Home \ International \ Nine essential tips for a great ADT operator
Nine essential tips for a great ADT operator
27/05/2024
Pubblicato da Redazione
Scottish ADT manufacturer Rokbak explains how to master the art of being a successful and trusted articulated hauler operator
An efficient articulated hauler operator combines technical expertise, safety and situational awareness with effective communication and a commitment to productivity. Scottish ADT manufacturer Rokbak explains how to master the art of being a successful and trusted articulated hauler operator.
Get ready to move: take control of the hauler and your daily work before the ignition has been switched on by making sure you know the truck. It’s important to have a thorough understanding of the truck's controls, capabilities and limitations. This includes knowing how to operate it efficiently and safely in various conditions, such as on gradients, rough terrain or in adverse weather.
Check things over: at the start of the working day, prestart checks are essential. A diligent operator conducts routine truck inspections to make sure the truck is ready for work. You should check for pre-existing damage including identifying leaks and loose parts, the tyre conditions, lights and beacons are fully operational, full visibility through the windows and fluid and battery levels daily. Rokbak trucks have ground level test points and a fully tilting cab for quick, easy access when servicing. A thorough equipment walkaround before starting a shift can make a big difference, and it doesn’t require a lot of time.
Know your limits: before you start working, learn your worksite boundaries such as speed, ground bearing weight limits, travel direction, passing areas, width and height restrictions and no-go areas. Know your hauler’s capacity and ensure you are aware of your truck’s working limits with regard to payload. Furthermore, keep an eye on how many buckets the loader is dumping in the truck to stay within the safe operating limits of the ADT and avoid accelerated component wear through overloading. Rokbak provides an optional onboard payload system and exterior payload lights, which indicate to both the truck and loader operators whether the payload is on target or overloaded. This information is recorded and transmitted via the Haul Track telematics system.
Safe operation: follow all site operating procedures when driving the truck. Keep under speed and under control on gradients and check grade guides for safe and controlled descent speed. Correctly use differential locks – you’ll want to employ them when you’re operating in soft or slippery ground conditions to maintain traction and control. Be aware of what equipment is on your haul route and what sort of traffic you can expect to encounter.
Correct usage: the Rokbak RA30 and RA40 articulated haulers have fully enclosed multi-disc brakes on all six wheels plus a retarder to deliver safe, consistent performance. Understanding the correct use of the retarder can prolong the life of the service brakes and reduce maintenance intervals for lower total cost of ownership (TCO). If required, make use of the transmission lock in range or manual shift modes to maintain a steady ascent or descent on gradients.
Stay alert: a good ADT operator stays alert to their surroundings, including other workers, vehicles and obstacles on site. They anticipate potential hazards and adapt their driving accordingly to maintain safety for themselves and others. Inevitably there will be challenges, such as navigating tight spaces. An alert operator can quickly assess situations, make informed decisions and take appropriate action to resolve issues while minimising downtime. Never operate an articulated hauler if feeling fatigued or unwell.
Keep an eye on targets: operating an articulated hauler requires attention to detail to ensure proper loading, unloading and manoeuvring of materials. While an integrated payload system can account for the number of loads moved, manually recording progress in relation to a target keeps productivity proceeding on schedule. For improved fuel efficiency, minimise heavy acceleration and aim to reduce unnecessary idle time whenever feasible.
Don’t ignore fault codes: critical information is delivered whenever system fault codes are triggered. If a Rokbak truck does develop a fault, the operator will receive a warning symbol on the dashboard. Faults should be reported when they occur as continuing operating could exacerbate the issue. Following the truck’s advice means increasing uptime by avoiding potential disruptions, and effective communication with site supervisors, co-workers and other equipment operators is crucial for coordinating tasks and ensuring smooth operations.
At the end of a shift, follow the correct shutdown procedure. Allowing the truck to idle for a brief period at the end of a long workday enables the coolant to circulate through the engine. This helps to gradually lower the temperature, preventing potential damage from frequent ‘hot shutdowns’ over time. Adhering to the correct maintenance and start-up and shutdown procedures will help to keep operation costs low.

