Home \ International \ Modern Liebherr mixing plant of type Betomix 2.5 in operation in Berlin
Modern Liebherr mixing plant of type Betomix 2.5 in operation in Berlin
20/10/2021
Pubblicato da Redazione
Liebherr mixing plant Betomix 2.5 produces up to 115 m³ concrete per hour, aggregates can be fed to the plant from an HGV.
The ultra-modern and well-equipped Betomix 2.5 further expands the ready-mixed concrete services of Heidelberger Beton GmbH in Berlin. The mixing plant delivers up to 115 m³ output per hour with its proven DW 2.5 twin-shaft mixer. The automatic high pressure cleaning system cleans the mixer and collecting funnel largely automatically, whereby the daily manual cleaning times are reduced to a minimum. Plenty of space on the mixer platform and generous platforms and walkways make all areas of the plant easily accessible.
The entire steel structure of the mixer and weigher platform, the skip elevator and the weighing belt have been hot-dip galvanised for a long service life. The latest generation of the Betomix horizontal mixing plant series has been successfully established worldwide for many years, thanks to its modular concept. This design facilitates numerous variants in accordance with customer requirements and equipment, such as the bucket elevator for feeding.
The inline silo with seven chambers holds around 350 m³ of aggregates; four of the seven chambers are divided. A recessed charging hopper allows the sand and gravel delivery to be tipped out at ground level by dump trucks; a wheel loader is not required. A bucket elevator transports the materials upwards onto a reversing belt for feeding the chambers. Four of the chambers are equipped with the Litronic FMS moisture measurement sensors developed by Liebherr; the sand moisture levels are measured up to 40 times per second.
Six cement silos with a total cement store volume of 600 tonnes are available for cement storage. By dividing two silos, it is possible to store a total of eight types of binding agents. During winter operation, a heating system conducts warm air into the aggregate silos. This guarantees operation during the cold season.
Heidelberger Beton GmbH placed great importance on the issue of safety when planning the plant. Through additional characteristics, it was possible to enhance the safety standards even further: For example, all walkways were designed with a width of 800 millimetres instead of 600 mm and were realised in slip resistance class R11. Heidelberger Beton GmbH paid particular attention to emergency exit, rescue and escape routes. The plant design includes no ladders for ascending and descending; instead, all areas up to the top of the cement silos are accessible via stairs. All pneumatic components that pose a risk of crushing are safeguarded during maintenance work by lockable ball valves. Electric drives are protected by lockable inspection switches.
The plant is secured with a transfer key locking system. In this way, all maintenance points that pose a potential risk include a consistent process of unlocking and locking before maintenance work is possible to deliver maximum hazard reduction. Accessing these areas during plant operation would be life-threatening.
The entire mixing plant is equipped with extensive accessories. These include video surveillance systems for monitoring in various areas, a traffic light system on the silo chambers for the levels and vibrators on the silo walls. Air dispersion receptacles are used for material with poor sliding characteristics. The accessories are completed by a 60 millimetre insulating lining for the plant and dust filter systems.

Ultime notizie di Liebherr EM-Tec Italia
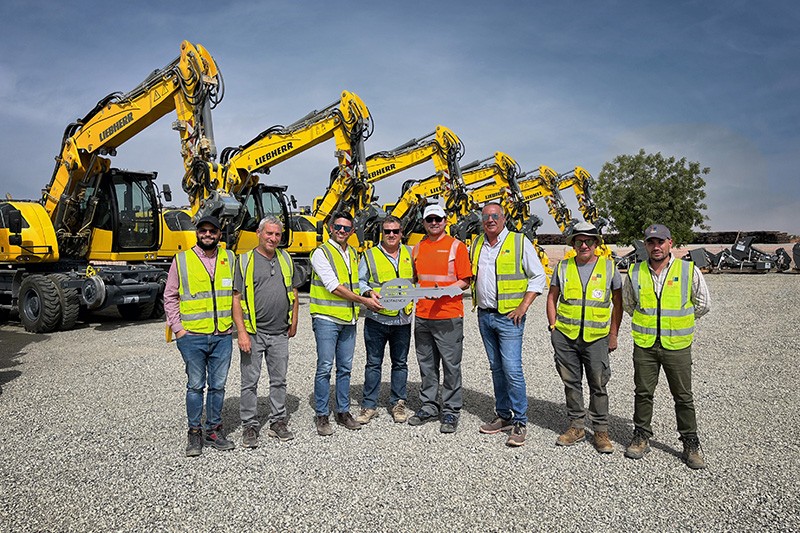
Earthmoving Machinery
26/11/2024
Mota-Engil orders 10 Liebherr railroad excavators for a major project in West Africa
The Portuguese construction company Mota-Engil has once agai...
