Home \ International \ Max Aicher Umwelt uses a Sennebogen 835 mobile material handler to process slag
Max Aicher Umwelt uses a Sennebogen 835 mobile material handler to process slag
01/04/2020
Pubblicato da Redazione
Indispensable to the steelworks and so to the recycling system too
Steelworks processes are finely coordinated and timed with each other - from the delivery of old scrap, to smelting and right through to loading steel products and processing slag, the system is reliant on constant functionality. Machine downtime means congestion in the flow of the system, or even a complete standstill. To prevent this happening, Max Aicher Umwelt in Meitingen, who processes slag for Lech-Stahlwerke, has gone with its long-standing, tried and tested method and acquired its third successive green machine, the new Sennebogen 835 mobile material handler.
For the last 34 years, Max Aicher Umwelt GmbH has been an important part of Lech-Stahlwerke in Meitingen. The site, which employs 25 people, processes all the steelworks' co-products and by-products, in particular the electric arc furnace slag (EAFS). In this way the company sustainably contributes to the reuse of the lava-like, solidified molten material as a construction material in many different areas. For example, when it comes to building roads, slag is a welcome alternative to gravel and grit. The slag as a by-product is thus recycled and conserves natural resources. Max Aicher Umwelt processes 200,000 tonnes of electric arc furnace slag annually on its 35,000 sqm site in Meitingen.
"A standstill on our site can, in a worst case scenario, lead to a standstill across the whole steelworks. When we are buying machines, a 24-hour all-round machine service is absolutely essential for us!" says Benjamin Kinlinger, Division Manager of EAFS Processing at Max Aicher Umwelt in Meitingen. With the Sennebogen sales and service partner Fischer & Schweiger the ideal support could be found: Thanks to the close proximity of the companies they can react quickly and reliably in an emergency. "You can only really judge a machine's consumption rate once it has been bought and put to work in real conditions. But even here Sennebogen keeps the promises made in advance."
As well as being reliable, the mobile material handling specialist is a multi-functional, powerful, and, above all, robust machine that is used in Meitingen with a magnet and an orange peel grab. It sorts, for example, larger and smaller pieces of slag weighing up to 10 tonnes. A 231 kW diesel engine, configured to meet stage V emissions standards, drives the huge undercarriage and all the work processes. One highlight: using just 13.9 liters of diesel per hour, the 45.5 tonner's thriftiness has impressed those on site. "You can only really judge a machine's consumption rate once it has been bought and put to work in real conditions. But even here Sennebogen keeps the promises made in advance," explains Kinlinger.
As the name suggests, the diesel machine's efficiency is down to the Sennebogen Green Efficiency principle. The hydraulic oil flow rate is optimally adjusted to the tasks being carried out by the machine, and, depending on the power required, the right amount of oil is pumped through the large-scale pipes to achieve the best level of efficiency. In addition, the machine has series standard in-built automatic idle and stop functions that reduce and/or completely halt consumption when the machine is not in use for brief periods of time. This means that the machine can always be operated in a fuel efficient way, without direct input from the operator.

Ultime notizie di Sennebogen Maschinenfabrik GmbH

Lifting
12/01/2024
The last Sennebogen 880 EQ leaves the factory
Sennebogen is retiring the 880 EQ balance material handler a...

Demolition
15/11/2023
Industrial deconstruction in the production halls of a die casting manufacturer
The Sennebogen 825 demolition excavator with its long reach...

Components
11/10/2023
Digital services at Sennebogen
Networking and data-driven optimization of machines for the...

Lifting
02/10/2023
71 years of Sennebogen at "WE SHOW 71"!
In this year’s in-house exhibition, the “WE SHOW 71” the lat...

Lifting
27/07/2023
Sennebogen opens new steel plant in Hungary to meet growing demand
Sennebogen is continuing its growth strategy and expanding i...

