevated working areas with a wheel loader, which is usually available for feeding mix to the paver on most construction sites, anyway’, says Schmid.
The new shoulder had to be paved with a cross slope of 2% to ensure sufficient drainage. The paving crew therefore relied on an automated grade and slope control system specially designed for use with the MINI 500 for height control of the screed’s position. It compares target values with actual values, corrects them if necessary, and has a particularly simple and intuitive operating concept. ‘With the MINI 500, we were able to realise the job easily and efficiently and deliver very precise, high quality results’, says Schmid.

Ultime notizie di Wirtgen Macchine
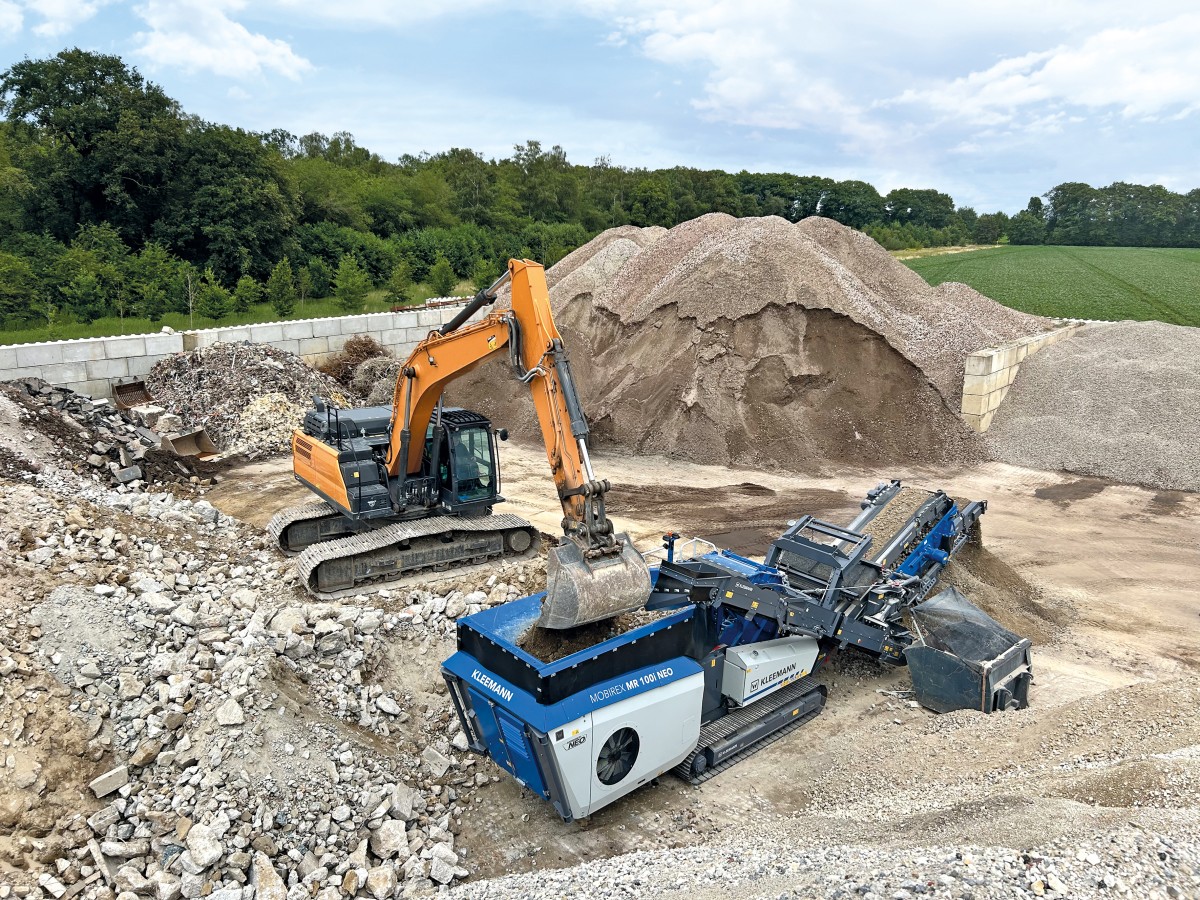
Earthmoving Machinery
21/11/2024
Kleemann: New compact crusher used for recycling
Impact crusher MOBIREX MR 100i NEO impresses during operatio...
