Home \ International \ One big, bad dozer turns 40
One big, bad dozer turns 40
28/09/2017
Pubblicato da Redazione
Forty years ago this September, Caterpillar rolled off of its production lines 10 pilot models of the world’s largest, most powerful dozer, destined to leave a lasting legacy on the industry. The Cat D10 dozer’s
Forty years ago this September, Caterpillar rolled off of its production lines 10 pilot models of the world’s largest, most powerful dozer, destined to leave a lasting legacy on the industry. The Cat D10 dozer’s radically different design, high weight and horsepower, and resilient undercarriage answered the growing calls from large mining and big heavy construction operations for a more powerful dozer.
“We bucked conventional wisdom with the D10 and tinkered with a centerpiece that was a part of the Caterpillar product line since the company was formed in 1925,” says George Alexander, a retired Caterpillar engineer who served on the D10 research team and one of four individuals named on the patent for Caterpillar’s elevated sprocket design.
The result of the team’s out-of-the-box thinking was a machine with no rival for weight, power or productivity. Offering 50 percent higher productivity than Caterpillar’s largest dozer of that era, the D9 dozer, the D10 weighed over 190,000 lb (86 180 kg) and measured 15 ft (4,6 m) tall, 12 ft (3,7 m) wide and slightly more than 31 ft (9,4) long. Power was supplied by the 700 hp (522 kW) D348, V12 diesel engine.
A changing industry in the late 1960s and early 1970s stretched the D9 to its productivity limits, and the mining industry led the charge for a dozer with more and more horsepower. Contractors working in predominantly hard rock applications also demanded a design that improved track longevity and durability. “The D9 dozer was the best track-type tractor of the day,” adds Alexander. “It worked great for dirt operations, but interstate and heavy rock applications were hard on the solid bottom tracks that were a part of all dozer designs of that era.”
To address the market’s needs, Caterpillar tapped a team of Research and Engineering personnel to develop a new, more powerful dozer, the D10. “The development and product introduction involved every discipline of the company. It was highly successful because of the total team effort. The challenge of beating the competition in our core product was a tremendous incentive,” recalls Ron Krolak, track-type tractor chief engineer, retired. The D10 research team established a set of design goals for the new dozer: high productivity; modular design; simplified maintenance; operator efficiency; and transportability. It quickly became evident that a new track design and improved undercarriage were needed to meet the production and durability goals for the new dozer. With management approval in 1970, a test bed was built for the new track. Engineers started by flipping the final drive for a D9G upside down. “We worked on undercarriage geometry a lot, and within six months we had it operational,” says Alexander. The new resilient track with elevated sprocket design was tested thoroughly in multiple demanding applications to verify its durability, and it showed significant potential for improving undercarriage durability for extreme tasks.
Two years of testing led to the first elevated sprocket patent application and ultimately building the first two D10 test models in August of 1973. “Our team generated 93 patents involving all systems of the concept,” adds Krolak. By separating the drive sprockets from the track roller frame and elevating them above the tracks, more track remained on the ground for improved traction. The elevated sprocket design was also better able to absorb ground shocks for longer life and greater operator comfort.
While initial testing proved the efficacy of the resilient undercarriage with elevated sprocket design, there were still some skeptics of the new design. “It didn’t look like any traditional Cat dozer,” explains Alexander. “The entire dozer was different in almost every way, except for the engine.”
Beyond looking different, the new undercarriage design required the transmission to be mounted behind the engine to provide for the only track-type tractor final drive system with a common centerline between the steering clutches and brakes. It also allowed engineers to move both the dozer blade and ripper closer to the tractor, providing a concentrated center of gravity and improving the balance of the machine.
The pilot D10 dozers built in 1977 were immediately embraced by Caterpillar customers. Their ripping and pushing capabilities made a significant impact on the mining industry, as studies showed the cost/yard to move material using the D10 was comparable to that of larger draglines. The resilient undercarriage with elevated sprocket conformed to the ground better than solid tracks, helping to improve machine pushing power and undercarriage life and enhancing operator comfort.
The dozer’s modular concept helped to increase machine transportability, as removable components facilitated machine moves from location to location. Its modular design also substantially advanced assembly and service task efficiency. The transmission and bevel gear removal and installation times on the D10 compared to that of the D9H dropped to 6 hours from 30 hours, while service time on the final drive plummeted to 9 hours from 45 hours, lowering long-term operating costs.
