Home \ International \ New Ammann eARX 26-2 Roller Utilises Electric Drive
New Ammann eARX 26-2 Roller Utilises Electric Drive
01/02/2024
Pubblicato da Ettore Zanatta
Ammann’s new eARX 26-2 Light Tandem Roller features a fully electric drive that can operate for up to 18 hours – and sometimes beyond – without recharging.
Ammann’s new eARX 26-2 Light Tandem Roller features a fully electric drive that can operate for up to 18 hours – and sometimes beyond – without recharging.
The absence of a combustion engine makes the eARX 26-2 extremely quiet during operation. Sound levels reaching the operation station are 46% less than with a diesel version. The innovative powertrain concept eliminates almost all hydraulic components. The ecological impact is also lessened – and total ownership costs are significantly reduced – by replacing the diesel engine and its cooling system. Important features, besides the electric drive, are the roller’s design, drum construction, operator platform and engine compartment.
The eARX 26-2 is equipped with a powerful battery pack with electric motors for the main drive and vibratory circuits. Gone are the conventional combustible (diesel) engine, hydrostatic drive and cooling circuits. Key is the advanced 48-volt battery pack with a capacity of 600 Ah/31,5kWh. The pack’s LiFePO4 technology is unique because each internal battery cell is independently protected. This makes the entire pack flame-resistant, increasing safety. The roller’s technology provides extended operation on a single charge. Depending on the jobsite and the demands on the machine, an eARX26-2 can operate up to 18 hours without having to recharge. This means the machine must only be charged once per typical working day, usually at the end of the working shift (depending on jobsite conditions). All electric drive and vibratory motors are equipped with a recuperation mechanism as standard. When the machine stops, or when vibration is turned off, the electric motors continue to generate power – and send it to the main battery to increase charge.
The battery can be recharged via the recuperation process during machine operation – or with chargers when the machine is not operating. Charging is fast, easy, and requires no special tools. Two charging systems are available: On-board charger – 50-amp charging system with 12 hours charging time (from 0% to 100% battery capacity); External charger – 200-amp charging system with 3,5 hours charging time (from 0% to 100% battery capacity). The LiFePO4 battery is characterised by a long lifespan and a high number of charging cycles. The battery is likely to last for the life of the machine.
The operator can continuously monitor battery charge level. An automatic alert is sent via the multi-functional display when charge falls to 10%. If the level drops to 3%, the system automatically disengages the vibrator to conserve power for machine travel to a charging zone. Ambient operating temperatures are another important advantage. The temperature ranges are wider than Li-ion batteries and other common technologies. LiFePO4 batteries can operate below the freezing point – specifically from -10° C (14° F) – and up to 60° C (140° F).
The fully electric drive offers the unique possibility for 100% traction control. Ammann Traction Control (ATC) is able to precisely distribute drive power to the drums without any delays or losses in power transfer, which makes this the best climbing machine on the market. Electric drive motors require more space than hydrostatic motors. Therefore, an innovative approach to vibratory drum design was required. Ammann developed a patented solution that makes it possible for drive motors to be installed inside the drums and within the eARX 26-2’s contour. This means there are no limits for operators when working close to obstructions. Electric drive motors also bring more precise control to the vibratory unit. This enables frequency control that is unique to the market. Vibratory settings can be adjusted from 55 Hz to 66 Hz for high-quality, efficient compaction output. A key improvement is effortless switching between drive modes, which can now be adjusted with an electric control. Soft drive enables smooth, steady adjustments to directional changes – particularly important when working on asphalt. Hard drive responds quickly to directional changes. Panic stop idles the machine if the operator makes very sudden directional changes or significantly adjusts the travel lever position.
The operator station is consistent with the complete line of Ammann Light Articulated Tandem Rollers. This includes technical advantages that improve machine operation, resulting in easier control, higher productivity and enhanced operator comfort. The operator’s platform is insulated with rubber buffers, limiting the vibration that reaches the operator. The lack of a combustible (diesel) engine reduces additional vibration, making the ride very smooth during transport or static use. All indicators and controls are conveniently located and visible on the dashboard and multi-functional display. The operator can easily monitor the battery charge, load and recuperation.