Ultime notizie di OnSite News
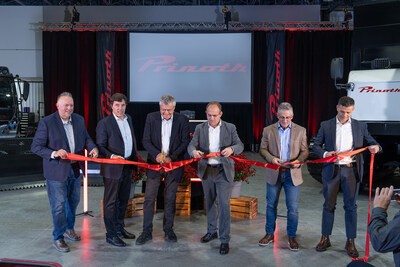
Earthmoving Machinery
25/11/2024
Prinoth Unveils Expanded Production Facility in Granby, Canada
Prinoth held an event to announce the official opening of it...
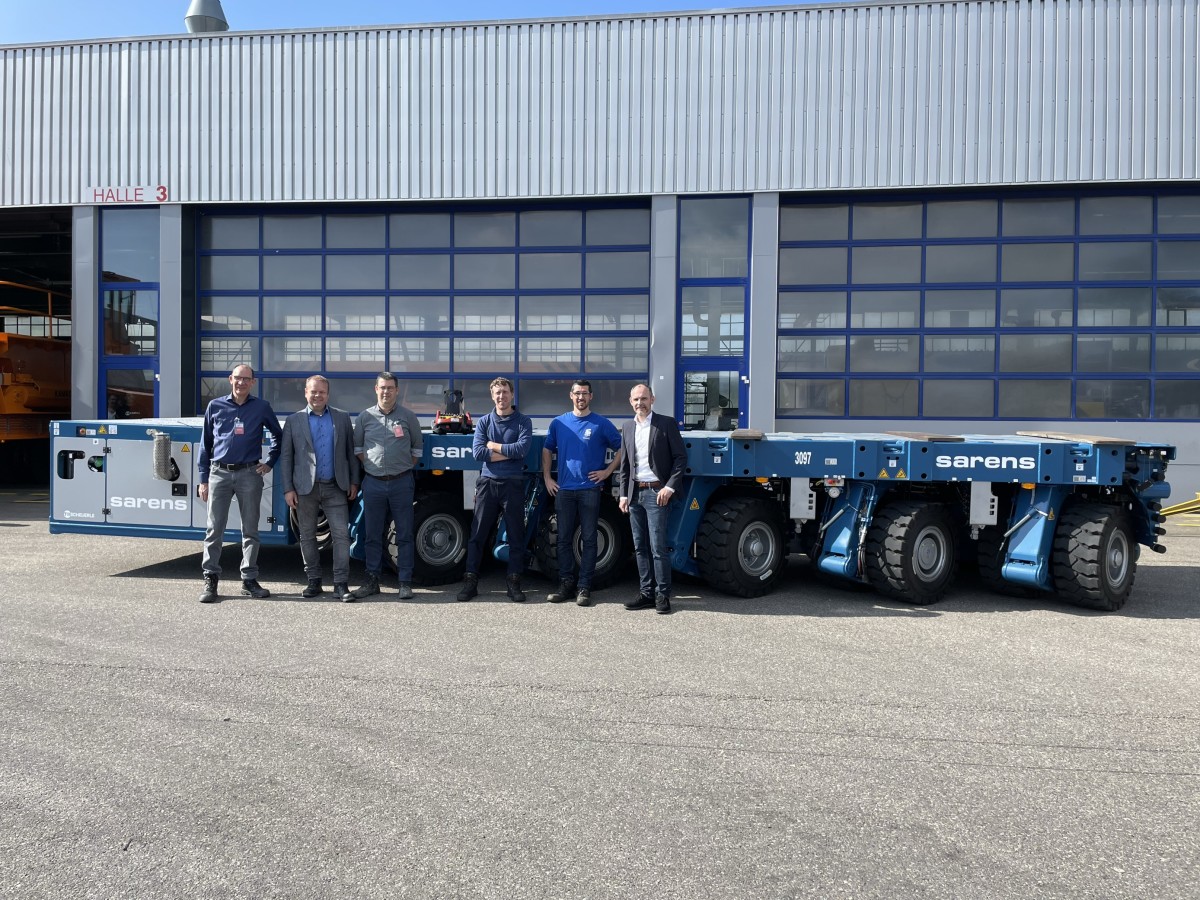
Logistics
22/11/2024
Sarens acquires additional SCHEUERLE SPMT K24 modules
renowned for its expertise in crane rental services, heavy l...