The original big and bad Cat D10 legacy lives on today with thousands of Caterpillar elevated sprocket dozers operating around the world. The elevated sprocket track concept has been expanded to today’s Cat D6N and D6T medium dozers and the D8T, D9T and D11T large dozer models as well as the current D10T2 model. “After I retired in the 1990s, I gave my presentation on the development of the elevated sprocket design, and a person afterwards said to me, ‘Wherever you go, you will see the results of your work,’” recalls Alexander. “He was right. No matter where I traveled in the world, I saw dozers with the elevated sprocket design, and it made me proud to be a part of the original research team.”

Ultime notizie di Caterpillar - CGT
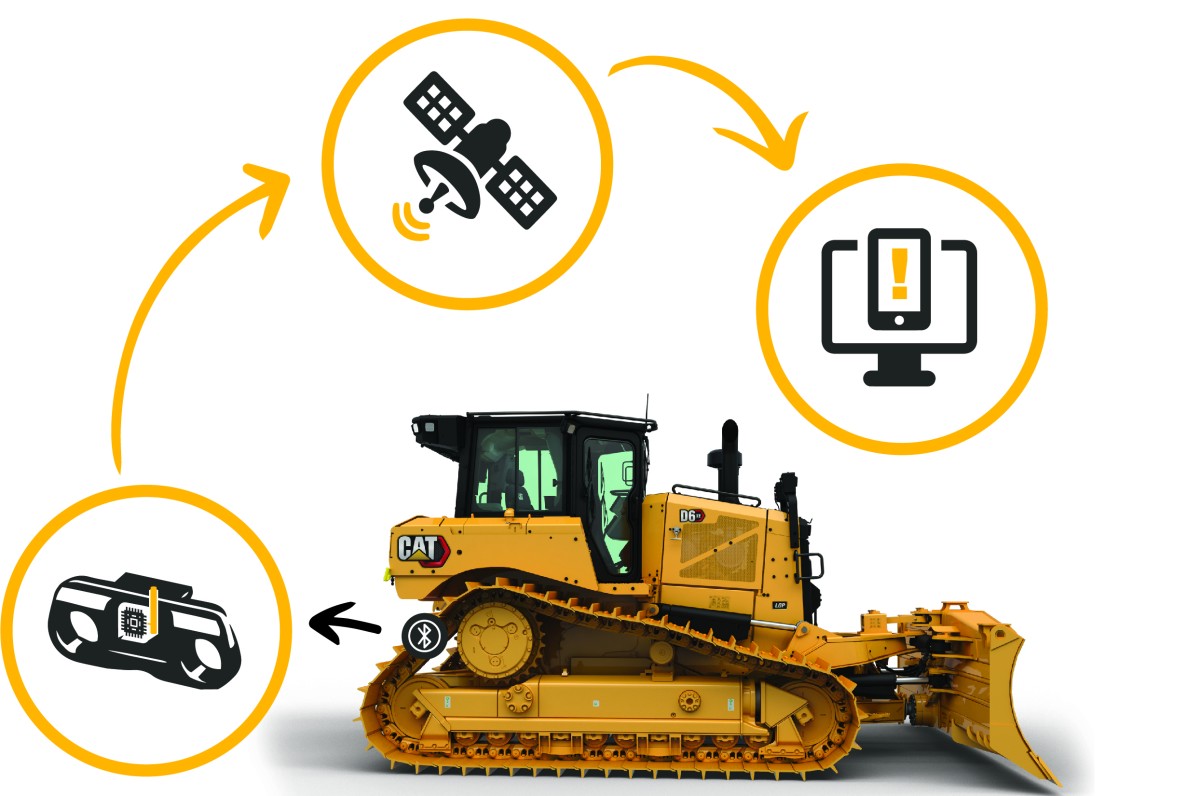
Components
26/07/2024
Exclusive new Cat Track Wear Sensor
Exclusive new Cat Track Wear Sensor provides remote, no-touc...

Earthmoving Machinery
18/01/2024
Caterpillar Signs Strategic Agreement with CRH
Caterpillar Signs Strategic Agreement with CRH for Electric...

Earthmoving Machinery
06/12/2023
Caterpillar to Amplify Electrification and Energy Solutions at CES 2024
This year’s display focuses on Caterpillar’s electric machin...

Components
27/11/2023
Caterpillar to Develop Hydrogen-Hybrid Power Solution for Off-Highway Vehicles
Starting in early 2024, the advanced hydrogen-hybrid project...