Earthmoving Machinery
30/06/2023
Sennebogen: Building demolition in two days with 45 t demolition excavator
A warehouse silo has been dismantled piece by piece by the S...
Altri International
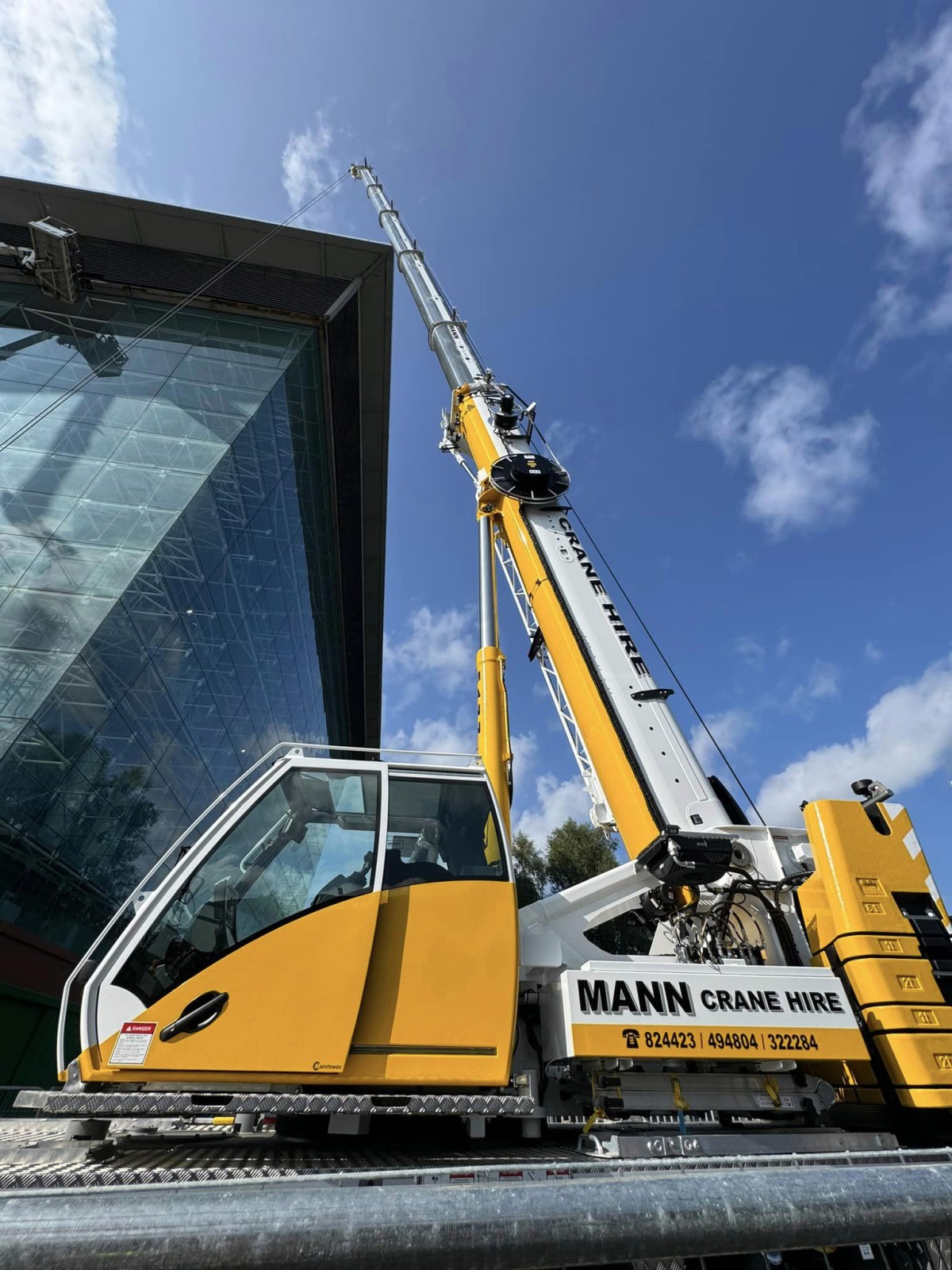
International
25/11/2024
New Grove GMK3060L-1 drives busy schedule for Mann Crane Hire
• Mann Crane Hire selected the GMK3060L-1 for its class-lead...
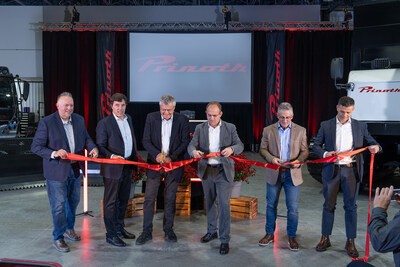
International