Equipments
21/11/2024
SITECH partners with Royal Engineers to create poppy and demonstrate tech offering
The demostration involved creating a ground-level poppy desi...
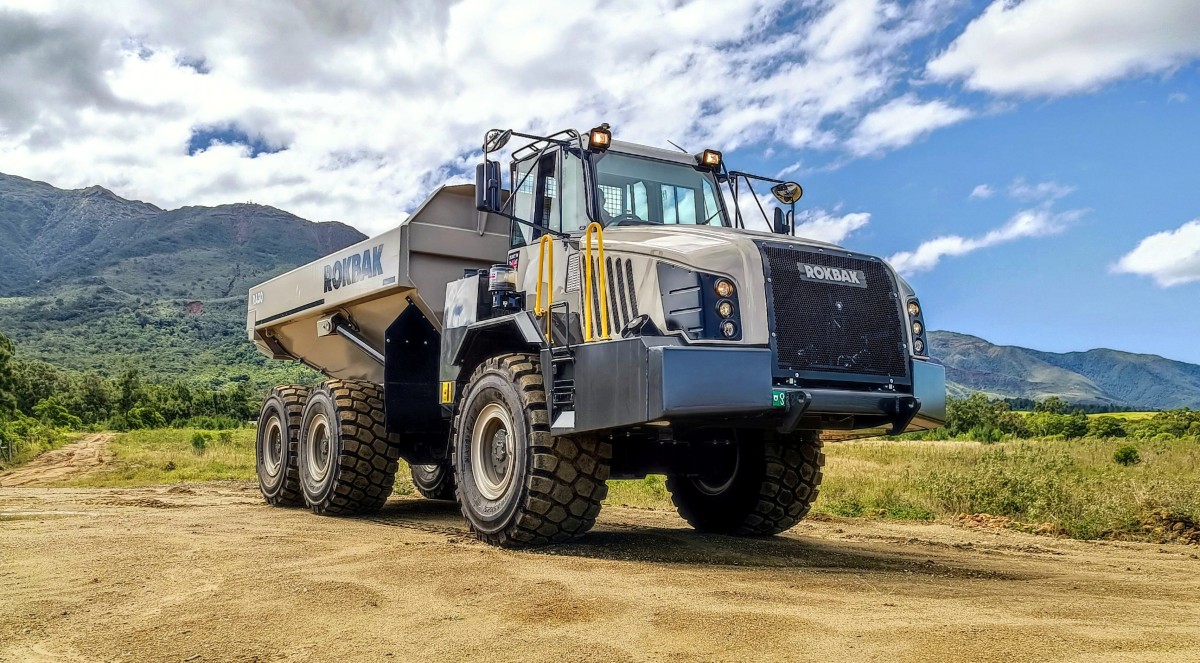
Earthmoving Machinery
20/11/2024
Strong and stable RA30 trucks carry the weight at New Caledonian mine
Three Rokbak RA30 trucks are delivering exceptional durabili...