The machine fits well on sound-sensitive jobsites such as crowded locations, city centres, and historical and residential areas. The eARX 26-2 is a great fit for night work. The absence of a diesel engine and after-treatment structure eliminates exhaust emissions. Therefore, the machine can work inside buildings and at underground jobsites, such as tunnels. Intuitive control and easy-to-explain operation are big benefits for those who provide training to end users, for those who rent for a short time, or for less-skilled operators. The usage of only 48 volts is another safety feature. The low voltage minimises risk of injury during operation and service.
Serviceability, reduced downtime and total cost of ownership are essential to profitability. The eARX 26-2 is almost maintenance-free, which significantly decreases the total cost of ownership and improves profitability. There is no combustible (diesel) engine to maintain – or diesel particulate filters to worry about. The vibratory system and articulation joint are maintenance-free. All rollers are equipped with an auto-diagnostics system that communicates with service technicians.
The zero emissions machine is part of Ammann’s eMission initiative, which lessens environmental impact and improves economic efficiency. Products in the eMission programme represent a new chapter in sustainability at Ammann, including reduced levels of CO2 and a smaller carbon footprint. This becomes increasingly important as emissions regulations become stricter. The core of eMission is development of a highly innovative power train structure. The new generation of eMission machines also reflects a commitment to minimise maintenance and the total cost of ownership. This includes decreasing the volume of fluids required and making service points extremely accessible. This Ammann commitment – known as ECOdrop – makes the latest Ammann products significantly more environmentally friendly. ECOdrop combines with eMission to produce machines that are unique in terms of positive ecological impact, significantly cutting total costs of machine ownership due to: The lack of a diesel engine – no periodic change of engine oil or filter; The absence of an engine after-treatment structure (EGR, DOC, SCR, DPF) – no additional cost or regular maintenance; The elimination of a DEF tank – no filters to be changed, tanks to be cleaned or fluids to leak; The exclusion of a cooling system – no cooling liquid to change; The use of a maintenance-free articulation joint and vibratory system – no maintenance needed for the life of the machine; The reduction of hydraulic oil to 4 litres – only needed for the steering circuit.
Ammann ServiceLink is a standard feature of eMission machines. ServiceLink is a simple and efficient fleet management method for construction machines, providing comprehensive control of machine data for customer fleets. This method of self-monitoring makes it easy to avoid expensive downtime, evaluates parameters and offers intuitive operation.

Ultime notizie di Ammann Group

Equipments
04/04/2024
Ammann E-Drive Rammer retains power, other key features
The new Ammann eATR 68 Rammer, an electric-drive machine, ge...

Earthmoving Machinery
28/02/2024
Ammann announces the Electric-Drive Mini Excavator eAMX 15
Ammann announces the release of its first electric-drive min...

Road Machinery
27/02/2024
Ammann’s new ARP 75 Pivot-Steer Tandem Roller
New Pivot-Steer Roller Features Fingertip Steering, Innovati...

Road Machinery
16/02/2024
Ammann E-Plates match power of petrol versions
Ammann’s new eAPF 12/40 and eAPF 12/50 Forward Moving Vibrat...