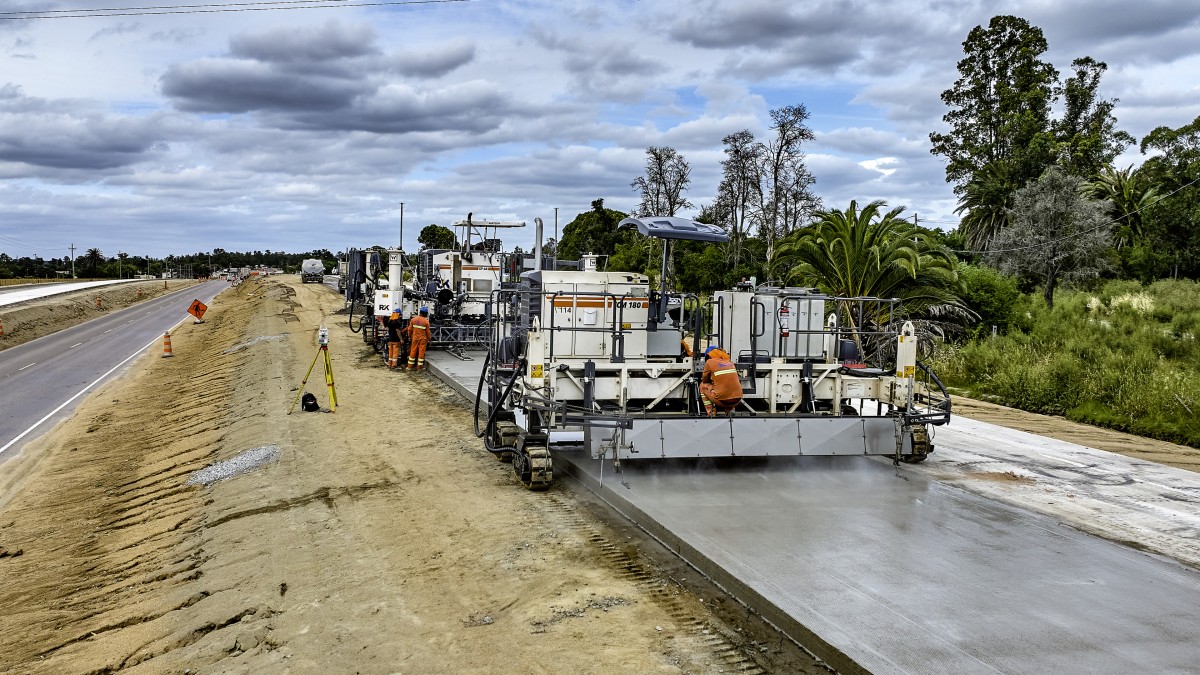
Road Machinery
04/11/2024
Wirtgen: Widening of the Ruta 5 highway from Montevideo to the Brazilian Border
Efficient concrete paving solutions from Wirtgen ensure the...