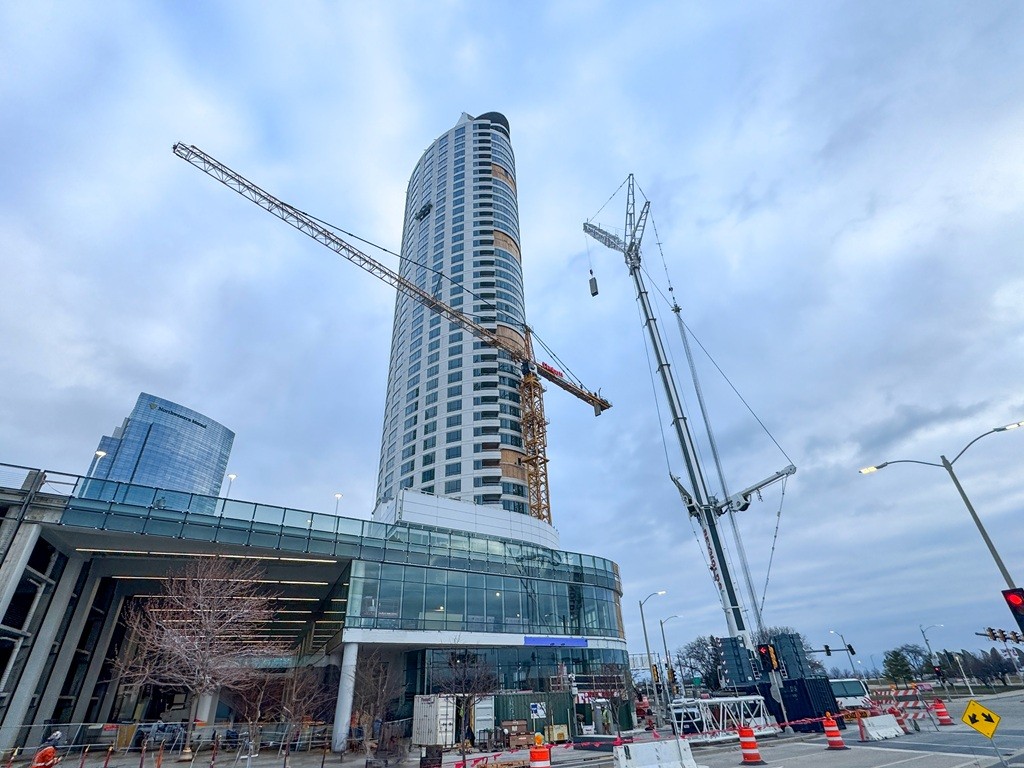
Lifting
20/11/2024
Tadano AC 7.450-1 Performs Double Duty in Wisconsin
A cost-saving and versatile solution was already on site - a...
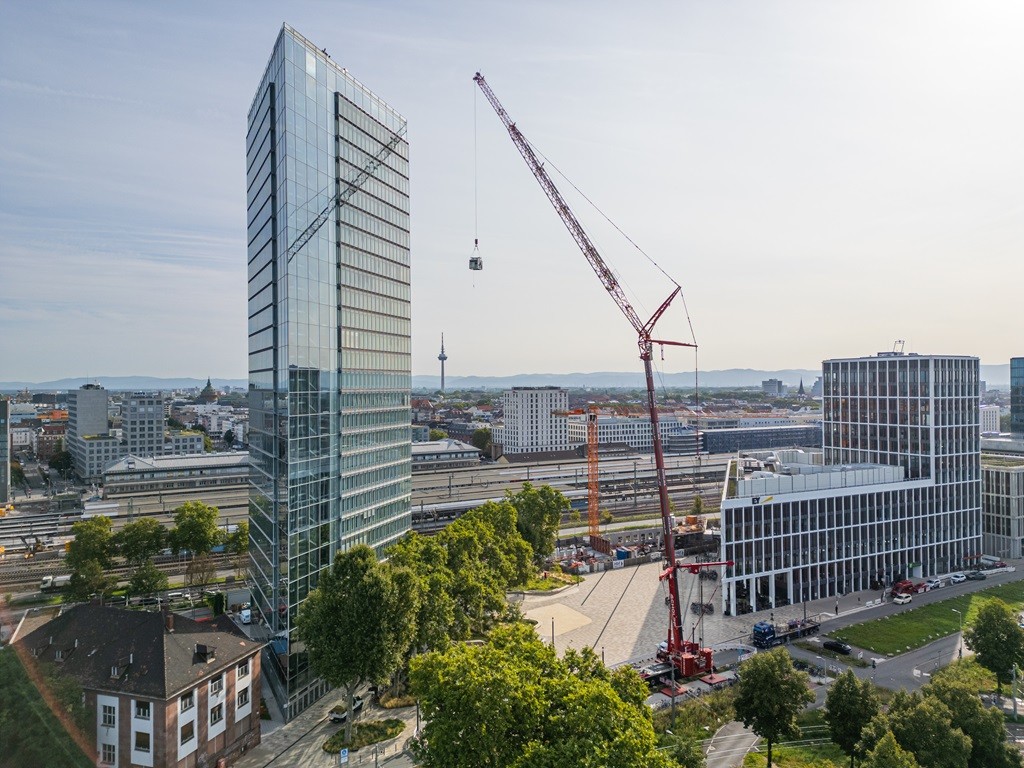
Lifting
11/11/2024
Tadano AC 7.450-1 all terrain crane for the Victoria Tower in Mannheim
Tadano AC 7.450-1 all terrain crane lifts cooling unit to to...