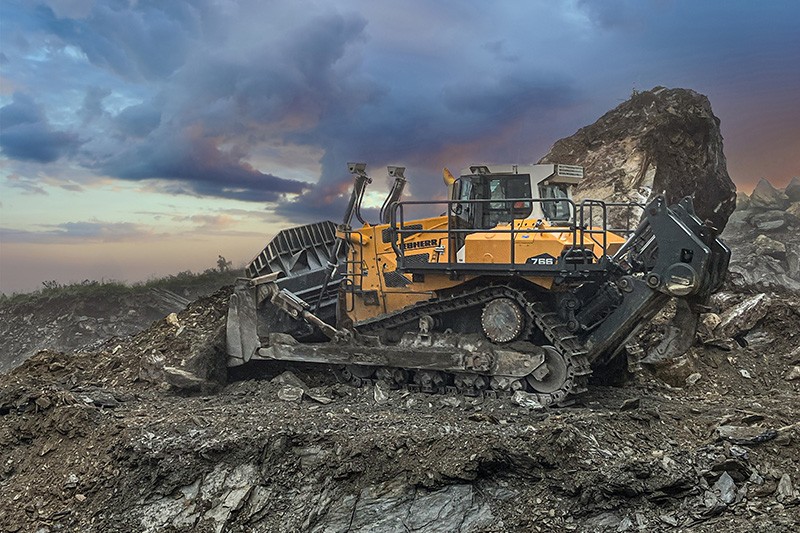
Earthmoving Machinery
22/10/2024
Hollaus company puts Liebherr to the test in reservoir construction
Equally impressive is the tremendous ripping and pushing per...
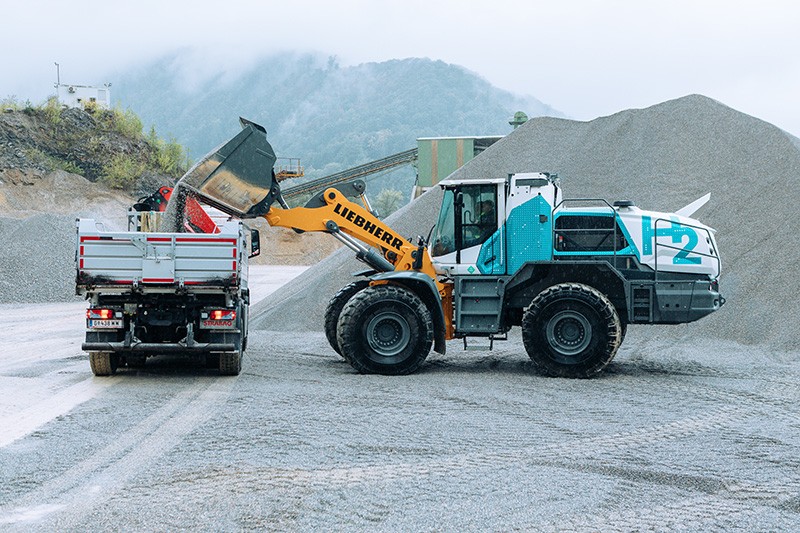
Earthmoving Machinery
18/10/2024
Liebherr and STRABAG test hydrogen wheel loader
Together with STRABAG, Liebherr is taking important steps to...