Earthmoving Machinery
10/11/2023
Freeport-McMoRan uses Cat MineStar to convert fleet
Caterpillar and Freeport-McMoRan (FCX) announce that the two...
Earthmoving Machinery
13/10/2023
Caterpillar celebrates production of the 50,000th Cat Wheel Excavator
Caterpillar announces production of its 50,000th wheel excav...
Altri International
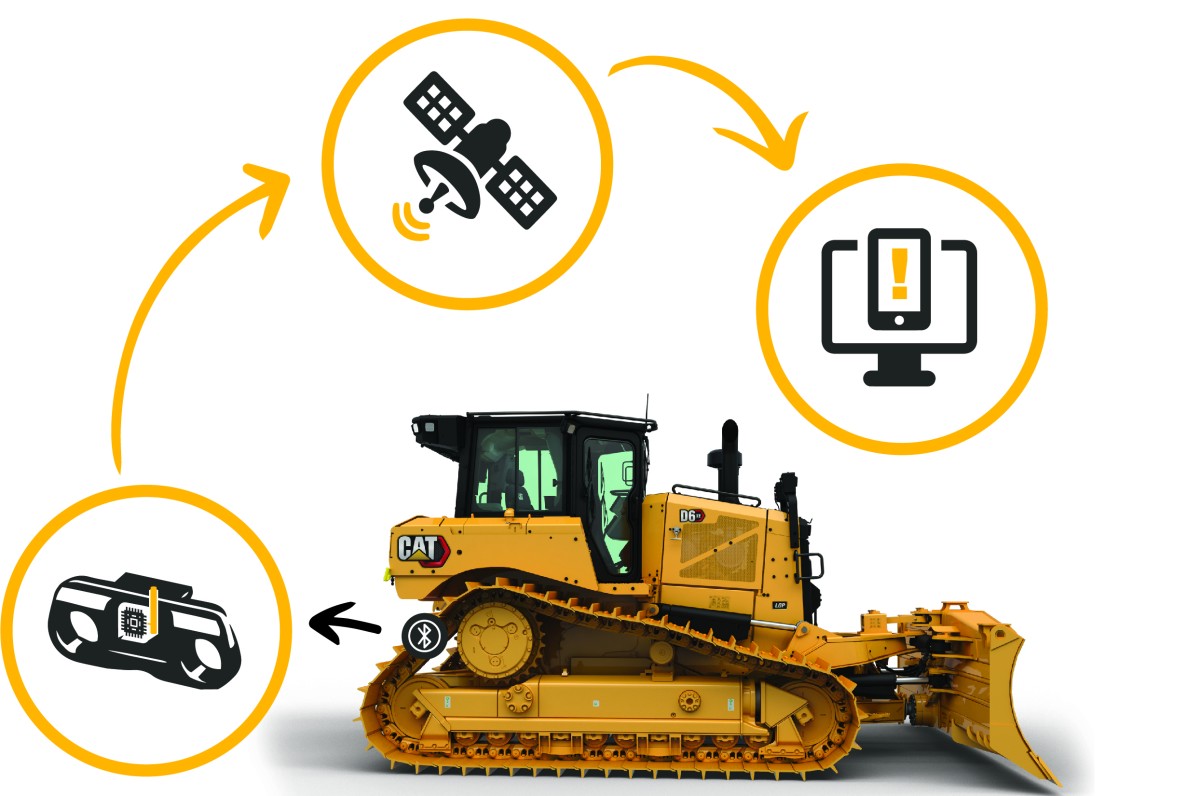
International
26/07/2024
Exclusive new Cat Track Wear Sensor
Exclusive new Cat Track Wear Sensor provides remote, no-touc...
