Home \ International \ Hamm: sustainable solutions at every level
Hamm: sustainable solutions at every level
20/05/2022
Pubblicato da Liliana Rebaglia
A year after receiving environmental certification according to ISO 14001, it is clear that Hamm AG, based in Tirschenreuth, is in a good position in terms of environmental protection.
For many years, compaction specialist Hamm has been actively promoting environmental protection through sustainable solutions, and is continuously reducing its carbon footprint. Achieving the ISO 14001 environmental certification at the end of 2020 marked a milestone.
Stefan Klumpp, member of the Executive Board of Hamm AG, describes the company's motivation: "Protecting the environment is vital for us. This applies not only to our operations as a manufacturing company, but also to our products. It goes without saying that we therefore comply with the statutory regulations. Through our environmental management system, we have also identified further potential for improvement that will enable us to reduce our consumption of resources and energy."
One of the flagship projects to date is the construction of a geothermal system. It has been heating and cooling the administration building since 2013, yielding savings of around 86 t of CO2 per year. At the plant in Tirschenreuth, the energy demand for lighting was almost halved in 2019 by switching to LED lights. This also saves over 80 t of carbon dioxide every year. Optimisations in the compressed air cycle also reduce the electricity/energy demand by 50,000 kWh. That corresponds to close to 5 t of CO2.
Since 2018, an environmental protection manager has been advancing the further minimisation of raw material and energy consumption, waste, packaging and emissions of solvents (VOCs) and placing all divisions under the magnifying glass. In this way, Hamm is improving its ecological footprint through large-scale measures as well as numerous finely detailed projects. At the moment, the energy demand for heating is also being drastically reduced, as well as the consumption of fresh water in production. There are also very high standards regarding waste water and low noise emissions from the plant. Alongside this, paperless production is to be introduced in the near future.
Waste is also a key focus. "By implementing numerous individual measures, by 2023 we will have reduced the waste per produced machine by approximately 20% compared with 2019," explains plant manager Dirk Pressgott. In production, an innovative painting process reduces the amount of paints and solvents used while offering the same paint quality. Hamm also recycles the solvents used for cleaning the painting systems. Internal logistics also saves energy by optimising routes and also uses quiet electric forklift trucks. Shortly before the rollers leave the plant, the brake energy is recovered via recuperation at the test bench, which all machines pass.
In general, "intelligent solutions instead of materials" applies in purchasing and logistics at Hamm. Special transport racks therefore render much of the packaging superfluous. And, thanks to a 4PL strategy, there are virtually no empty runs when supplying purchased parts and semi-finished products. In addition to these measures, suppliers are selected based on their environmental certification and training of employees with a view to environmental protection. Through dialogue with the Design and Production departments, Hamm has also been continuously reducing excess packaging and optimising transport capacity for many years. Recycled plastics are also used wherever possible for constructing rollers.
With regard to products, Hamm follows the objective of "developing low-consumption machinery and machine control systems that ensure an efficient and, therefore, resource-friendly work process on the construction site," explains Dr Axel Römer, Head of Research and Development. Specific examples of this are compaction with oscillation, which emits little noise and conserves resources; process optimisation through digital tools and networking; and consumption-reducing technologies in the area of the power train. Hamm rollers can also be operated with non-fossil fuels such as biodiesel or hydrotreated vegetable oil (HVO). Today, many machines can already work with these types of fuels, and applications are being expanded. Biodegradable hydraulic oils are also part of the standard supply range.
Durable products are especially sustainable. This is where Hamm's telematics system comes in to play, as the service life of the rollers is extended through regular maintenance – and with optimal availability. The long service life of Hamm rollers is also reflected in the spare part philosophy. Hamm still supplies customers with spare parts for all models ever built. Moreover, most spare parts can be ordered separately – not just in assemblies.
Hamm relies on sustainable materials when shipping spare parts. Films and plastic are avoided as far as possible, and polystyrene packing chips are taboo. Instead, Hamm packages spare parts in cardboard; packing paper acts as a fill material and padding. Moreover, Hamm receives a large portion of spare parts and wear parts already ready to ship with the corresponding packaging. Material-intensive repackaging – quite common in the sector – is therefore not required. A shift can also be seen in machine documentation – it has been completely moved to data carriers. In its in-house documentation centre, Hamm prints documents only upon request based on the "print on demand" principle. It has therefore been possible to reduce the need for paper by more than 70%.