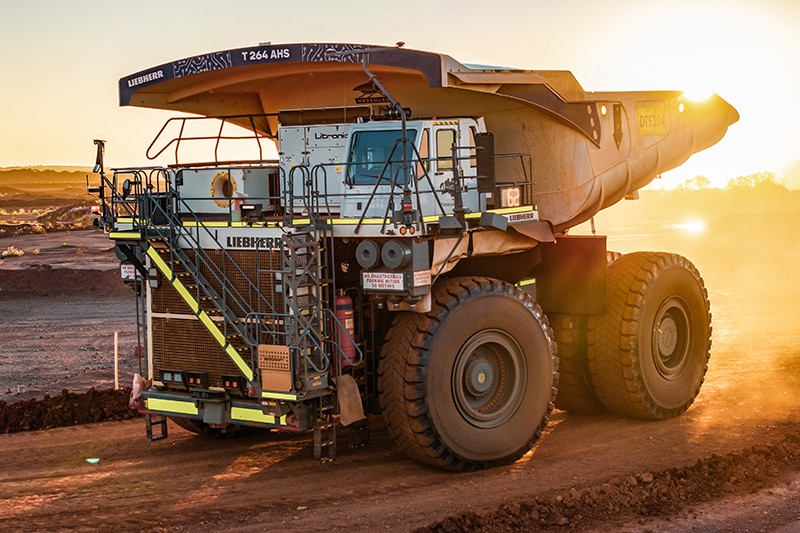
Earthmoving Machinery
07/10/2024
Liebherr’s expanded technology portfolio for integrated operations
Liebherr presented its updated and expanded technology portf...
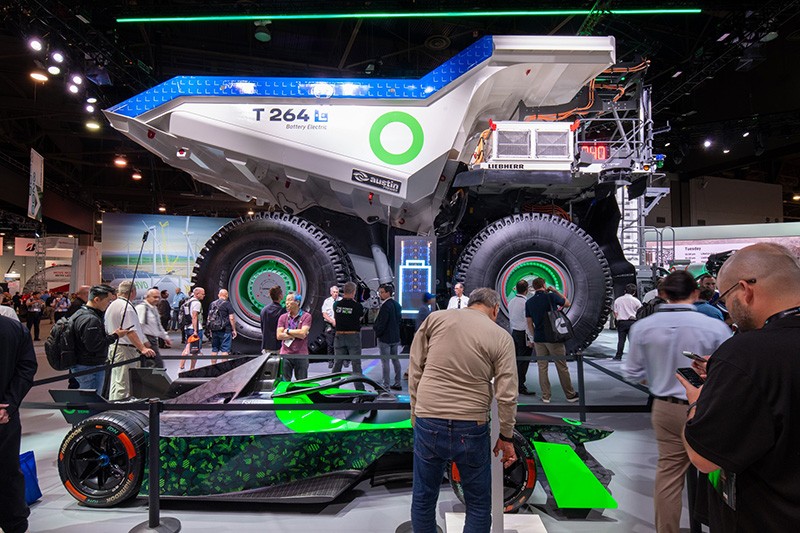
Earthmoving Machinery
27/09/2024
Liebherr presented its latest mining technology at MINExpo 2024
During the exhibition, Liebherr unveiled its autonomous batt...

Earthmoving Machinery
11/09/2024
High efficiency and power output: Liebherr crawler dozer PR 776
Spanish construction company AMM invests in Liebherr Crawler...