Altri International
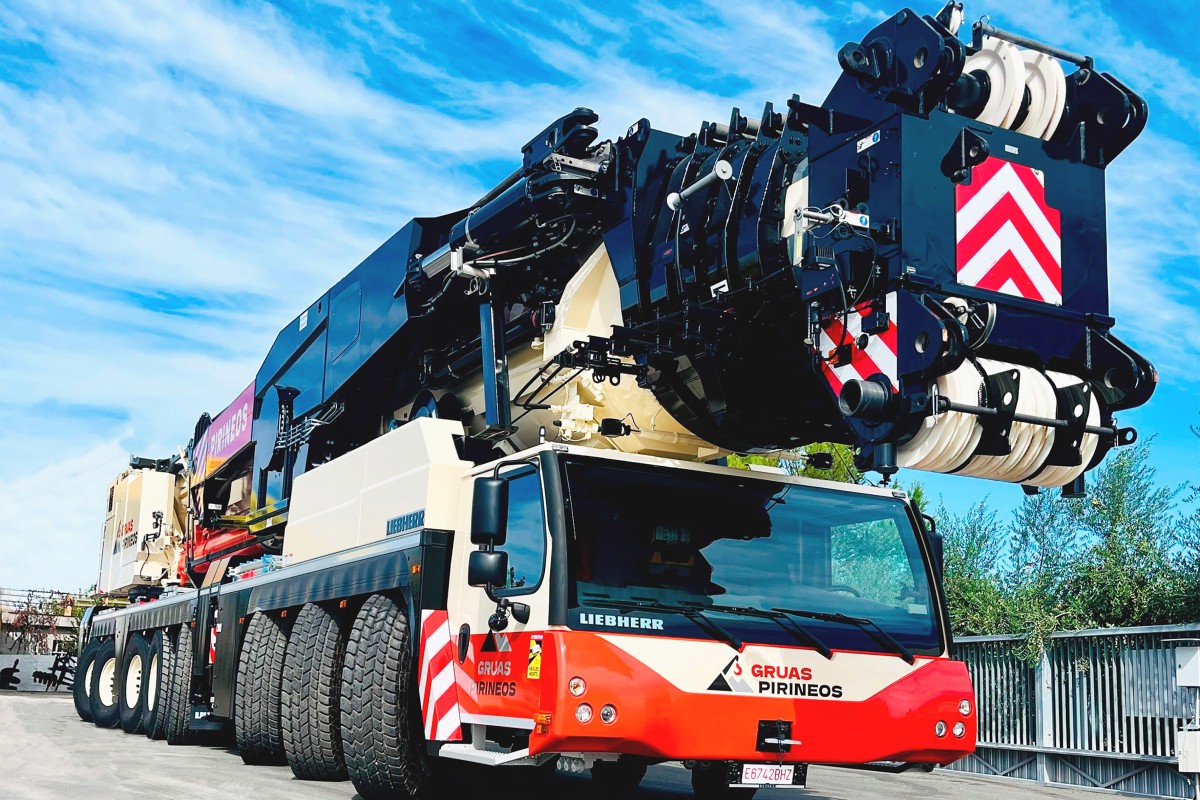
International
29/11/2024
Grúas Pirineos invests in a Liebherr LTM 1650-8.1 mobile crane
For Grúas Pirineos, the purchase of its first Liebherr mobil...