Ultime notizie di Wirtgen Macchine
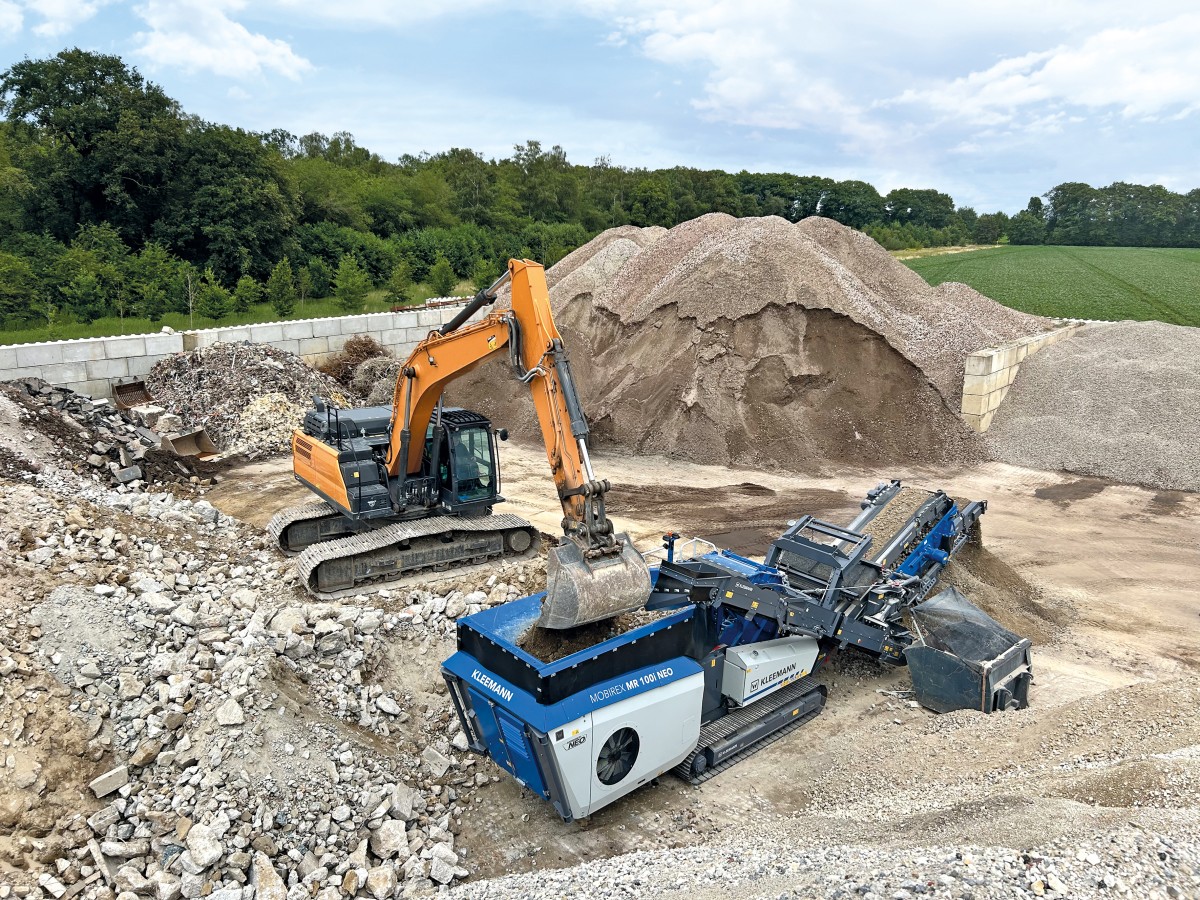
Earthmoving Machinery
21/11/2024
Kleemann: New compact crusher used for recycling
Impact crusher MOBIREX MR 100i NEO impresses during operatio...