Altri International
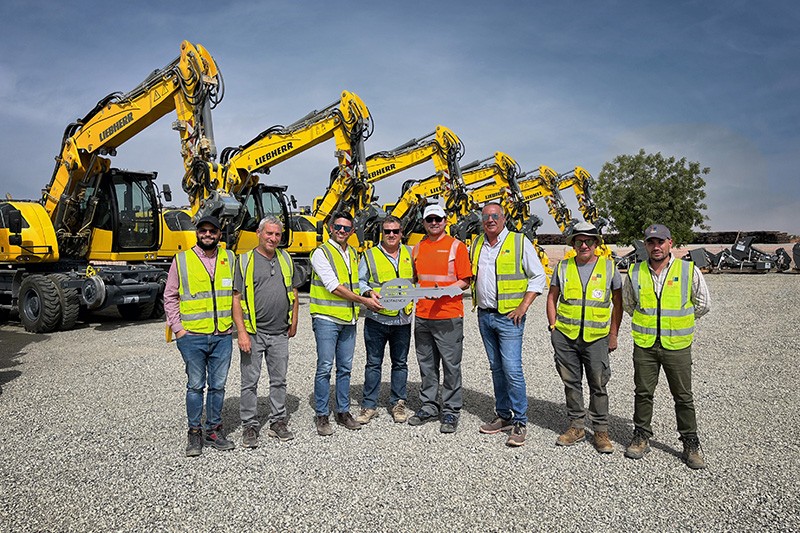
International
26/11/2024
Mota-Engil orders 10 Liebherr railroad excavators for a major project in West Africa
The Portuguese construction company Mota-Engil has once agai...
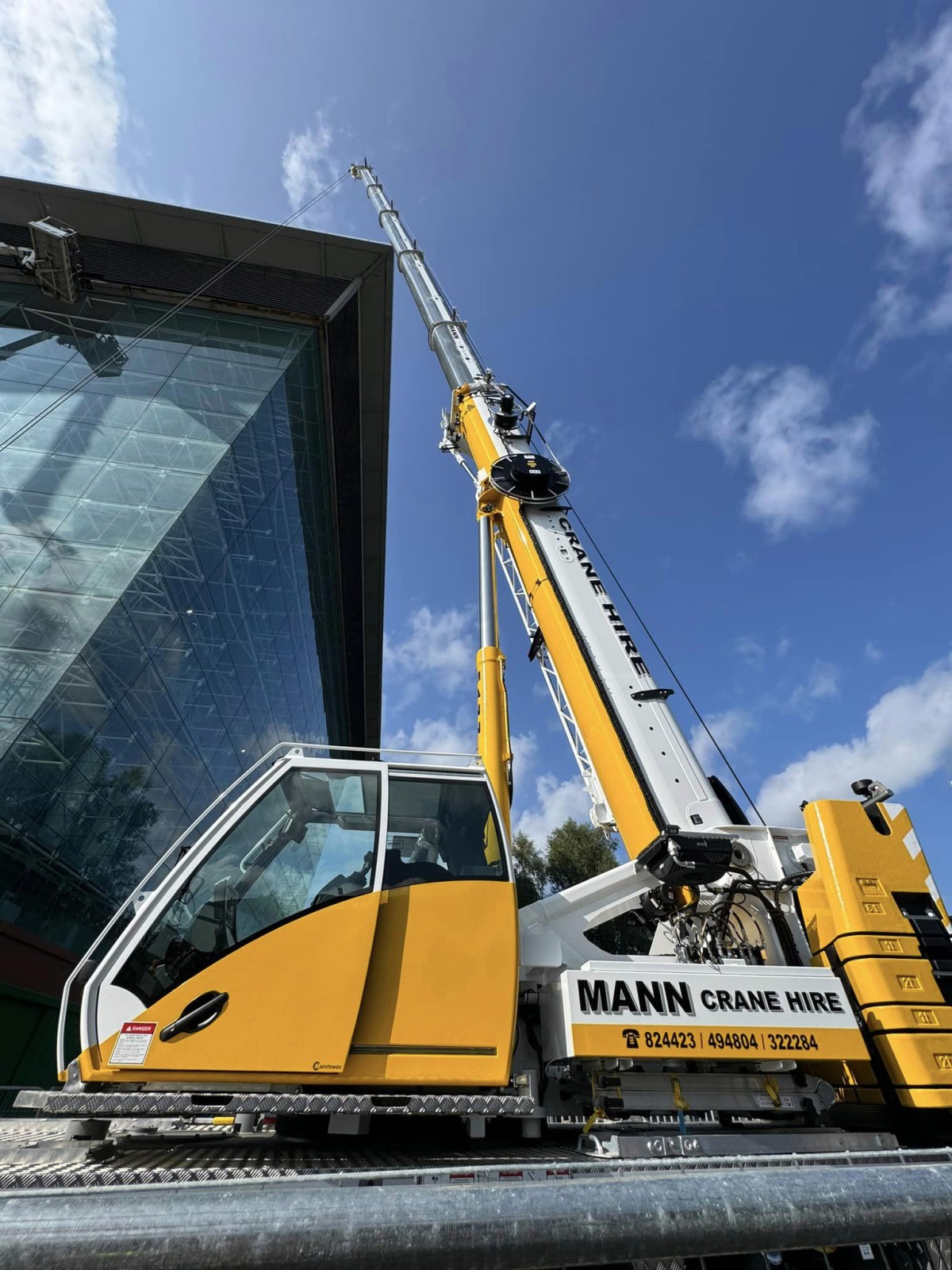
International
25/11/2024
New Grove GMK3060L-1 drives busy schedule for Mann Crane Hire
• Mann Crane Hire selected the GMK3060L-1 for its class-lead...