15/10/2019
Waste glass becomes high-quality sand
Ammann plant part of groundbreaking recycling effort

02/10/2019
Compact design ensures stability for ARS 200 and ARS 220 single-drum rollers – even on slopes
Lower Centre of Gravity Makes Compaction Work Easier
Altri International
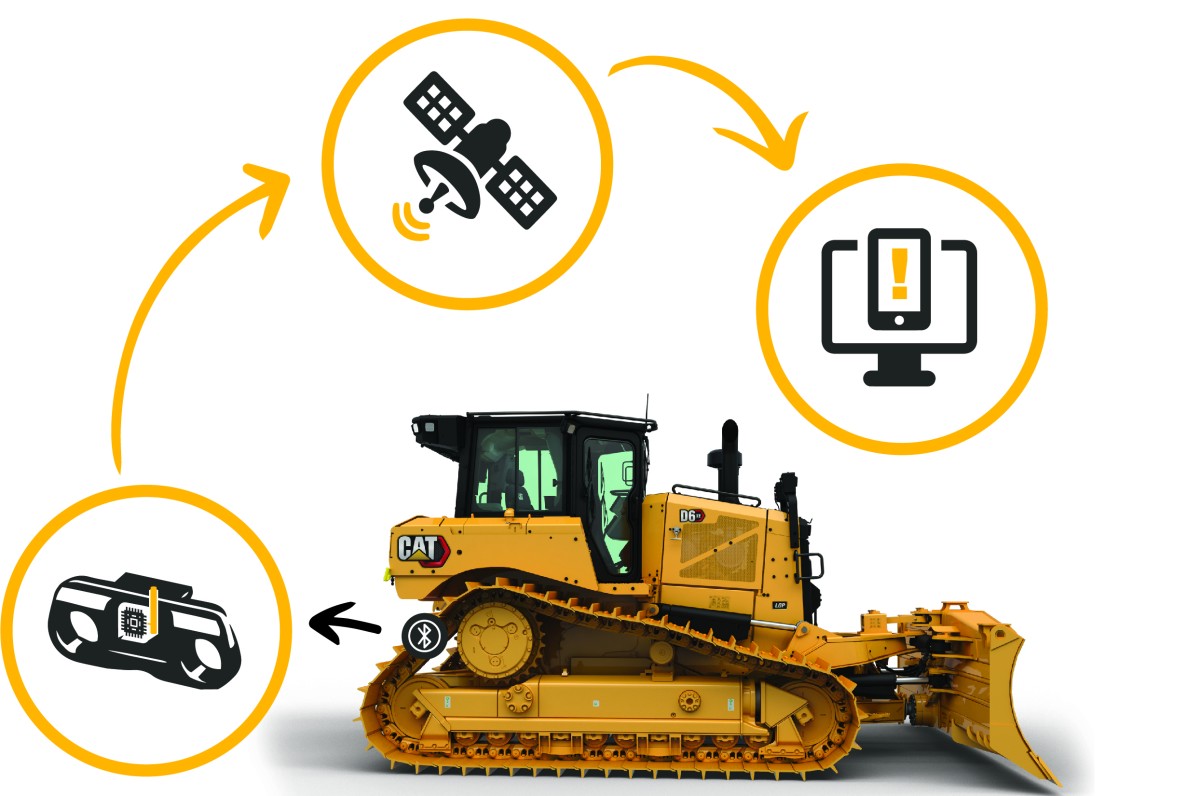
International
26/07/2024
Exclusive new Cat Track Wear Sensor