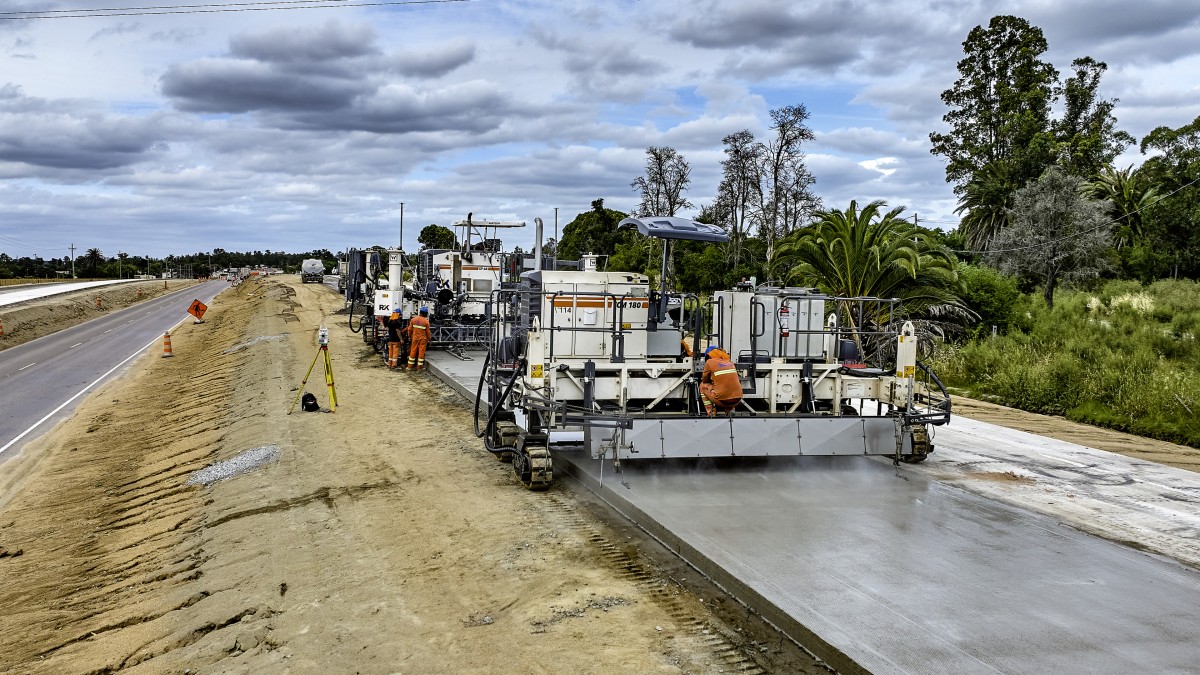
Road Machinery
04/11/2024
Wirtgen: Widening of the Ruta 5 highway from Montevideo to the Brazilian Border
Efficient concrete paving solutions from Wirtgen ensure the...
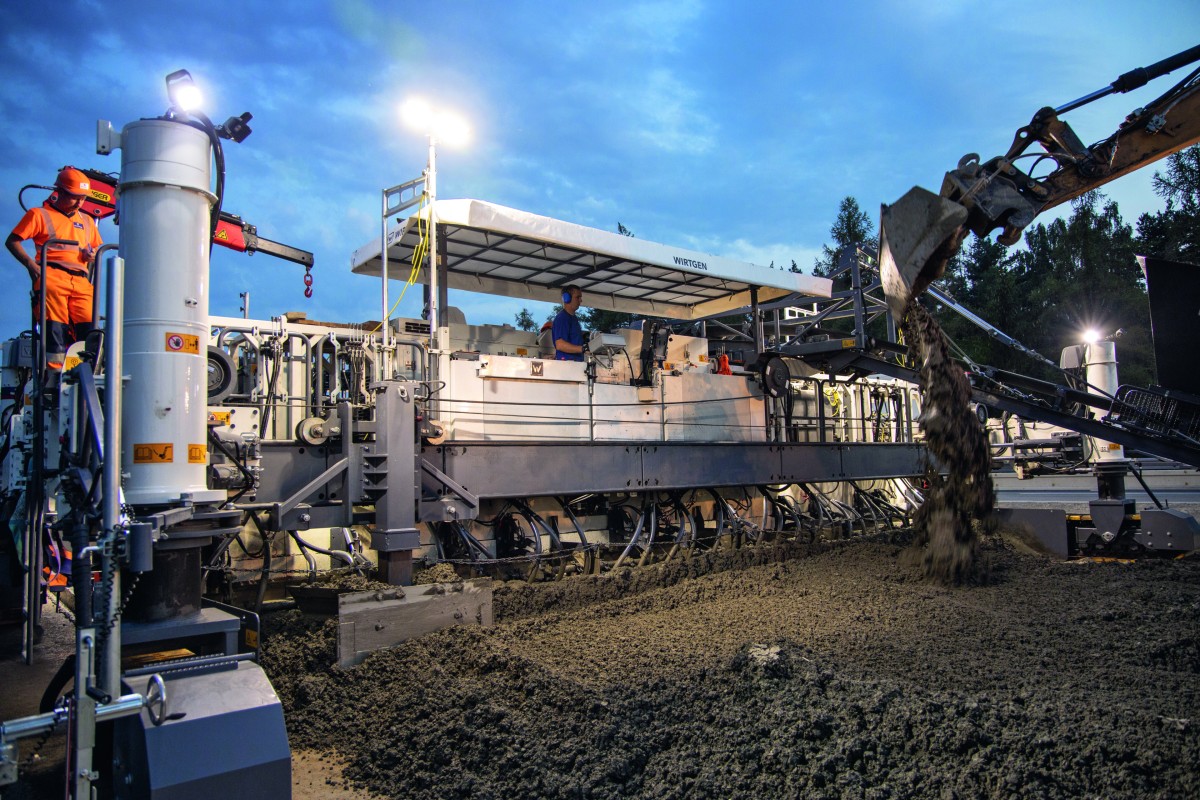
Road Machinery
31/10/2024
Wirtgen: Concrete paving with inset slipform pavers
Wirtgen has been offering machines for inset slipform paving...