25/11/2024
Prinoth Unveils Expanded Production Facility in Granby, Canada
Prinoth held an event to announce the official opening of it...
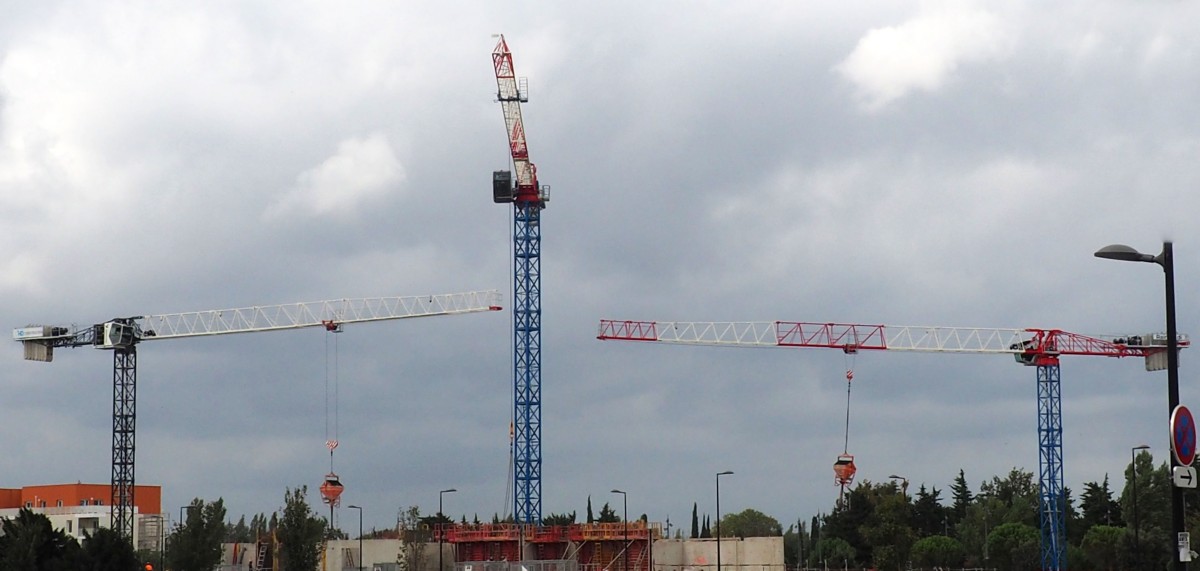
International
23/11/2024
GPMat International takes delivery of two Raimondi T147s residential development in the South of France
- Official agent of France expands its product lineup with t...
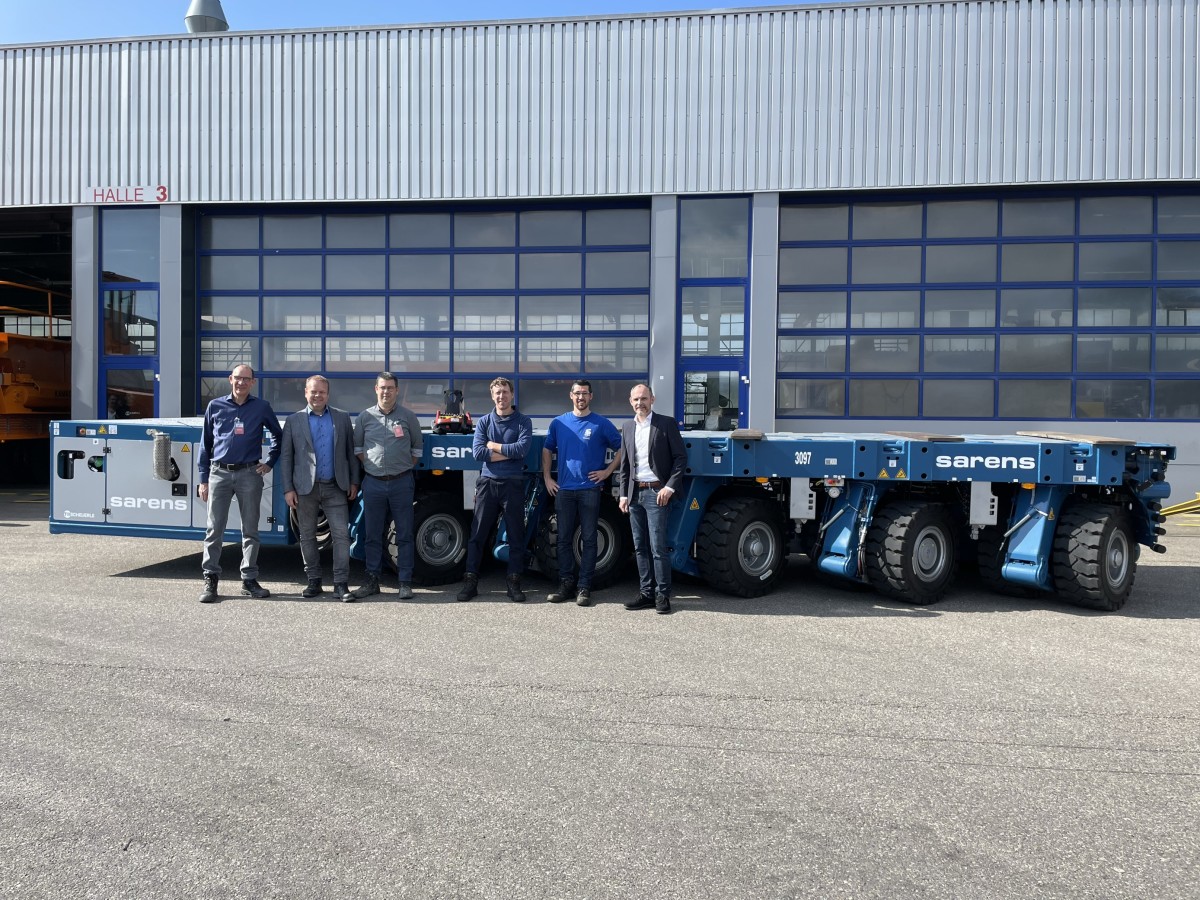
International
22/11/2024
