Home \ International \ Liebherr presents the new 6-axle crane LTM 1400-6.1
Liebherr presents the new 6-axle crane LTM 1400-6.1
20/06/2024
Pubblicato da Ettore Zanatta
The new crane LTM 1400-6.1 from Liebherr is characterised by strong lifting capacities and a 70-metre telescopic boom.
Liebherr's engineers have succeeded in getting the most out of a 6-axle crane during the product development process. The LTM 1400-6.1 achieves significantly higher lifting capacities than its predecessor, the LTM 1350-6.1, and is now the market leader worldwide. By successfully integrating its latest engineering expertise and innovative systems into this mobile crane, Liebherr has created an extremely powerful yet easy-to-handle machine.
In addition to achieving outstanding performance data, Liebherr has focused on simple and fast set-up processes during development of the new crane. The entire workflow leading up to full operational readiness on the construction site has been designed with maximum simplicity in mind. There are major differences to the predecessor model, the LTM 1350-6.1, particularly in terms of the assembly process for the Y-guying system. With just one self-assembly lift, the LTM 1400-6.1 places the guying system on the chassis, where it is then pinned in place. The hydraulic quick coupling closes automatically when the boom is luffed down between the two Y-frames. The electrical connection is established with one final movement and the telescopic boom with Y-guying is ready for use in just a few minutes. Various lattice jibs enable the new crane to work efficiently in a wide range of applications. The fixed lattice jib extends the telescopic boom by up to 45.5 metres and can be mounted at an angle of 0°, 10°, 20° and 40°. As an option, the fixed jib can be adjusted between 0° and 40°. The luffing lattice jib, with a length ranging from 14 to 80.5 metres, delivers maximum height, radius and performance.
As with its predecessor, the total available ballast for the new LTM 1400-6.1 consists of 100 tonnes of basic ballast and 40 tonnes of additional ballast. The hydraulic ballasting device is integrated in the counterweight frame – ballast assembly is simple, quick and does not require an auxiliary crane. The VarioBallast system is fundamentally different to the one found on the predecessor model. The 140 tonnes of total ballast can now be set to an enormous radius of 7.7 metres to achieve the maximum lifting capacity. In confined spaces, the ballast radius can be reduced to 5.6 metres. The counterweight plates are compatible with those found on other large Liebherr cranes – a major advantage for the crane operator in terms of both economy and logistics. The variable VarioBase supporting system ensures additional versatility. Here too, Liebherr engineers have come up with a new development: in addition to the option of flexibly using the predefined support positions with pinning options of 0%, 25%, 50%, 75% and 100%, the sliding beams can now also be freely extended between 0% and 50%. Until now, this was only possible on mobile cranes with up to five axles.
Unlike its predecessor, the new 400-tonne crane is powered by the Liebherr single-engine concept and a mechanical drive for the superstructure, which results in better economy. An eight-cylinder Liebherr diesel engine with 455 kW / 619 h.p. and 3,067 Nm of torque ensures a powerful travel drive. Liebherr has developed different driving conditions to ensure worldwide, economical mobility. With an axle load of 12 tonnes, the LTM 1400-6.1 with telescopic boom and detachable hook block has an overall length of 17.8 metres. On the construction site, the 400-tonne machine can be driven with 10 tonnes of ballast, a three-line hook block and Y-guying with an axle load of less than 16.5 tonnes. Equipment can be removed for road journeys requiring lower axle loads.
Another new feature is the installation of various driver assistance systems to increase road safety, especially for vulnerable road users such as pedestrians and cyclists. For example, the Blind Spot Information System warns the crane driver when someone is in the vehicle's blind spot, particularly when the crane is turning. The moving off information system also provides a visual and acoustic warning if someone is in front of the crane. By monitoring the areas around the crane while it is moving, a significant increase in safety is achieved despite the presence of components that restrict visibility, such as the boom and hook block.