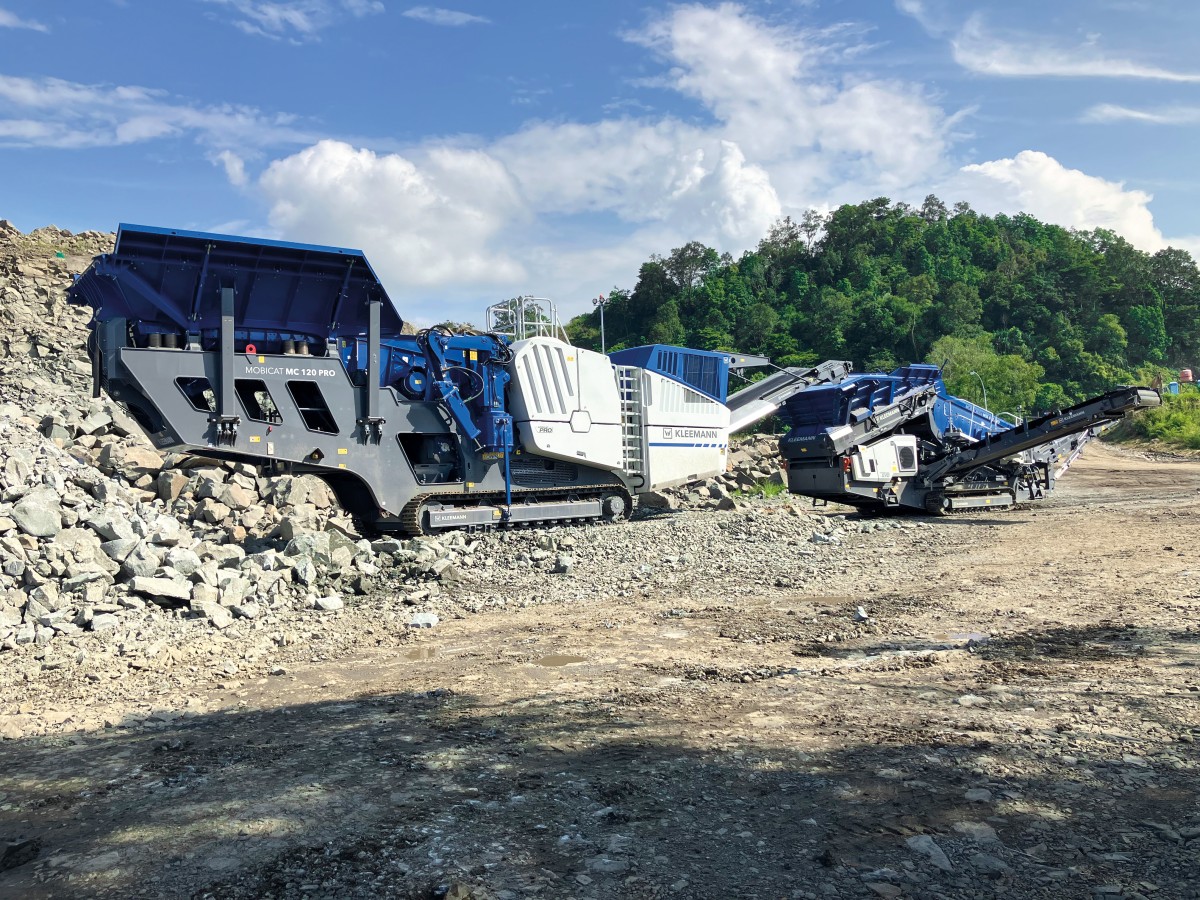
Earthmoving Machinery
28/10/2024
Kleemann: Andesite processing in Indonesia
A MOBICAT MC 120 PRO and a MOBISCREEN MSS 802 EVO are deploy...