Exclusive new Cat Track Wear Sensor provides remote, no-touc...
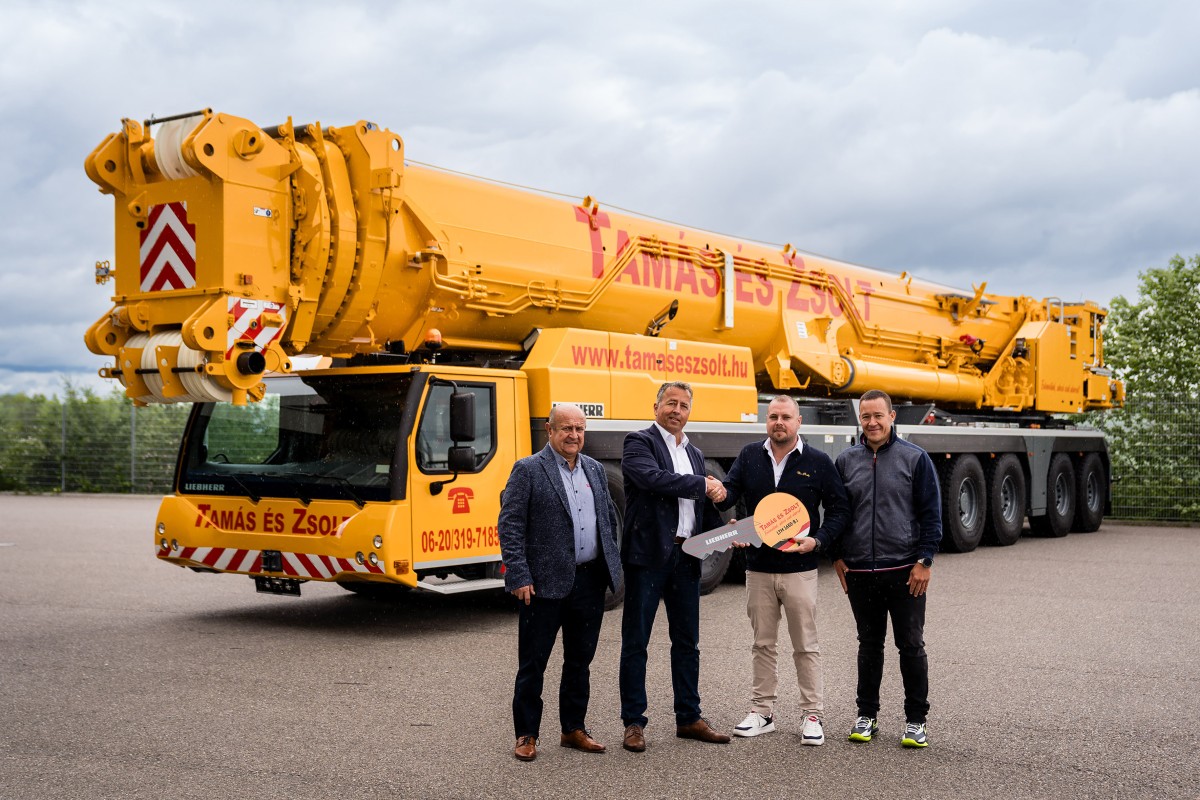
International
26/07/2024
Tamás és Zsolt Kft. took delivery of Liebherr LTM 1650-8.1
Tamás és Zsolt Kft. has added a Liebherr LTM 1650-8.1 to its...
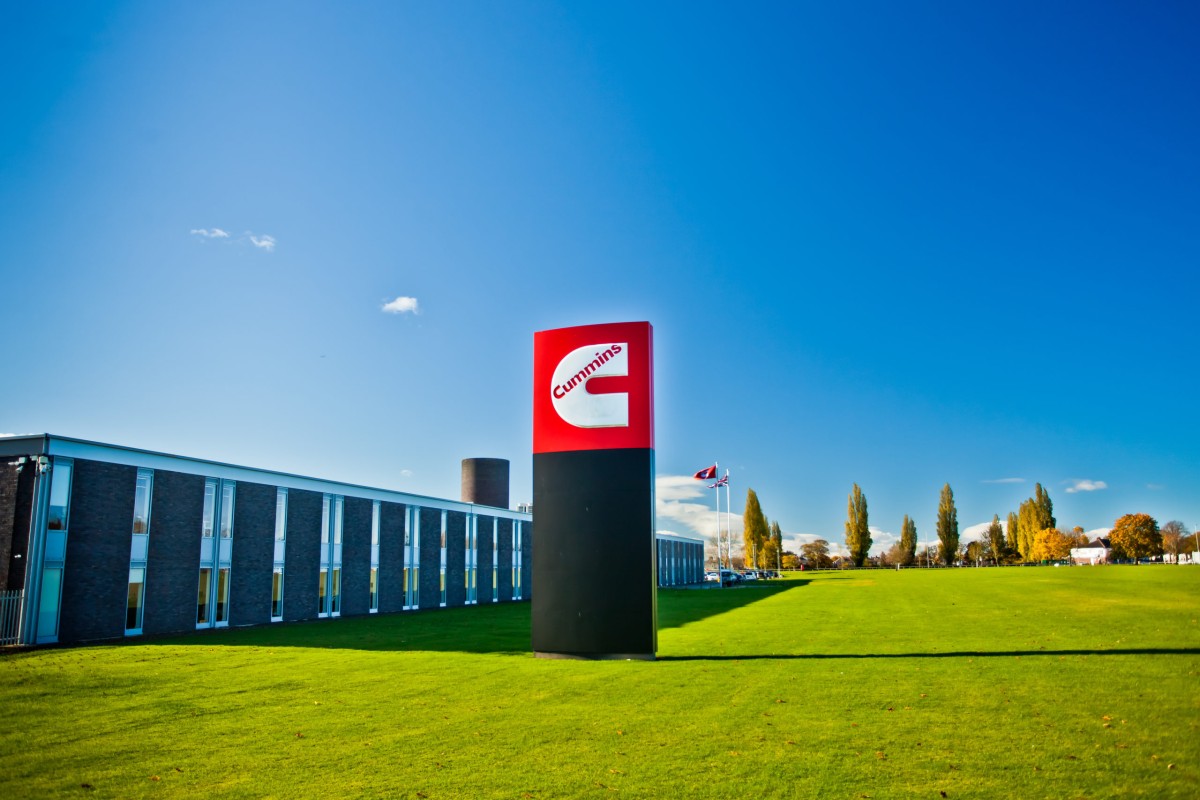
International
25/07/2024
Cummins opens new powertrain test facility
Cummins has opened a new powertrain test facility to support...