Ultime notizie di Liebherr Italia
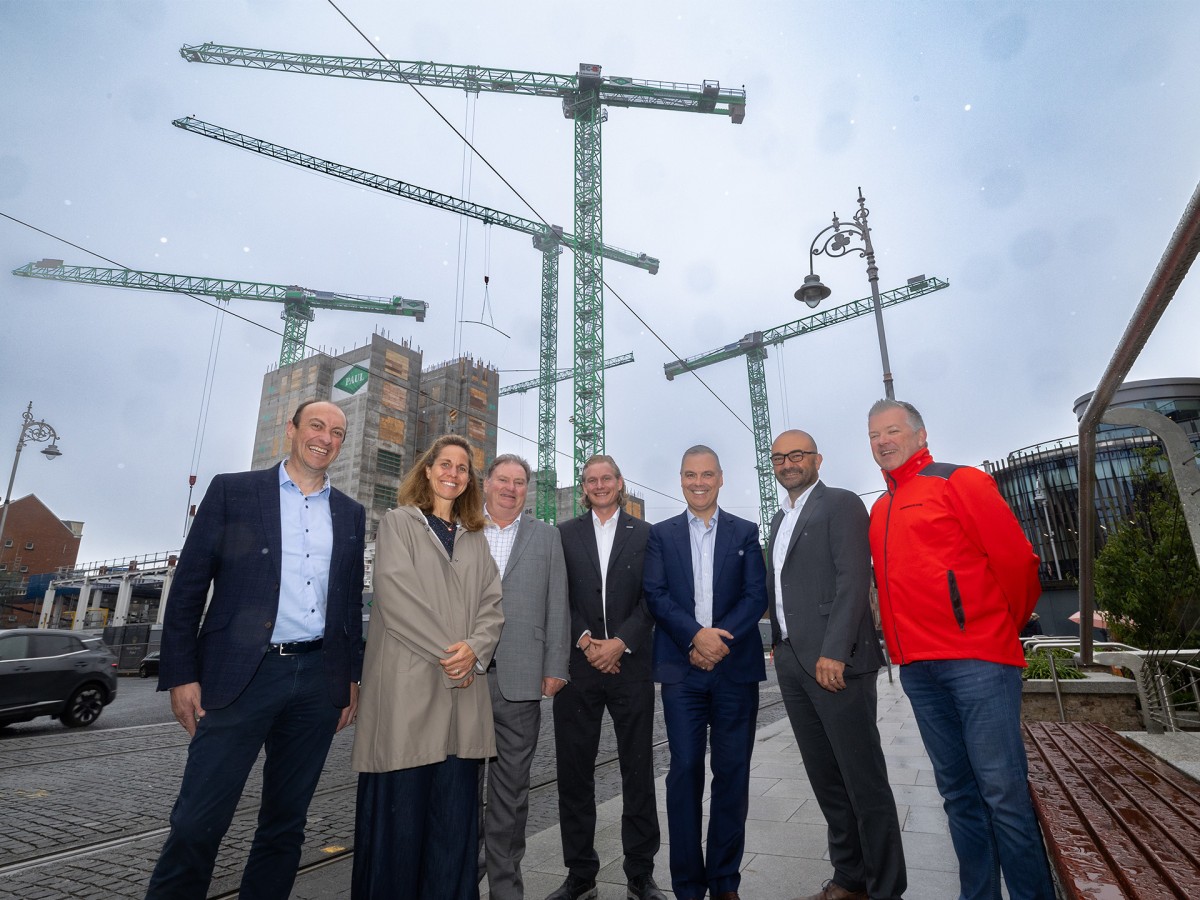
Lifting
19/11/2024
Liebherr Tower Cranes and John Paul Construction celebrate 50 years of partnership
Irish construction company John Paul Construction is celebra...

Lifting
29/10/2024
Wertz-Autokrane takes delivery of Liebherr LTM 1110-5.2 mobile crane
– The new 110-tonne crane complements the Wertz crane fleet...