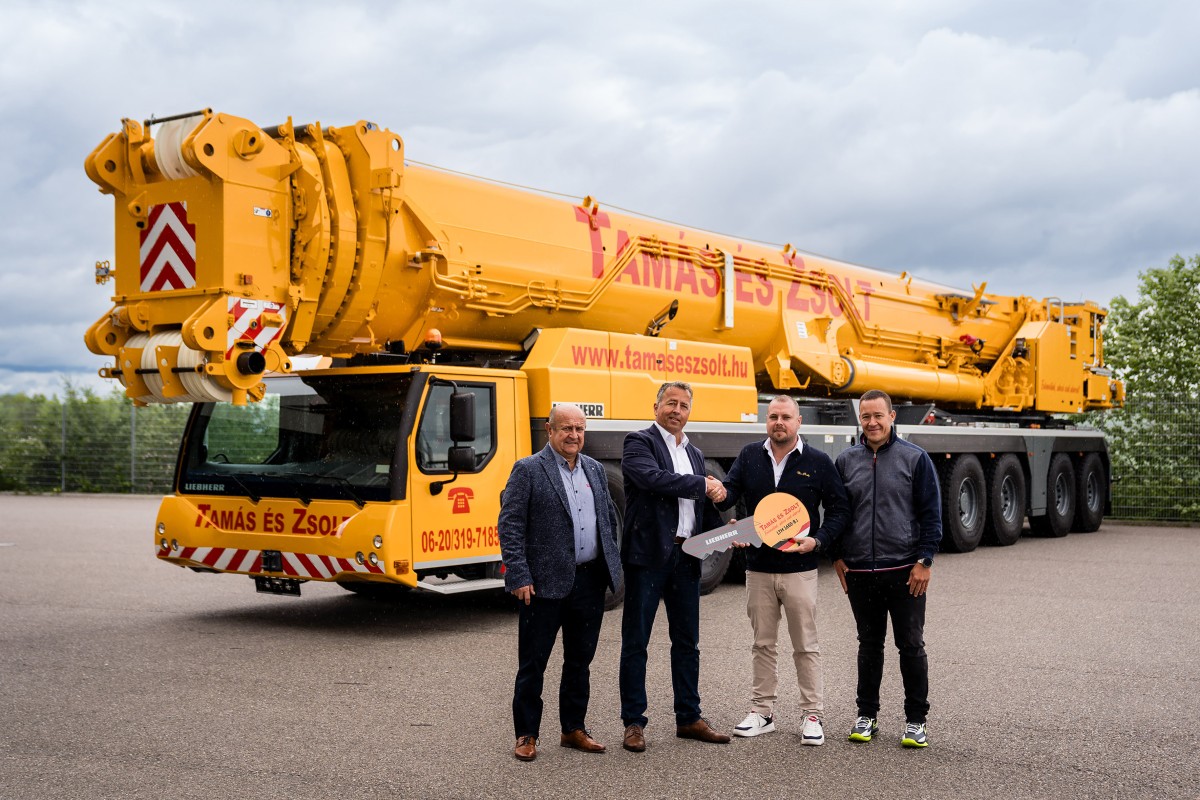
International
26/07/2024
Tamás és Zsolt Kft. took delivery of Liebherr LTM 1650-8.1
Tamás és Zsolt Kft. has added a Liebherr LTM 1650-8.1 to its...
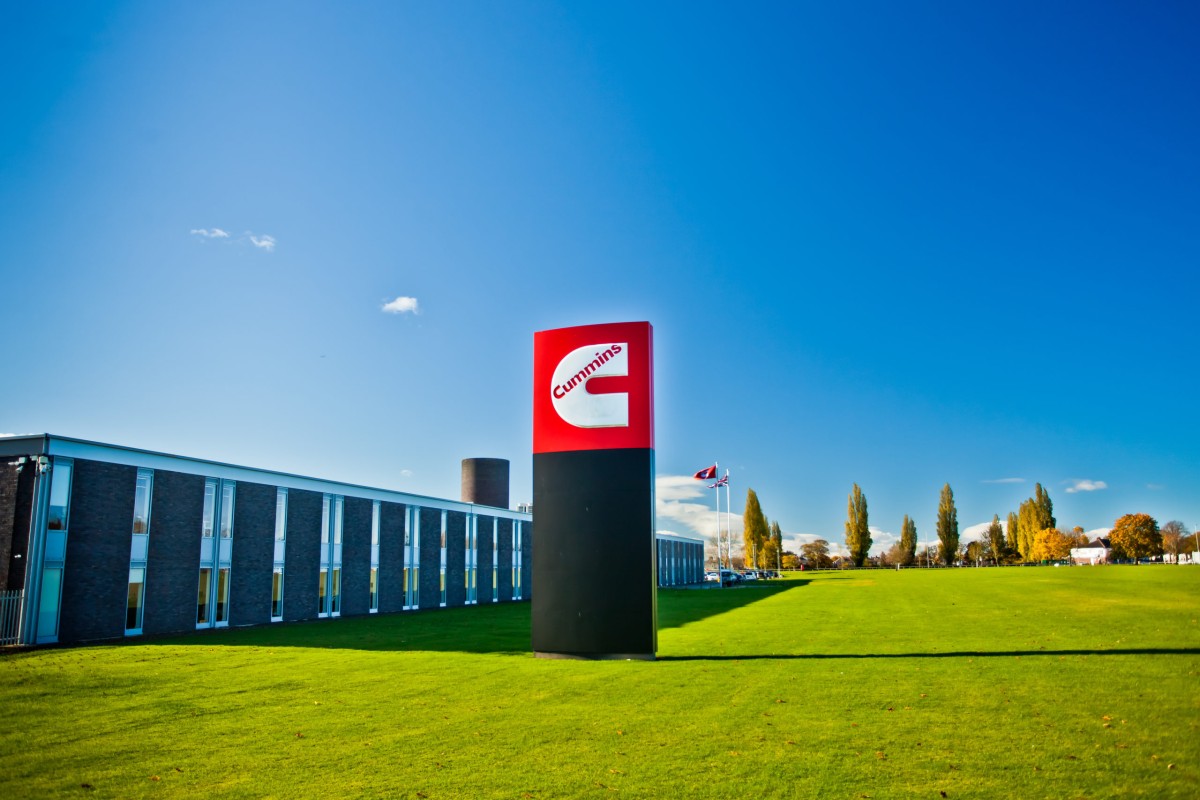
International
25/07/2024
Cummins opens new powertrain test facility