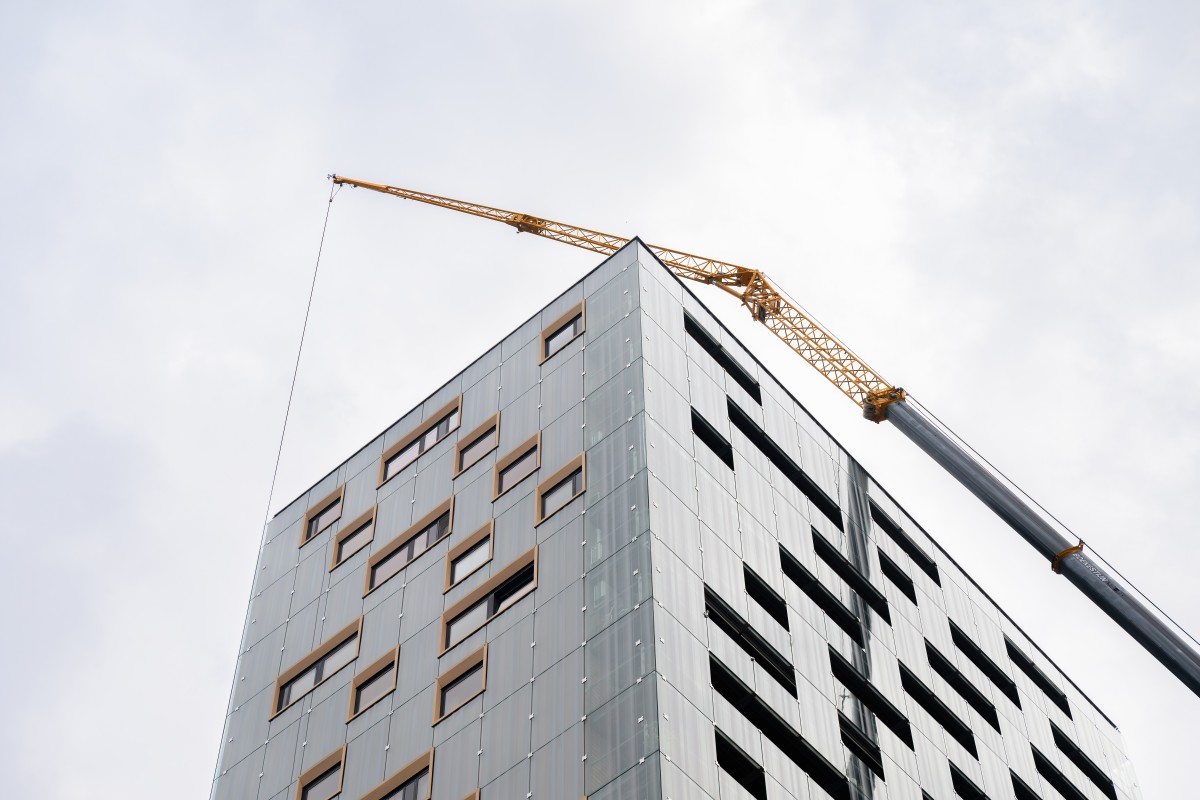
International
25/07/2024
Grove GMK6300L-1 proves perfect for compact jobsite in Rotterdam
Kraanverhuur Boekestijn sent its Grove GMK6300L-1 for city c...