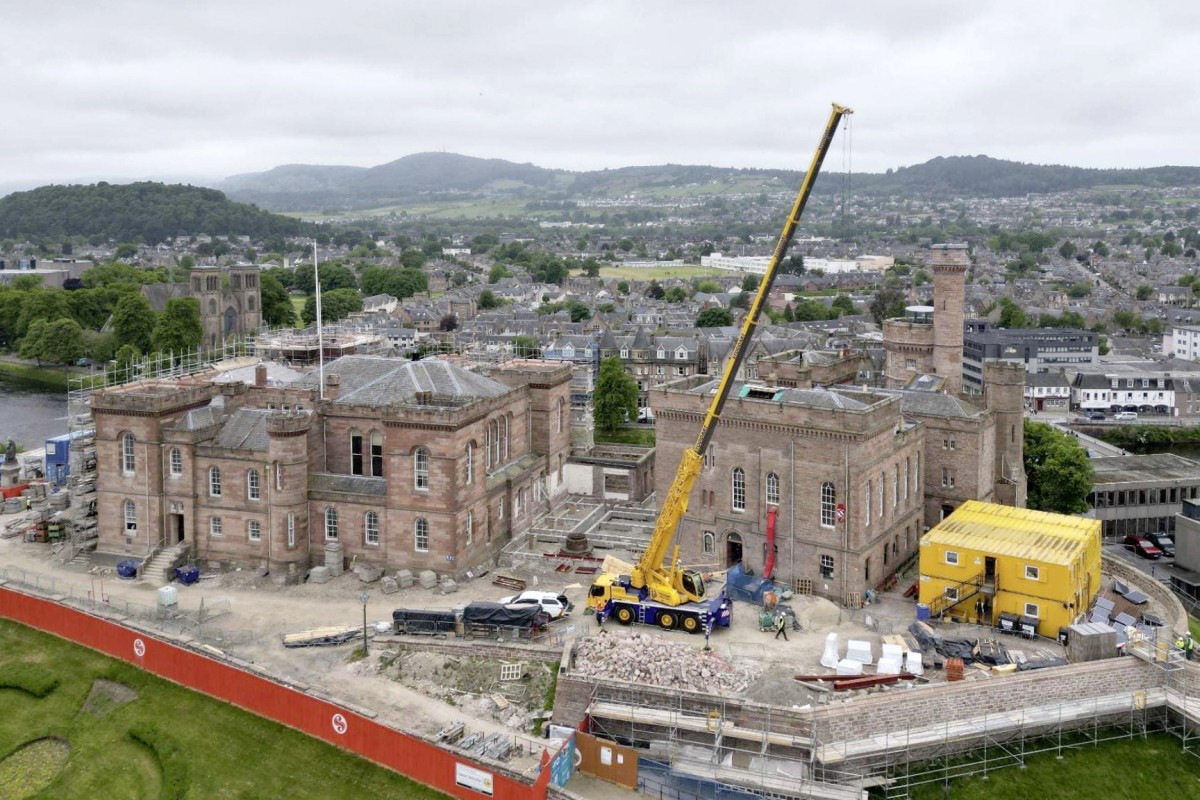
Lifting
23/10/2024
New Liebherr mobile cranes for Scotland
To mark its 20th anniversary, Stoddart Crane Hire gave itsel...
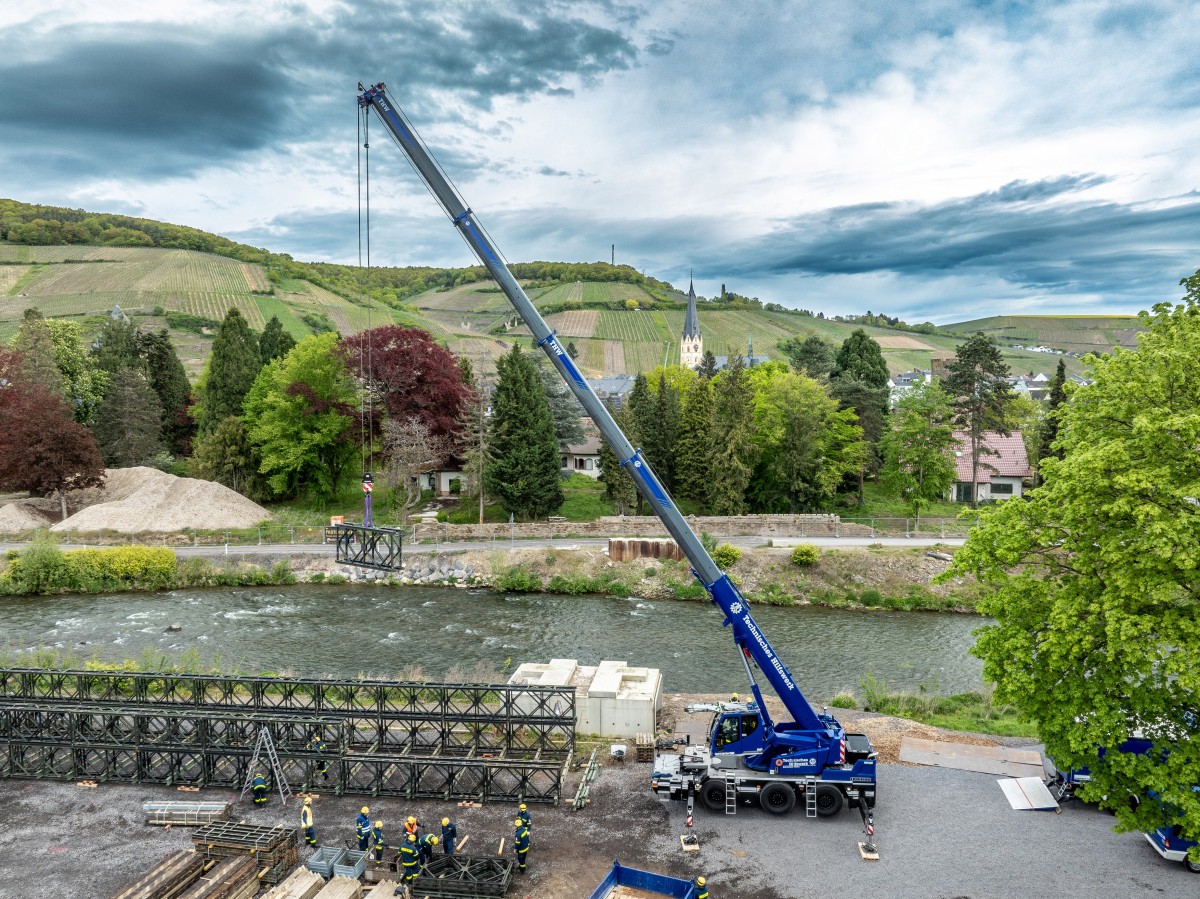
Lifting
17/10/2024
German Federal Agency for Technical Relief