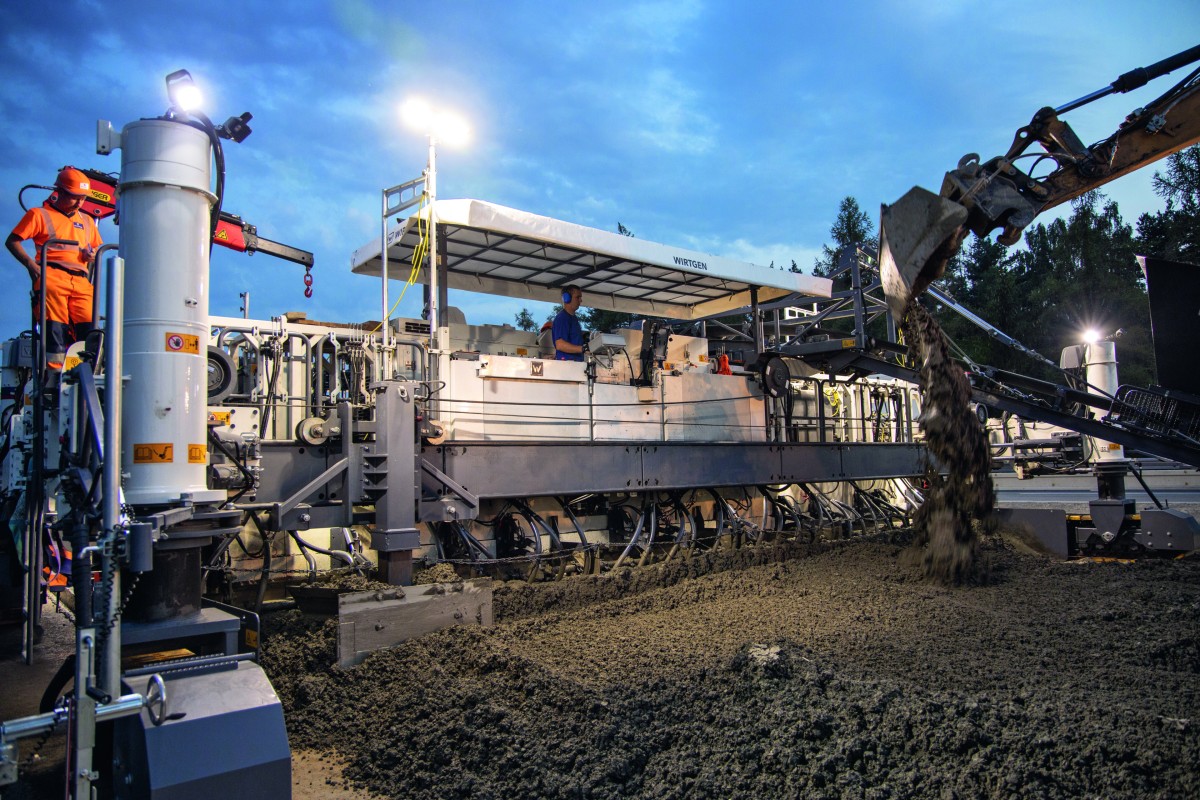
Road Machinery
31/10/2024
Wirtgen: Concrete paving with inset slipform pavers
Wirtgen has been offering machines for inset slipform paving...
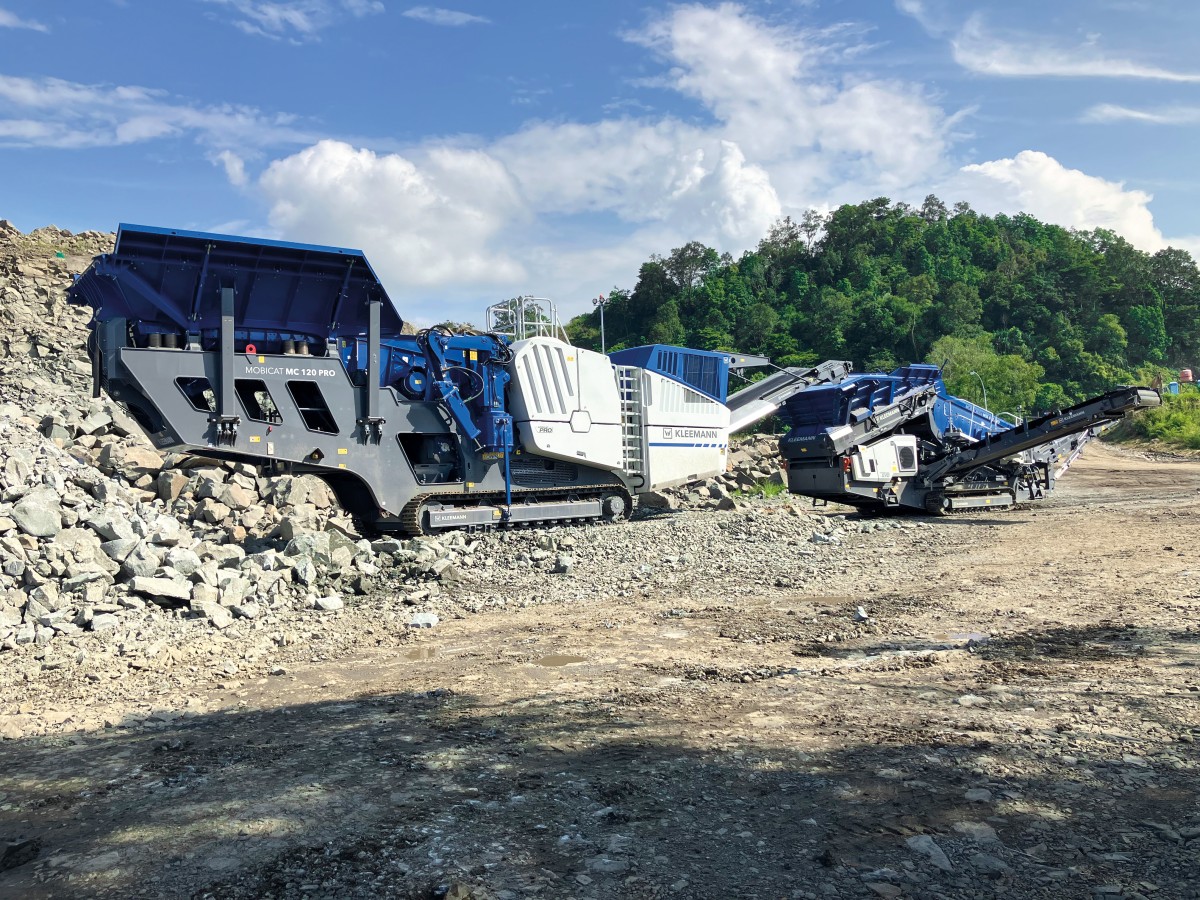
Earthmoving Machinery
28/10/2024
Kleemann: Andesite processing in Indonesia