Sarens acquires additional SCHEUERLE SPMT K24 modules
renowned for its expertise in crane rental services, heavy l...
International
22/11/2024
Five WOLFF cranes modernize Oslo’s Ulven district
With a total of five WOLFF cranes of type 7534.16 Clear, Wol...
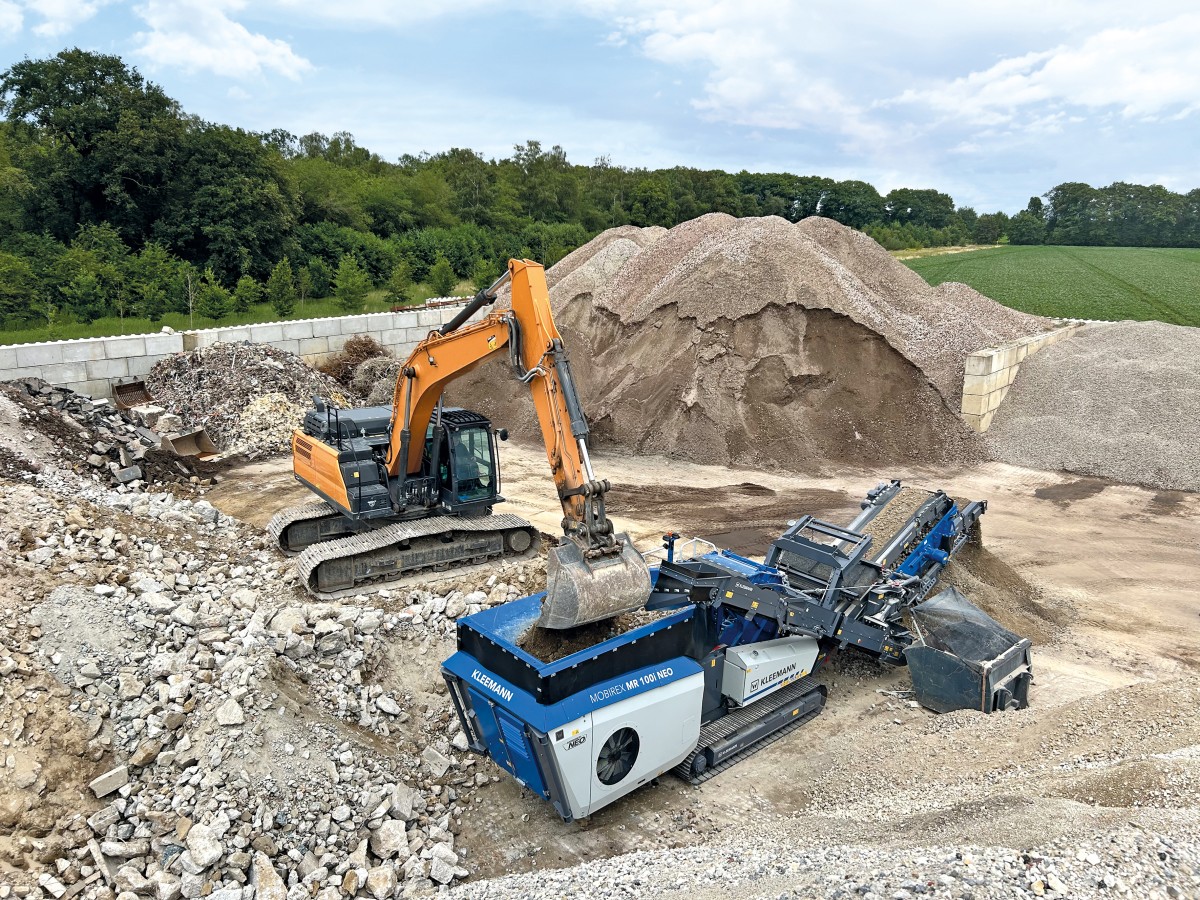
International
21/11/2024
Kleemann: New compact crusher used for recycling
Impact crusher MOBIREX MR 100i NEO impresses during operatio...