places its trust in Liebherr compact cranes
The German Federal Agency for Technical Relief (THW) placed...
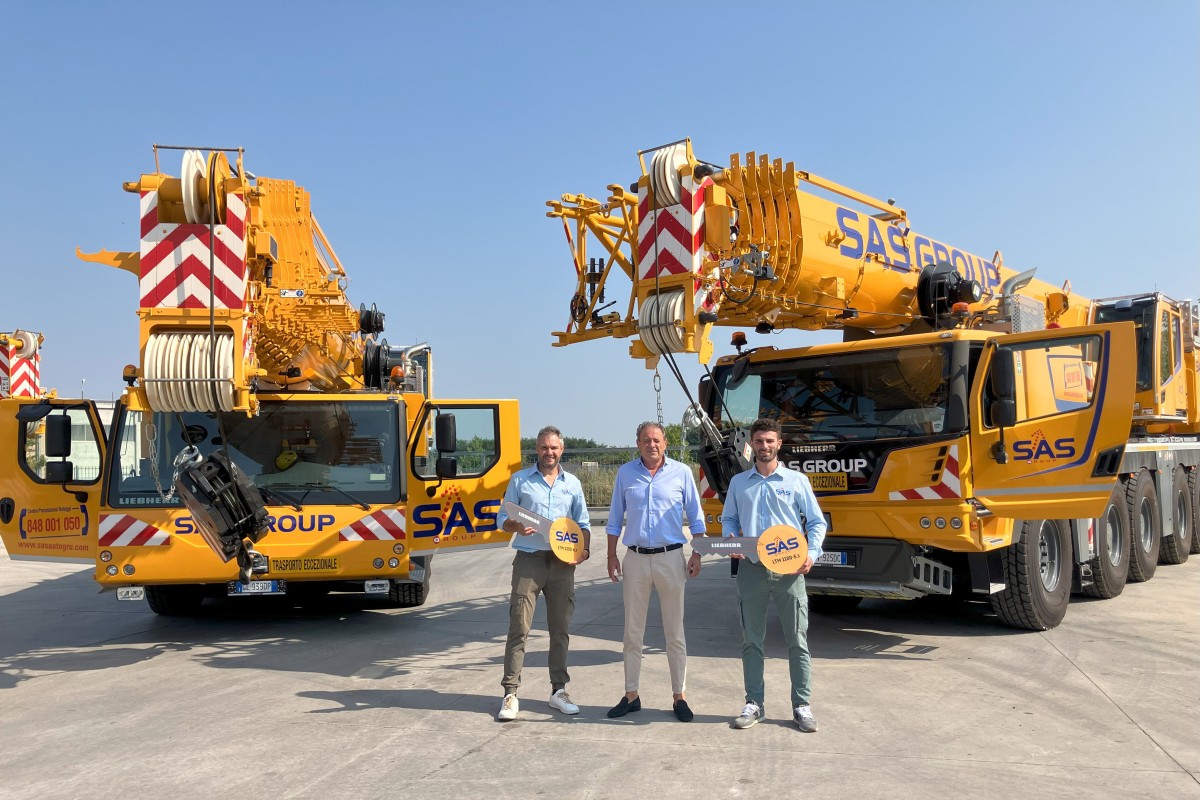
Lifting
14/10/2024
S.A.S Group expands Liebherr crane fleet
S.A.S Group expanded its Liebherr crane fleet with LTM 1300-...