Cummins has opened a new powertrain test facility to support...
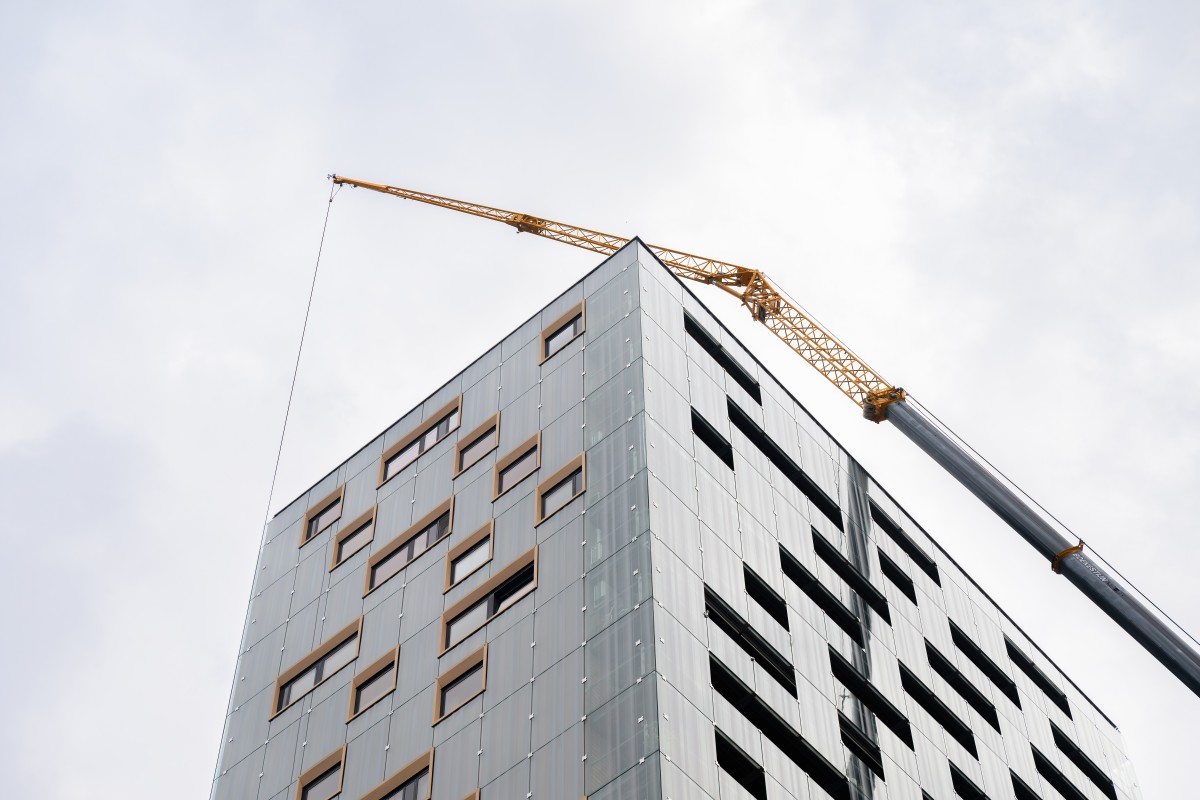
International
25/07/2024
Grove GMK6300L-1 proves perfect for compact jobsite in Rotterdam
Kraanverhuur Boekestijn sent its Grove GMK6300L-1 for city c...