A MOBICAT MC 120 PRO and a MOBISCREEN MSS 802 EVO are deploy...
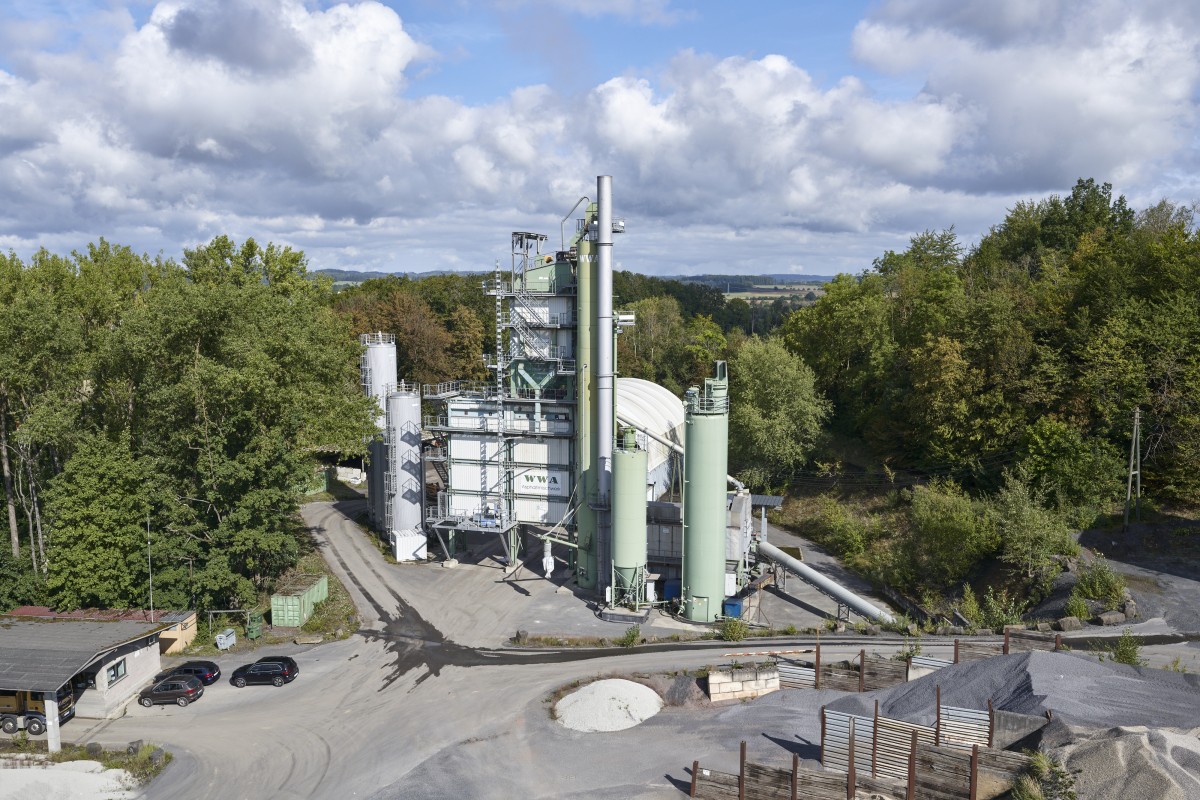
Earthmoving Machinery
24/10/2024
Benninghoven's REVOC system proven in practice
The REVOC Retrofit solution has been installed at an existin...
Road Machinery
01/10/2024