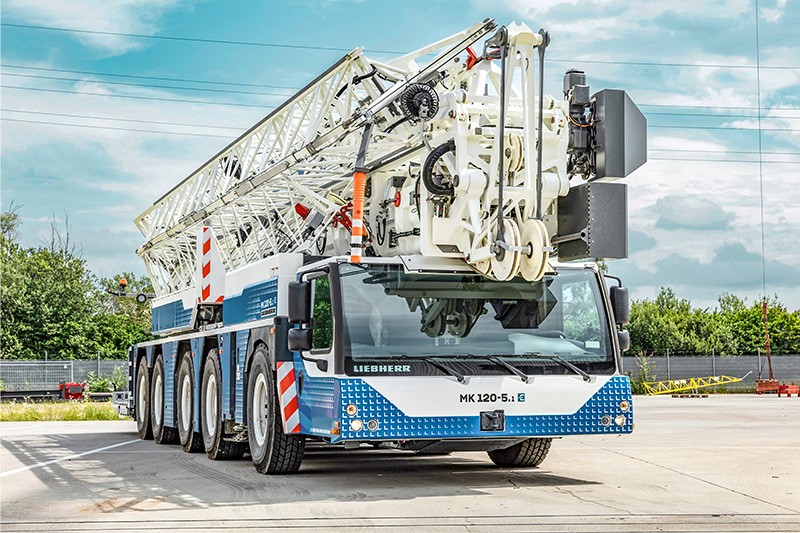
Lifting
04/10/2024
Liebherr’s mobile construction crane range is expanding
MK 120-5.1, now available to order, is an agile five-axle mo...
Altri International
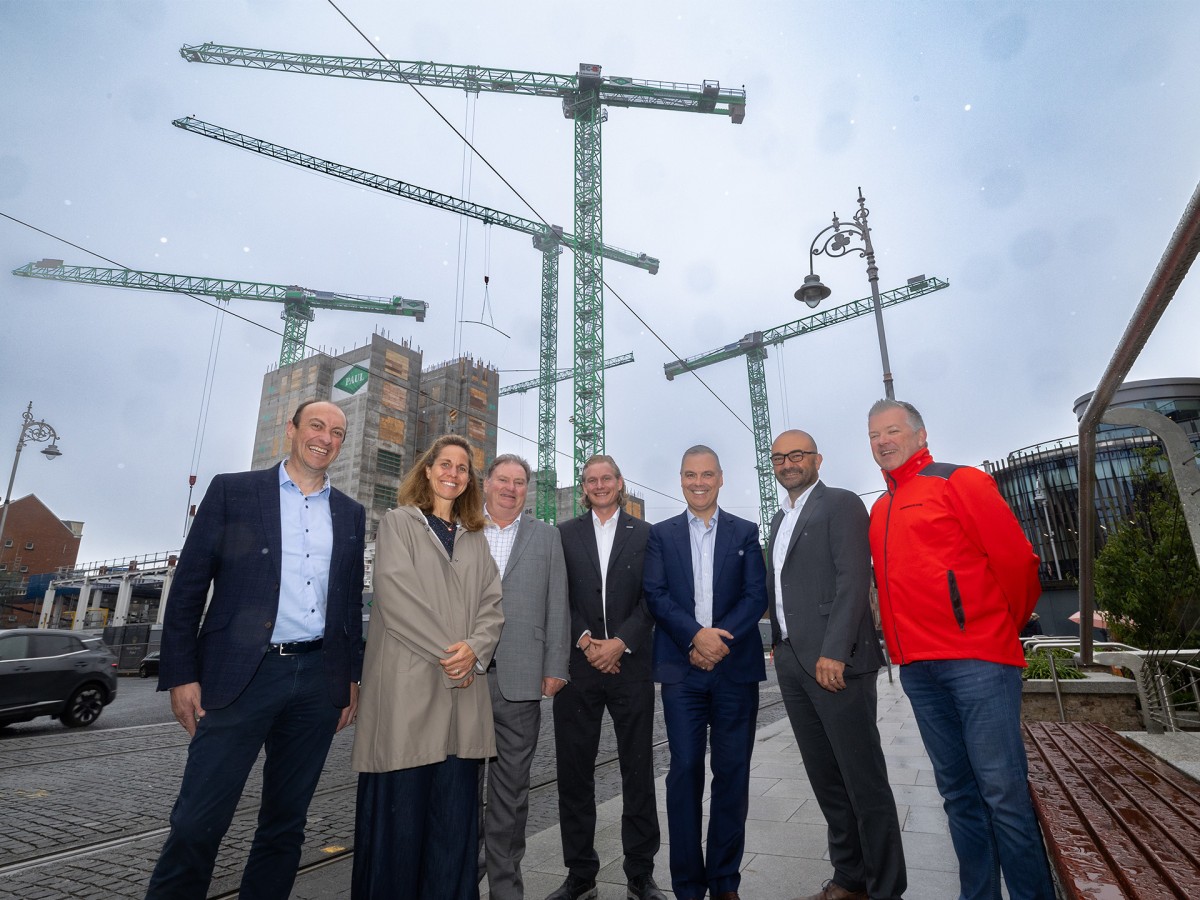
International
19/11/2024