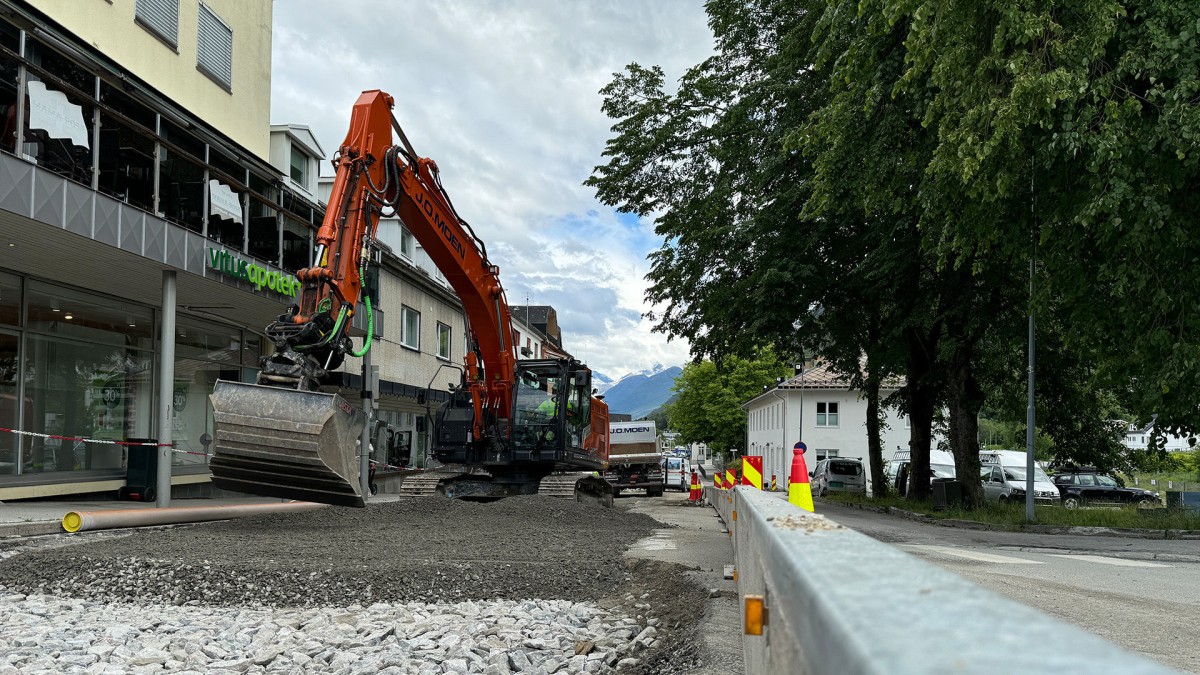
International
28/11/2024
Hitachi's Zaxis-7 excavator is a favourite for Norwegian family-business
Norwegian family business JO Moen AS has added a ZX225USRLC-...
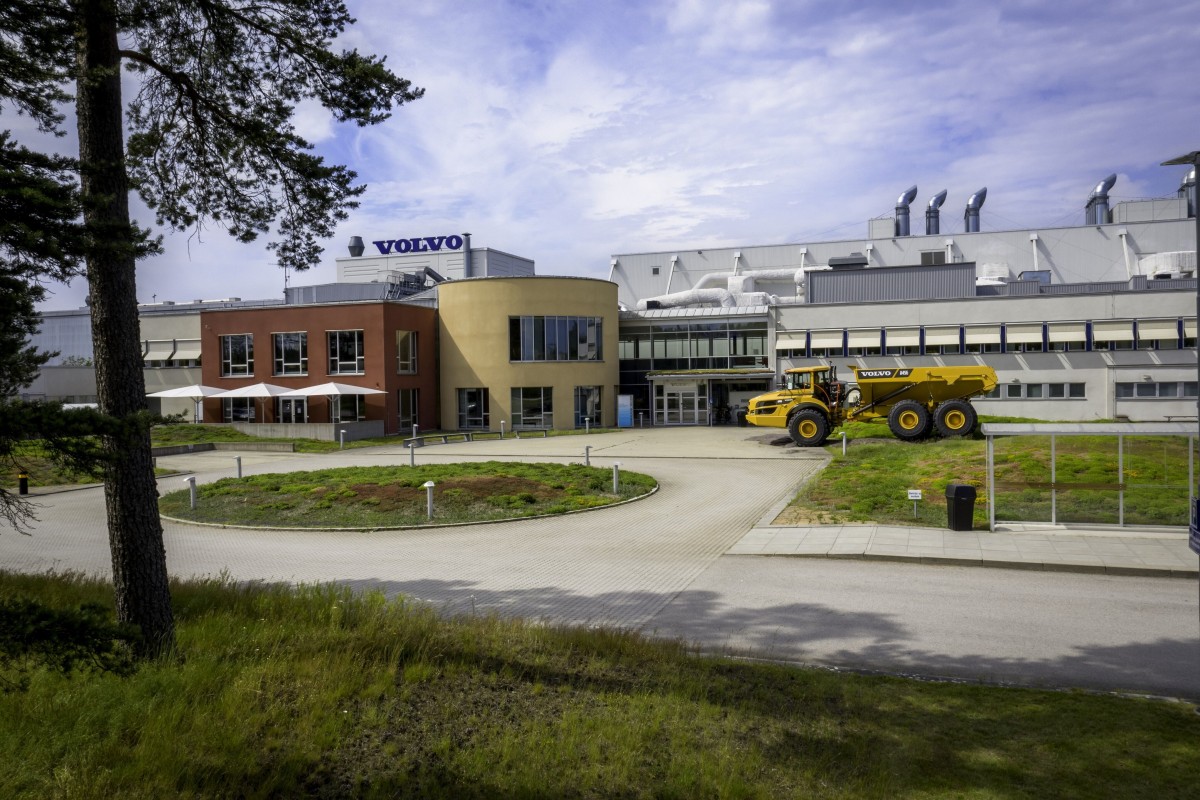
International
27/11/2024
Home of Volvo Construction Equipment’s pioneering articulated haulers advances to Climate Efficient Site