The Wirtgen Group at Paving Expo 2024
The Wirtgen Group presents groundbreaking technologies at Pa...
Altri International
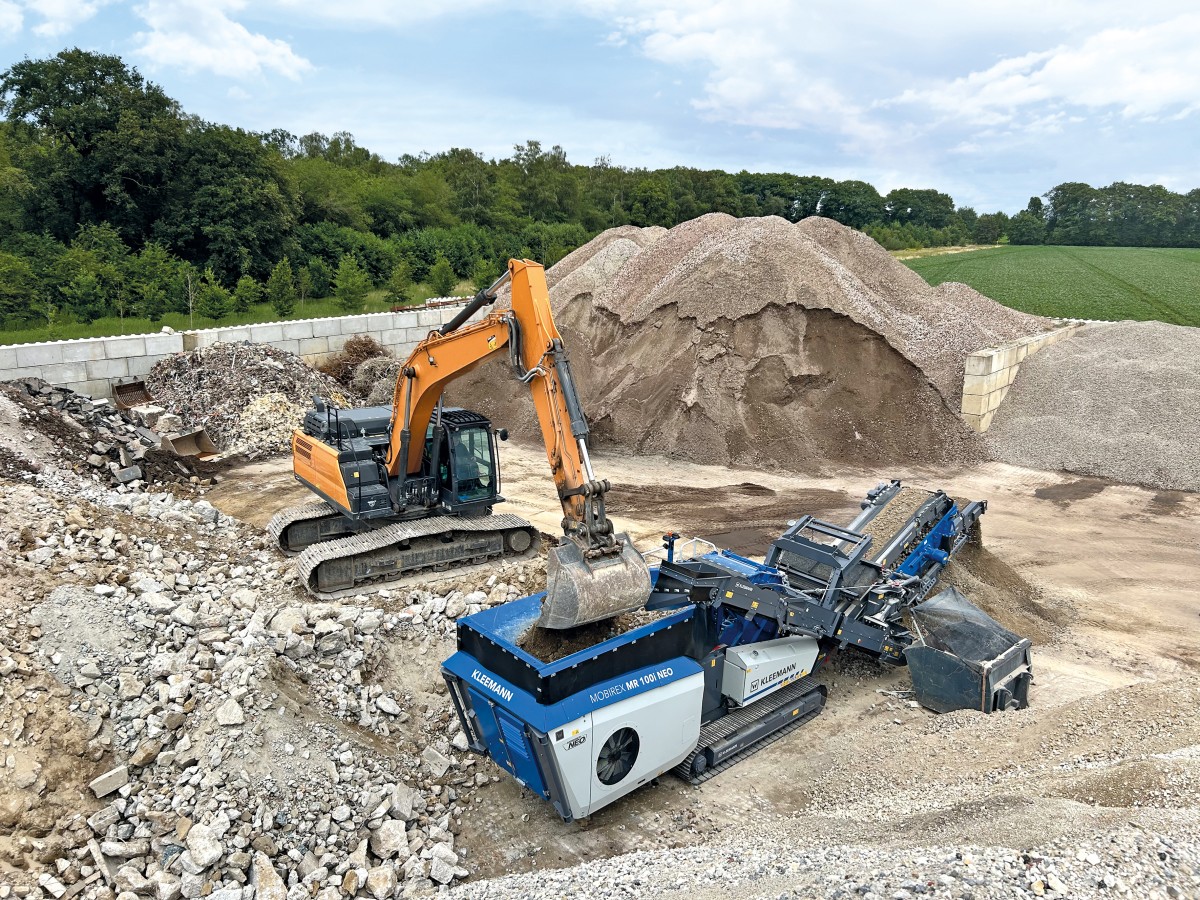
International
21/11/2024
Kleemann: New compact crusher used for recycling
Impact crusher MOBIREX MR 100i NEO impresses during operatio...