Liebherr Tower Cranes and John Paul Construction celebrate 50 years of partnership
Irish construction company John Paul Construction is celebra...
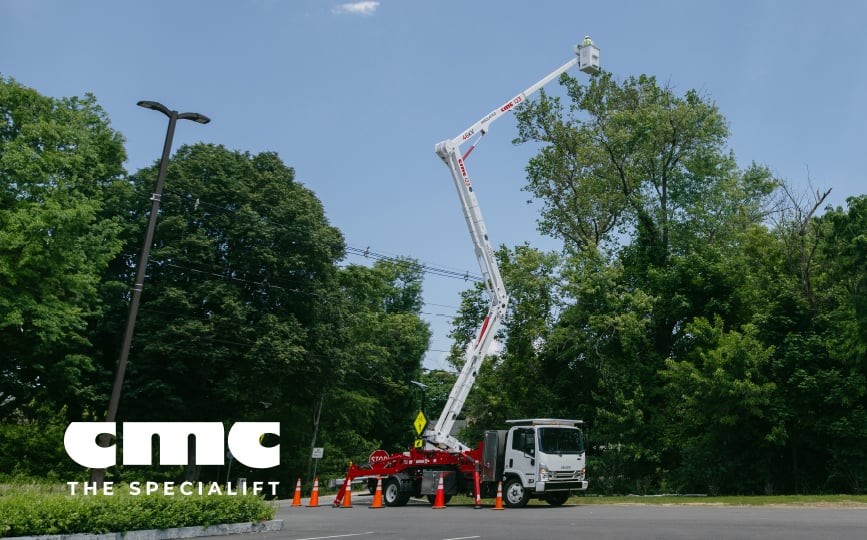
International
18/11/2024
The CMC i23 aerial platform: an example of high performances
CMC i23 is designed to maximise operational efficiency in al...