International
24/07/2024
MB Crusher breaks records and crushes challenges
MB Crusher is proud to support the construction of arenas, s...
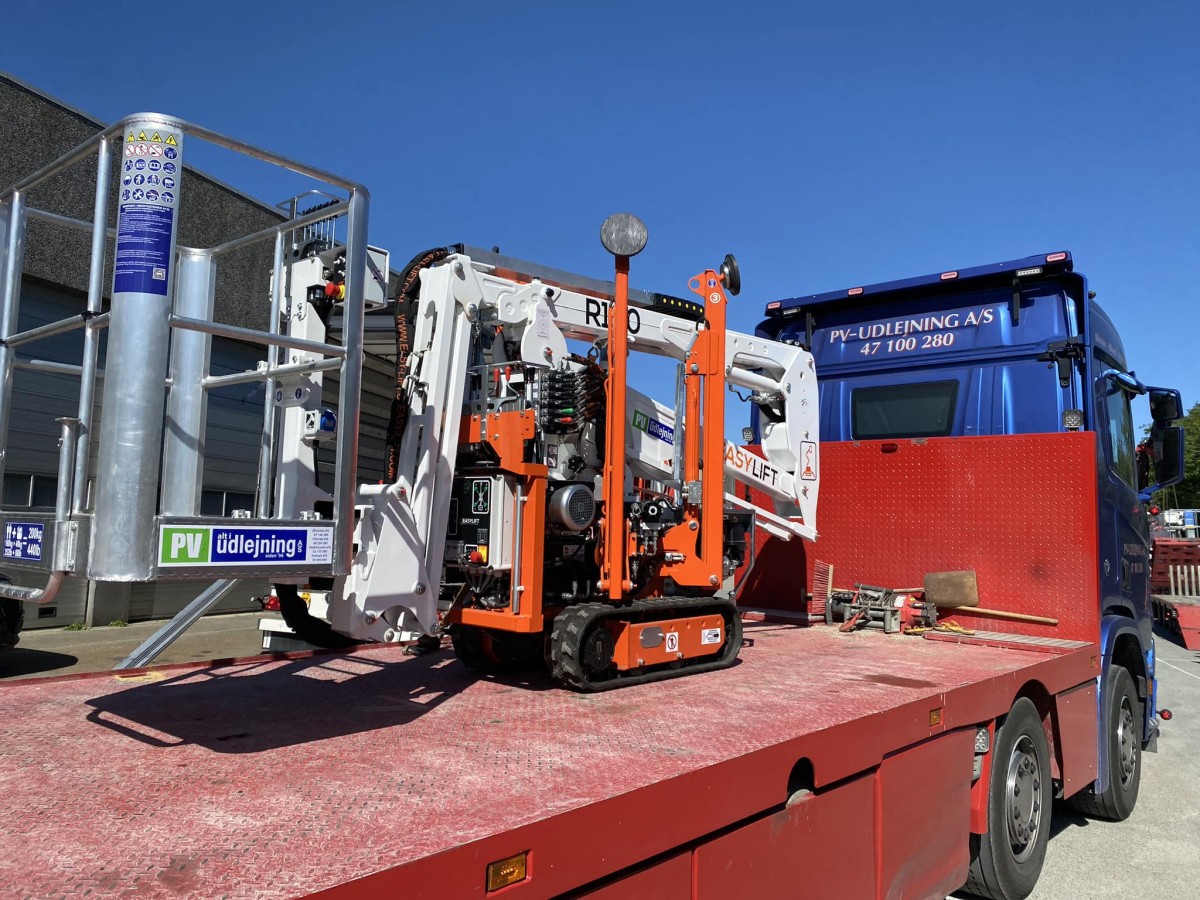
International
24/07/2024
Hammer Lifte makes a full load of deliveries of Easy Lift spiders
Easy Lift's Danish dealer, Hammer Lifte, is always busier to...