International
24/07/2024
MB Crusher breaks records and crushes challenges
MB Crusher is proud to support the construction of arenas, s...
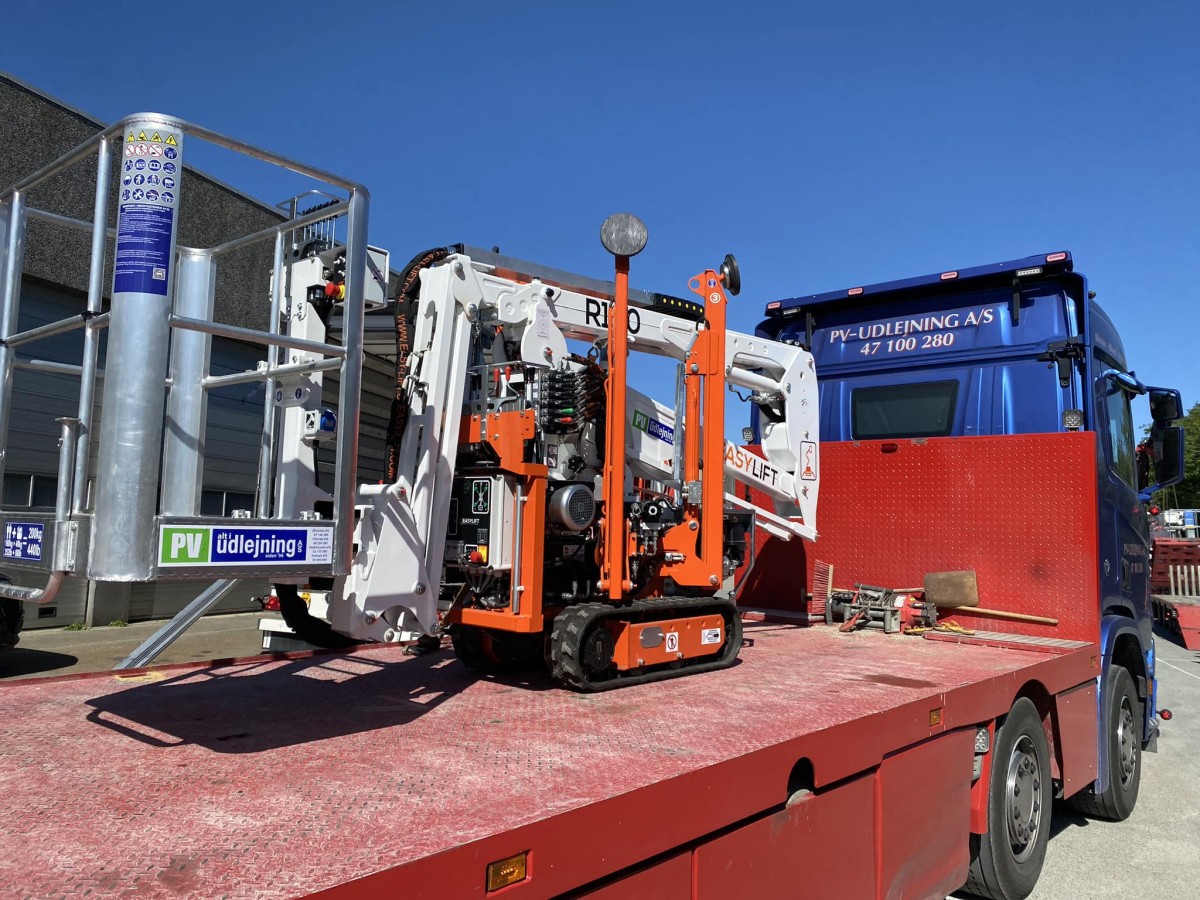
International
24/07/2024
Hammer Lifte makes a full load of deliveries of Easy Lift spiders
Easy Lift's Danish dealer, Hammer Lifte, is always busier to...