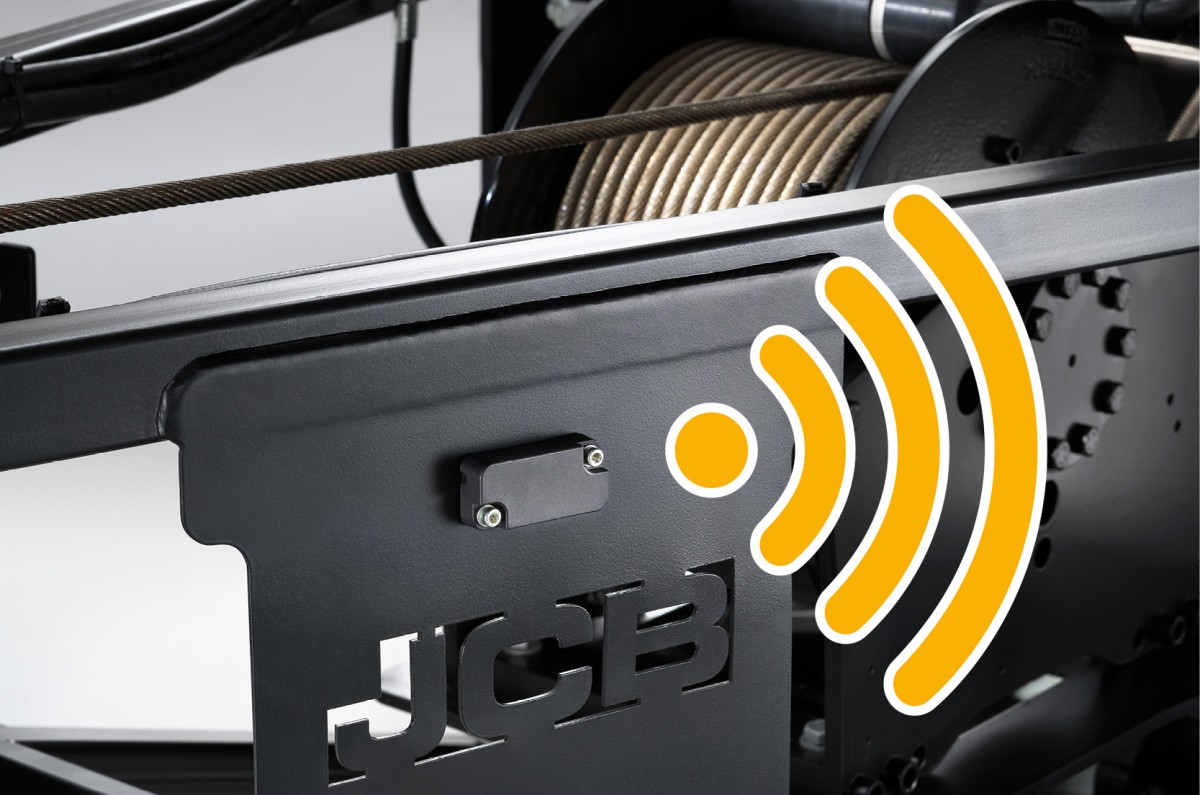
International
18/11/2024
JCB launches a new hi-tech tag offers versatile asset monitoring solution
JCB has launched a new product to help customers monitor the...
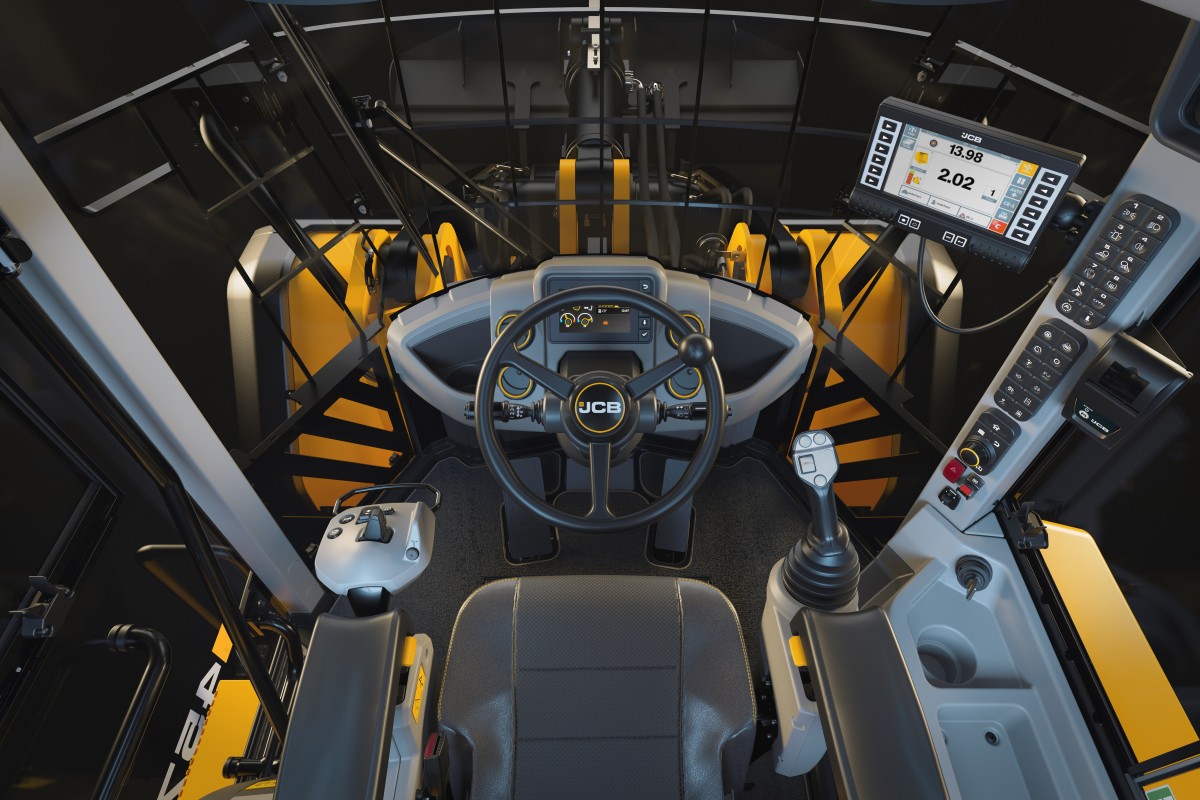
International
15/11/2024
JCB adds "Lever Steer" option to new controls package
JCB has developed a "Lever Steer" option for its large platf...