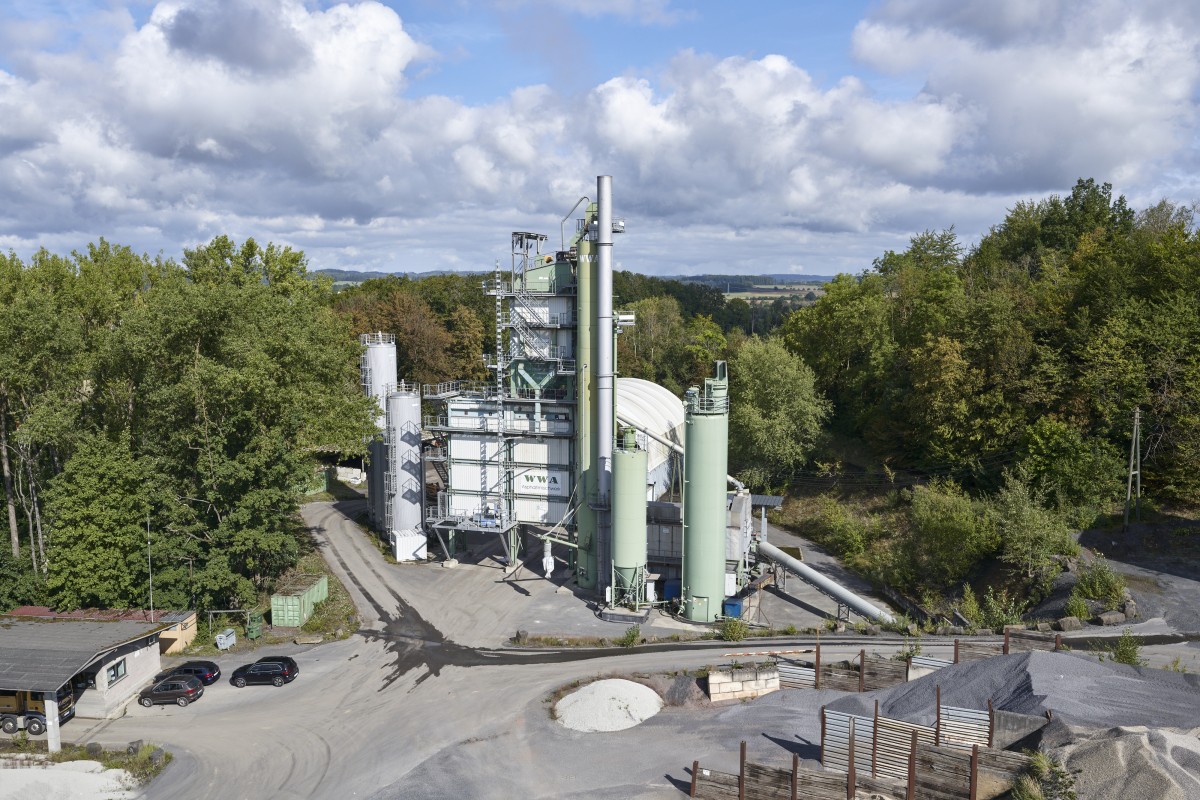
Earthmoving Machinery
24/10/2024
Benninghoven's REVOC system proven in practice
The REVOC Retrofit solution has been installed at an existin...
Road Machinery
01/10/2024
The Wirtgen Group at Paving Expo 2024
The Wirtgen Group presents groundbreaking technologies at Pa...
Altri International
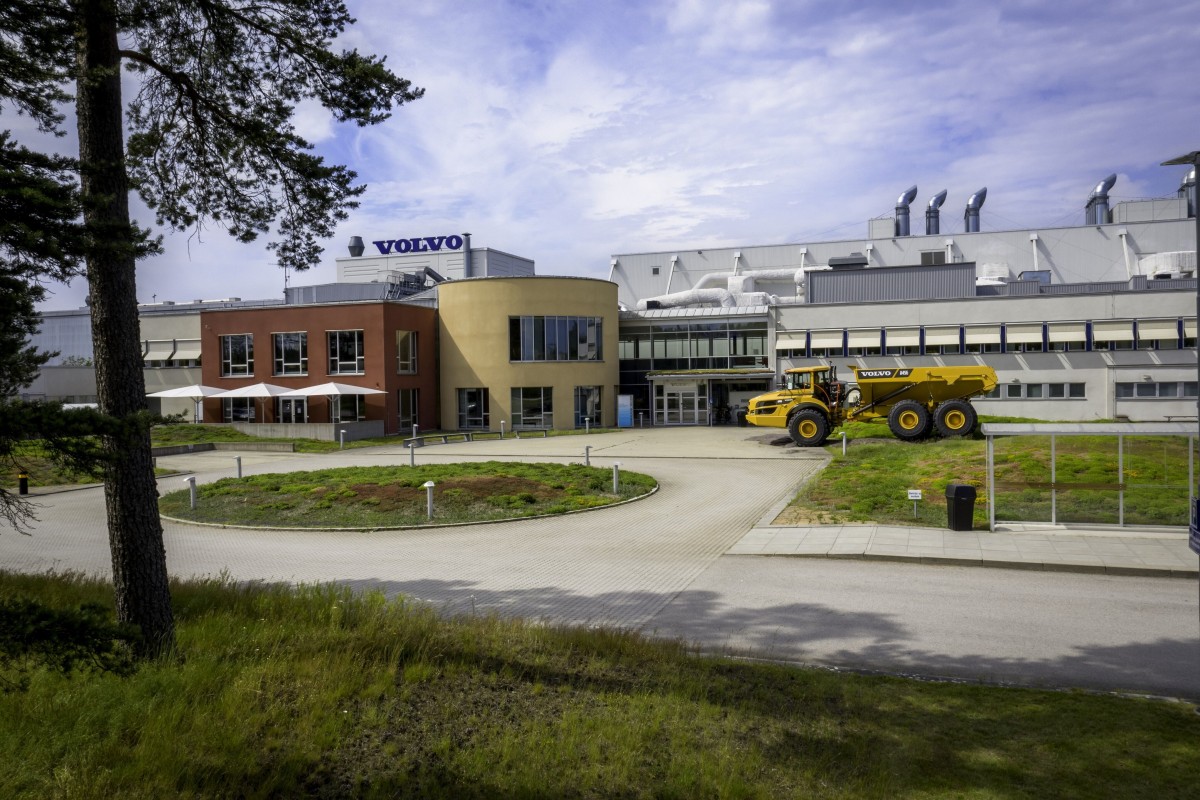
International
27/11/2024
Home of Volvo Construction Equipment’s pioneering articulated haulers advances to Climate Efficient Site