International
21/11/2024
SITECH partners with Royal Engineers to create poppy and demonstrate tech offering
The demostration involved creating a ground-level poppy desi...
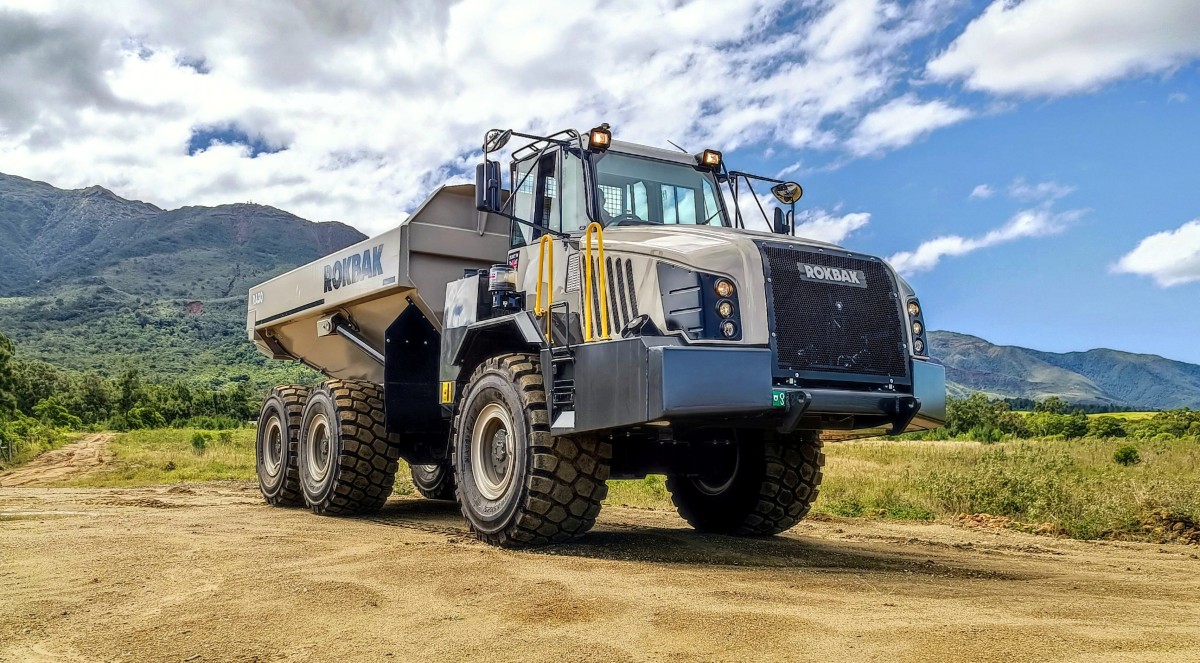
International
20/11/2024
Strong and stable RA30 trucks carry the weight at New Caledonian mine
Three Rokbak RA30 trucks are delivering exceptional durabili...