As one of the construction industry’s most active drivers of...
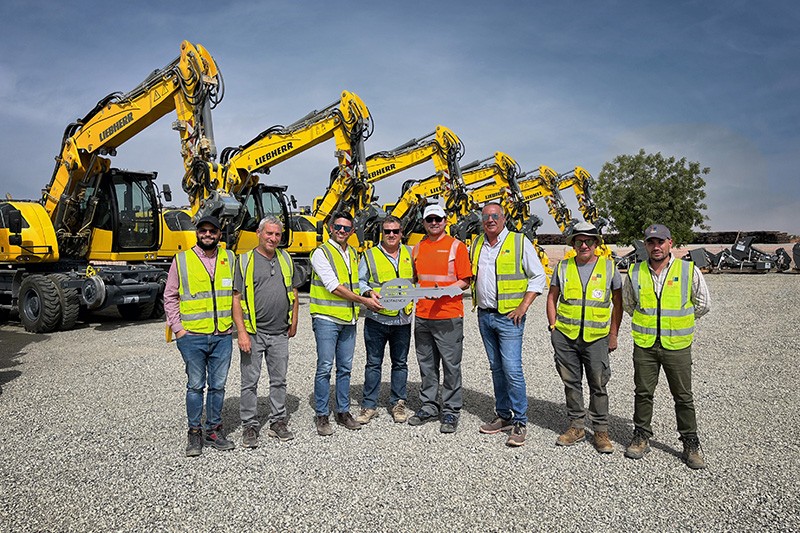
International
26/11/2024
Mota-Engil orders 10 Liebherr railroad excavators for a major project in West Africa
The Portuguese construction company Mota-Engil has once agai...