As one of the construction industry’s most active drivers of...
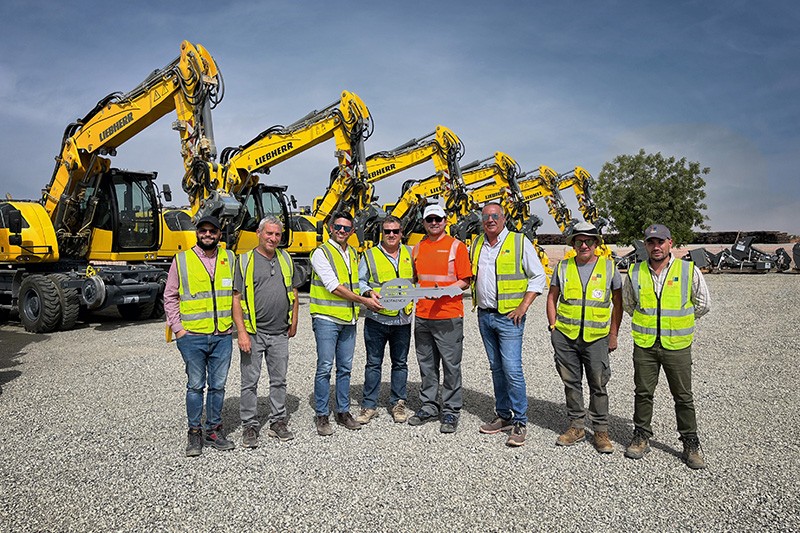
International
26/11/2024
Mota-Engil orders 10 Liebherr railroad excavators for a major project in West Africa
The Portuguese construction company Mota-Engil has once agai...
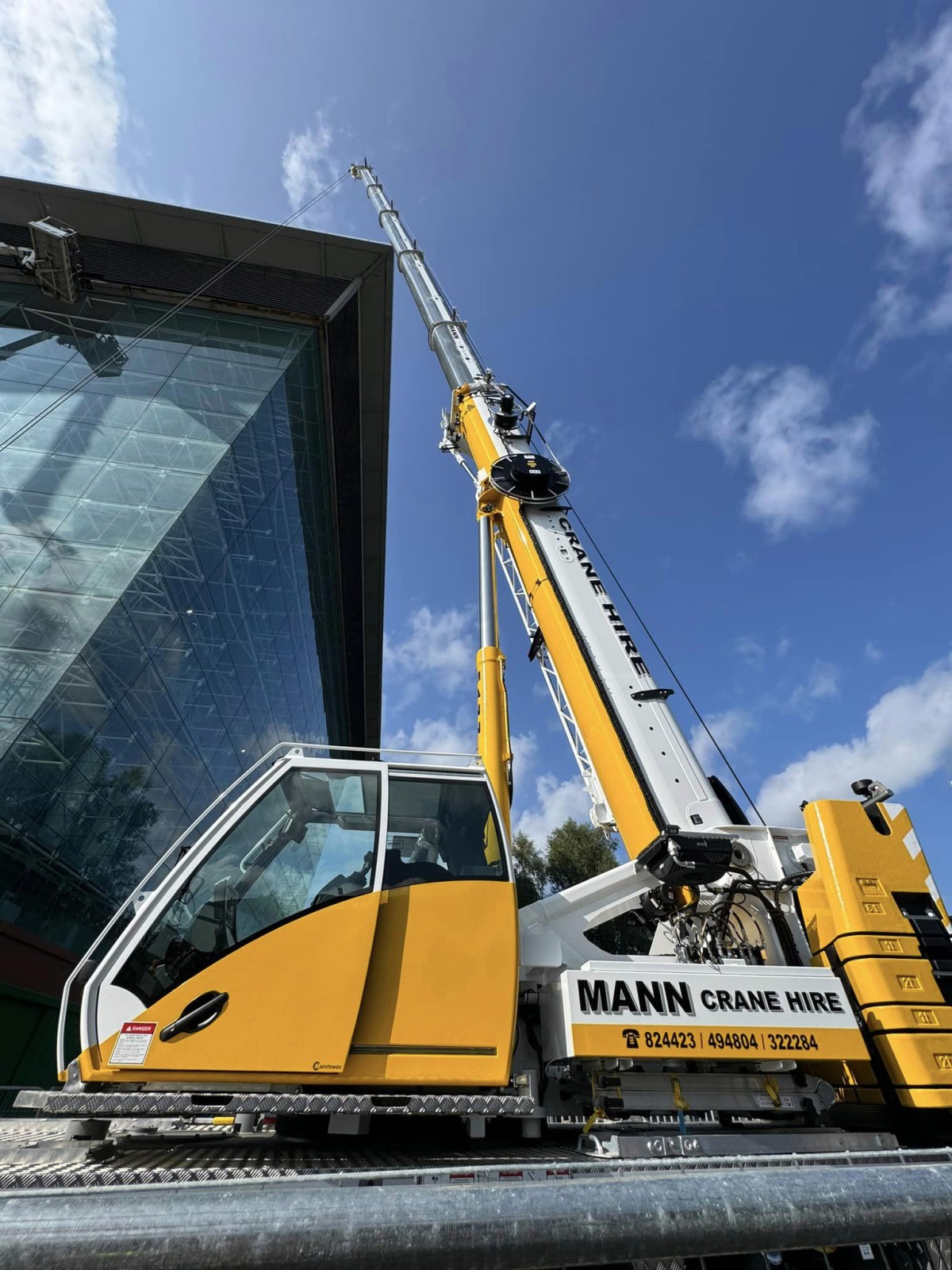
International
25/11/2024
New Grove GMK3060L-1 drives busy schedule for Mann Crane Hire