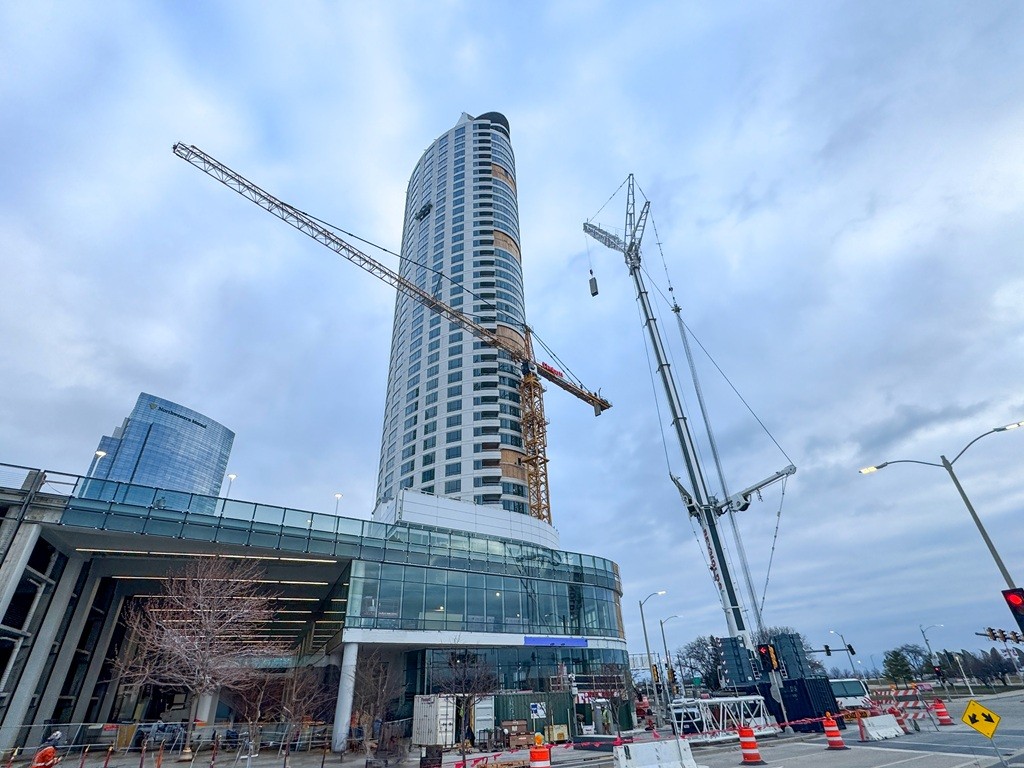
International
20/11/2024
Tadano AC 7.450-1 Performs Double Duty in Wisconsin
A cost-saving and versatile solution was already on site - a...
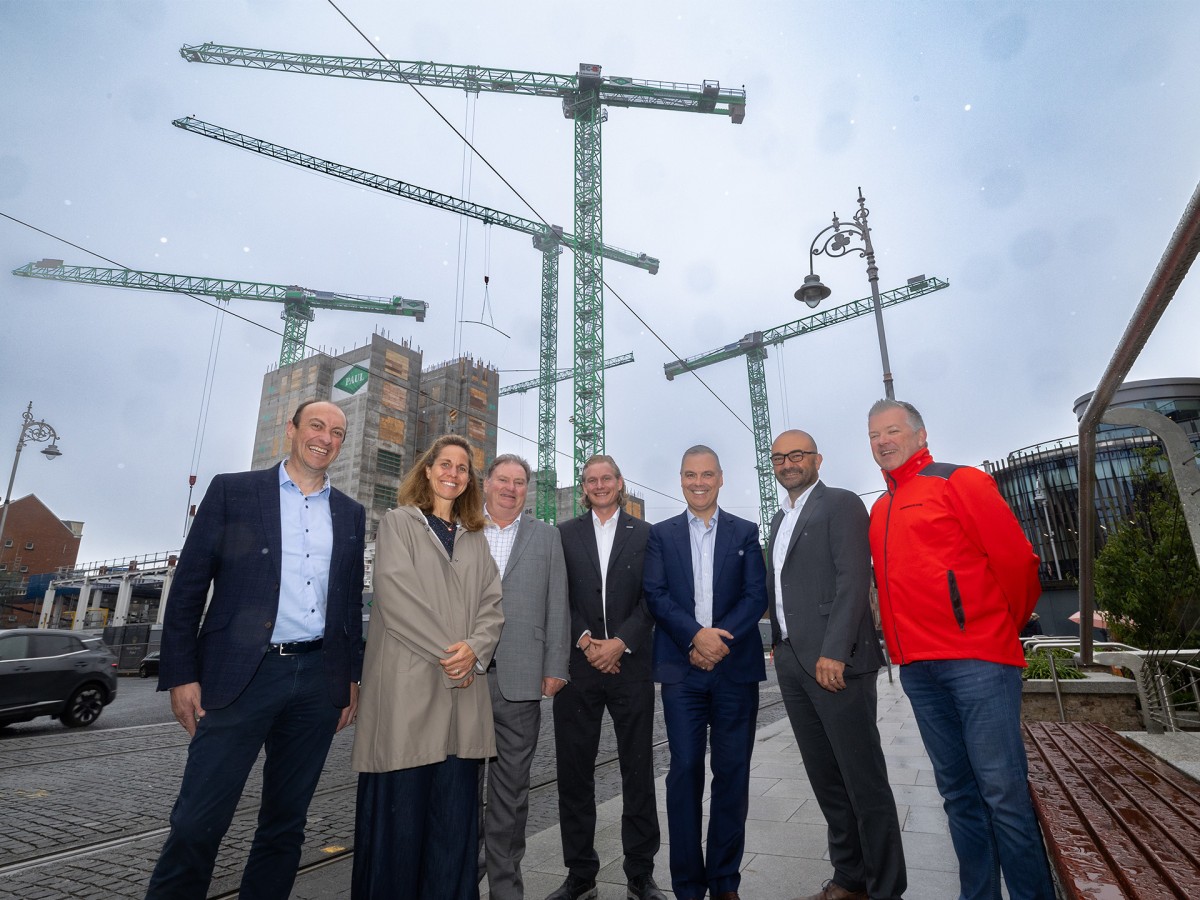
International
19/11/2024
Liebherr Tower Cranes and John Paul Construction celebrate 50 years of partnership