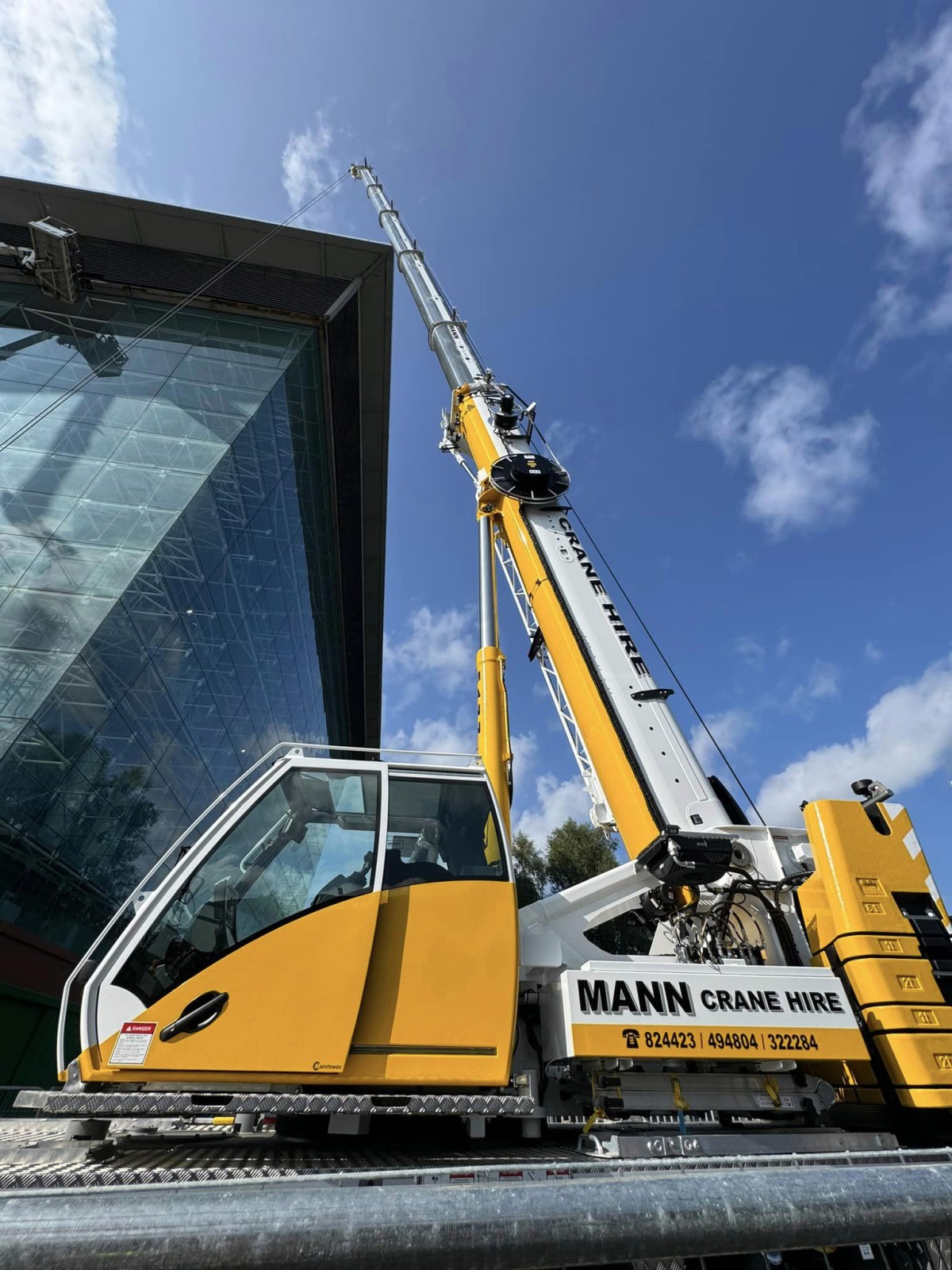
International
25/11/2024
New Grove GMK3060L-1 drives busy schedule for Mann Crane Hire
• Mann Crane Hire selected the GMK3060L-1 for its class-lead...
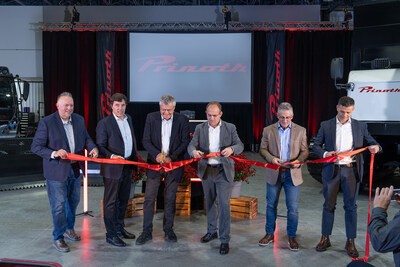
International
25/11/2024
Prinoth Unveils Expanded Production Facility in Granby, Canada
Prinoth held an event to announce the official opening of it...