• Mann Crane Hire selected the GMK3060L-1 for its class-lead...
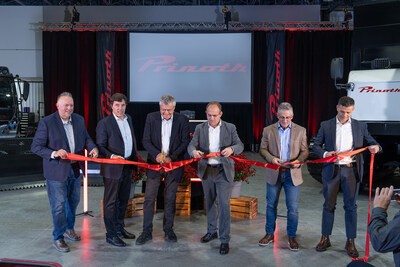
International
25/11/2024
Prinoth Unveils Expanded Production Facility in Granby, Canada
Prinoth held an event to announce the official opening of it...
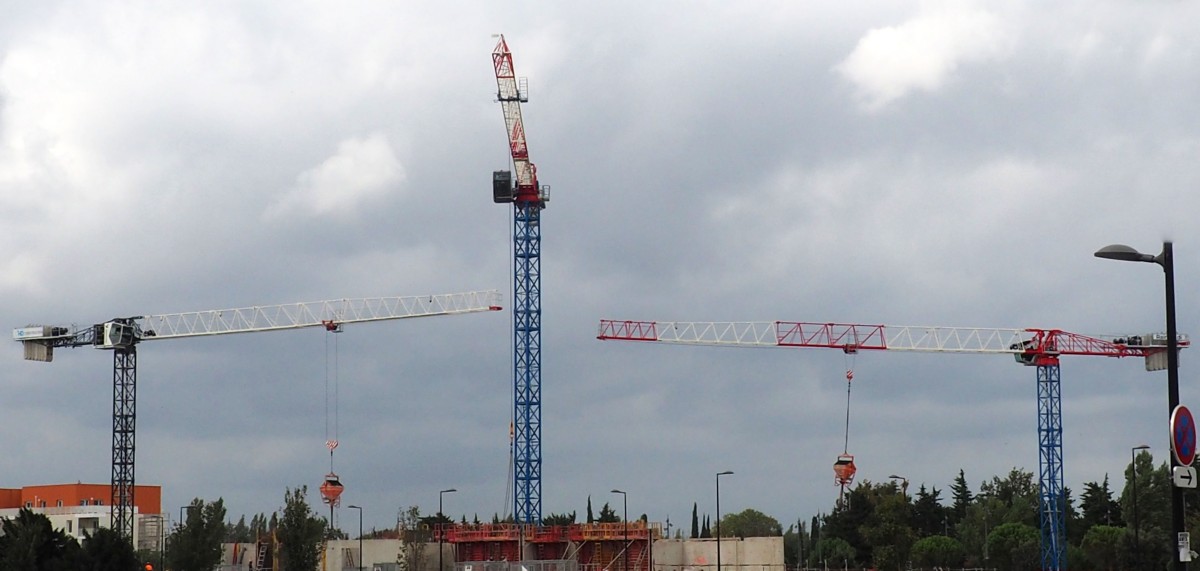
International
23/11/2024
GPMat International takes delivery of two Raimondi T147s residential development in the South of France
- Official agent of France expands its product lineup with t...