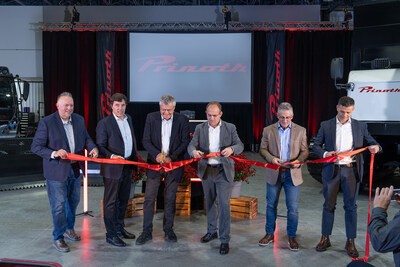
International
25/11/2024
Prinoth Unveils Expanded Production Facility in Granby, Canada
Prinoth held an event to announce the official opening of it...
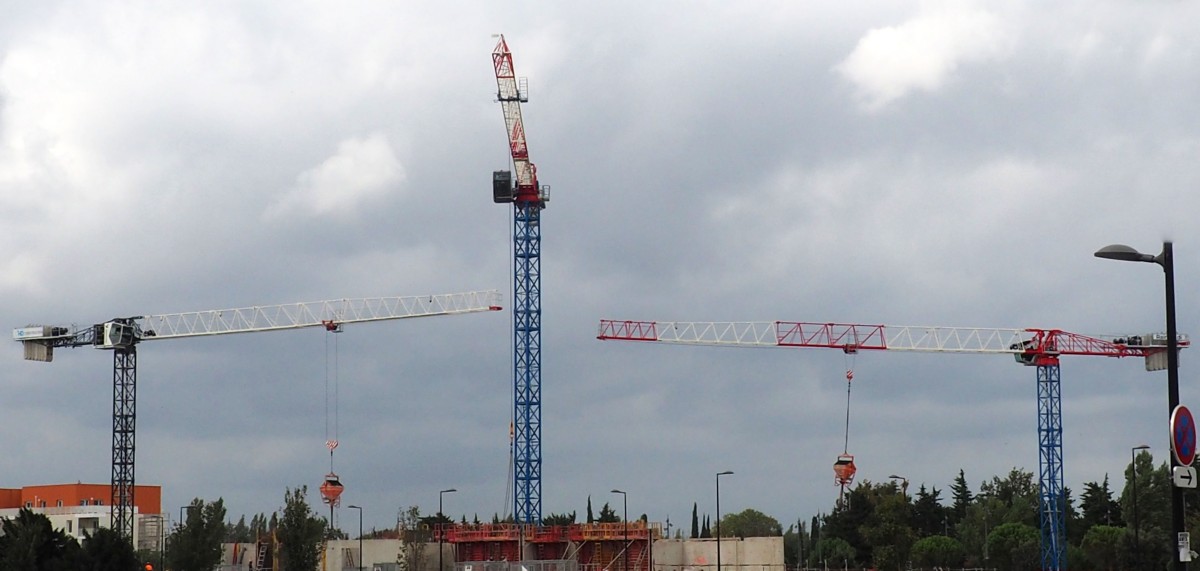
International
23/11/2024
GPMat International takes delivery of two Raimondi T147s residential development in the South of France
- Official agent of France expands its product lineup with t...