Irish construction company John Paul Construction is celebra...
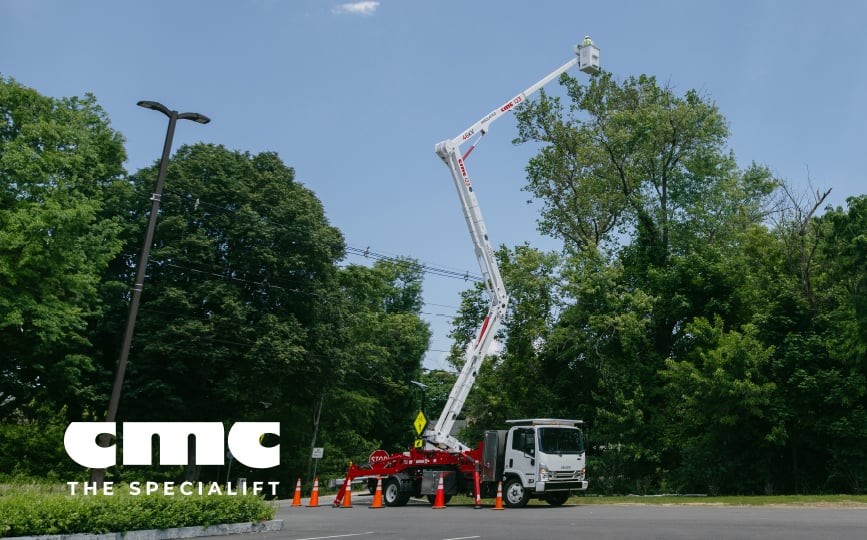
International
18/11/2024
The CMC i23 aerial platform: an example of high performances
CMC i23 is designed to maximise operational efficiency in al...