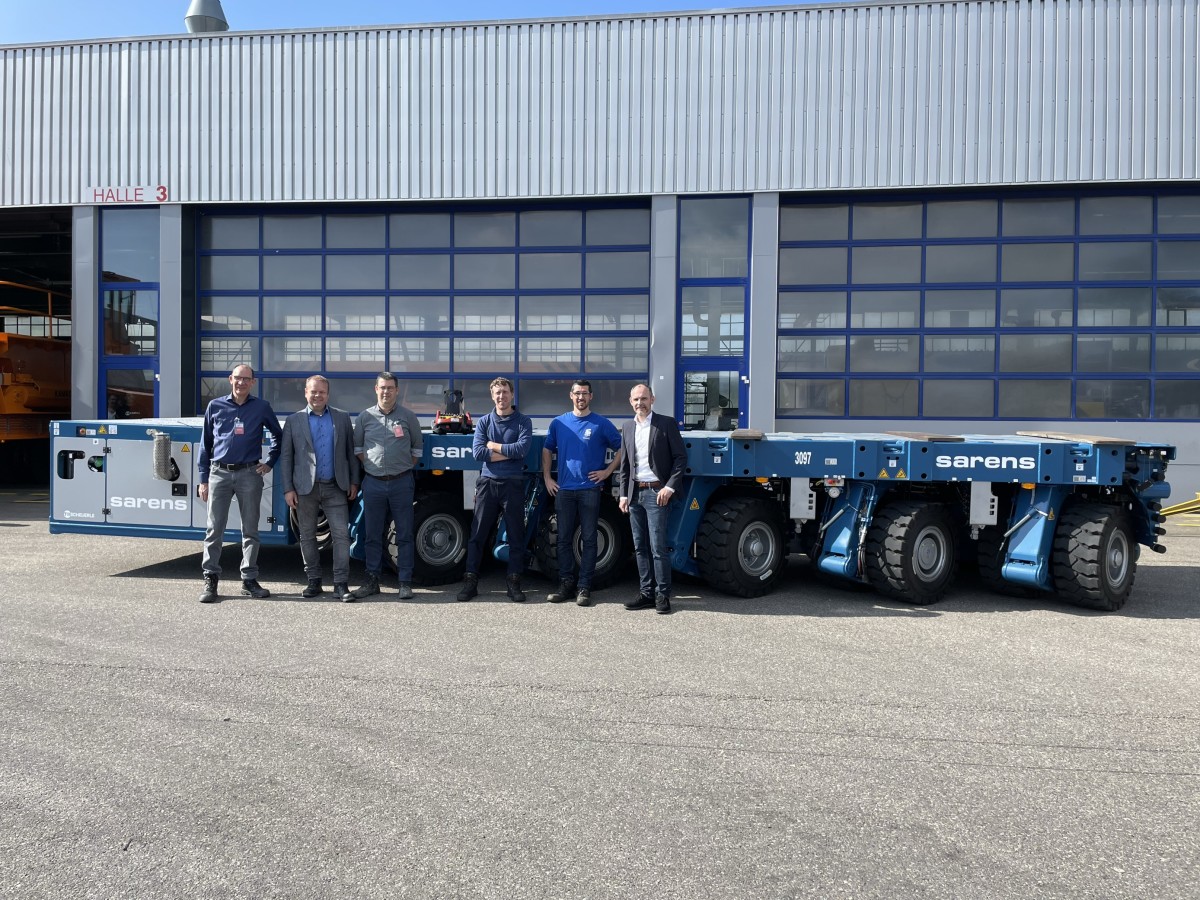
International
22/11/2024
Sarens acquires additional SCHEUERLE SPMT K24 modules
renowned for its expertise in crane rental services, heavy l...