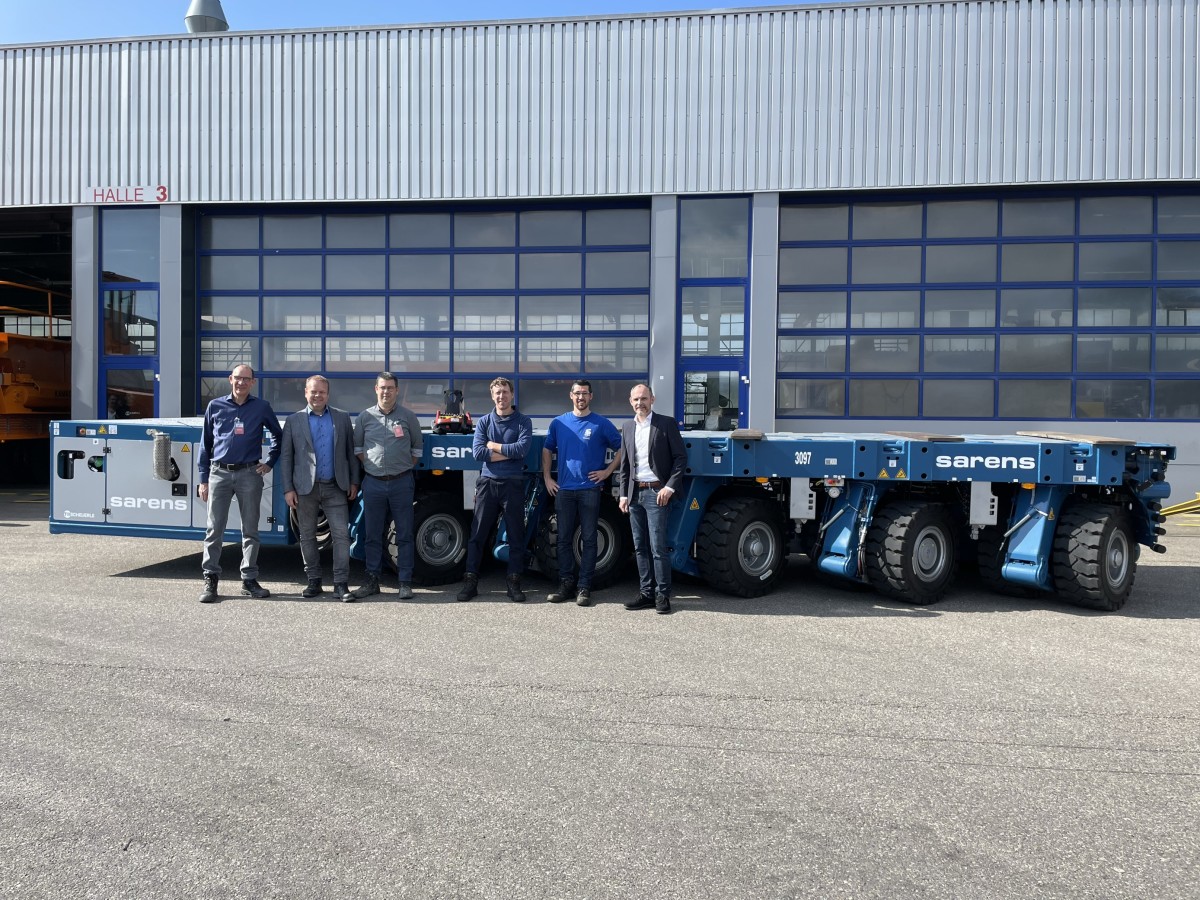
International
22/11/2024
Sarens acquires additional SCHEUERLE SPMT K24 modules
renowned for its expertise in crane rental services, heavy l...
International
22/11/2024
Five WOLFF cranes modernize Oslo’s Ulven district
With a total of five WOLFF cranes of type 7534.16 Clear, Wol...