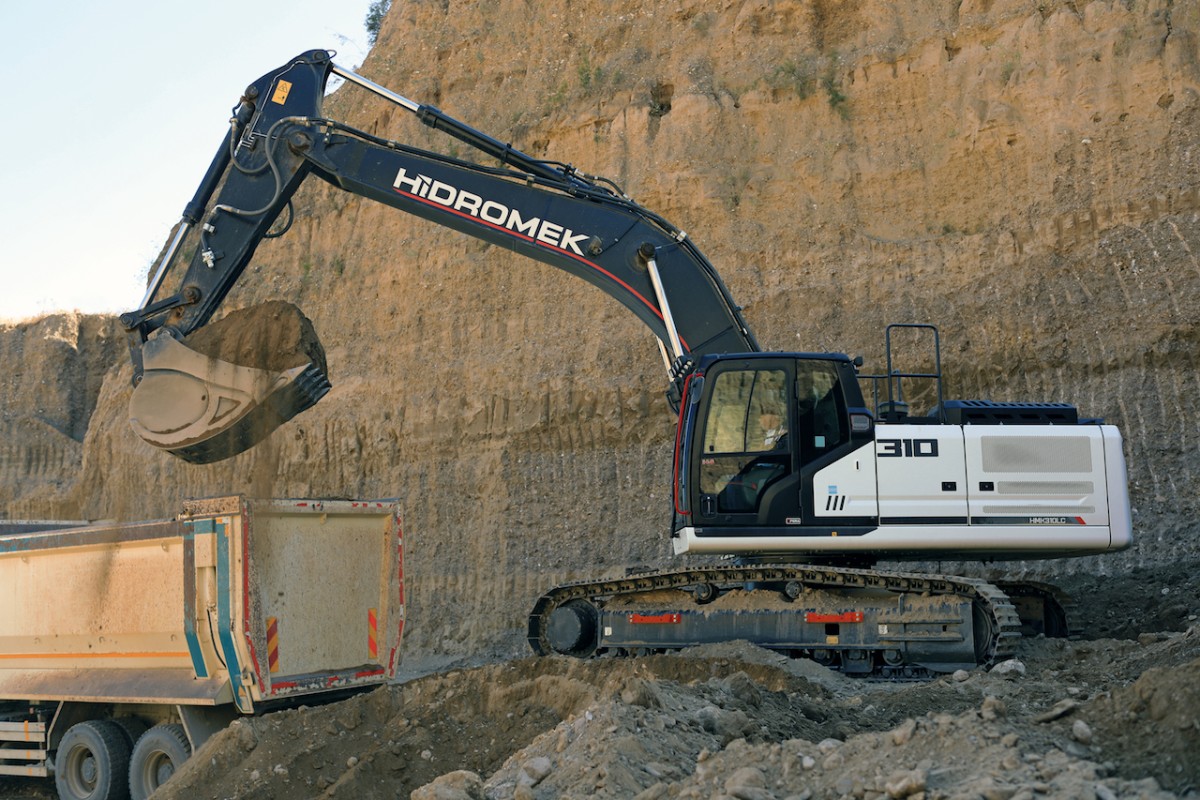
International
14/11/2024
Hidromek ıs ready for Bauma Chına wıth ıts ınnovatıve products
Hidromek will exhibit its HMK 200 C, HMK 310 LC crawler exca...
International
13/11/2024
CIFA publishes the first sustainability report of the Group and the concrete machinery field
Promoting the transformation of the entire sector by embodyi...