Home \ International \ Rope and Sling continues testing and inspection at King’s Lynn Power Station
Rope and Sling continues testing and inspection at King’s Lynn Power Station
28/12/2018
Pubblicato da Redazione
Rope and Sling Specialists (RSS) has completed the latest in a series of testing and inspection assignments at King’s Lynn Power Station, as investment into the 370-megawatt facility in Norfolk, UK continues.
Rope and Sling Specialists (RSS) has completed the latest in a series of testing and inspection assignments at King’s Lynn Power Station, as investment into the 370-megawatt facility in Norfolk, UK continues.
The lifting and rigging equipment company, which has been a frequent visitor to the site near the North Sea coast this year, has completed proof load testing of a lifting beam and inspection of a 2.5t capacity Hadef chain hoist installed on a 52m-long runway. The equipment is located 25m up an air-cooled condenser (ACC) building.
RSS accepted the scope of work from Poland-based MKL Bau to complete the testing and inspection procedures upon completion of installation by another company. The necessary tasks were executed by Gary Coleman, site engineer; and Mick Gill, senior testing engineer, both based at RSS’s Rotherham depot to the northwest of the power plant.
Coleman explained that the beam and hoist are used for removing motors for service and repair. The hoist can trolley to the outside of the approx. 30m-high building, lower to ground level, and complete the process in reverse. RSS is familiar with the lifting equipment typically installed in ACC buildings—and has learnt from experience.
Coleman said: “We used the steel structure either side of the walkway to pull against using chain slings, as an alternative to using live weights, to carry out a deflection test. This method saves a substantial amount of money in transportation and time using such weights. This is a practice we devised on a previous job at an ACC in Harrogate [Yorkshire, UK].”
The RSS pair employed a manual chain block and an electric chain hoist (the latter was supplied by the power station) to achieve deflection with a load and hoist weight. A load cell was also utilised to measure a safe working load (SWL) of 2.5t and 3.125 proof load. At ground level, meanwhile, a telehandler was employed to carry out a deflection test of a cantilevered beam, again to save the costs associated with the use of live weights.
RSS carried out aforementioned assignments for the same customer in May this year; it also completed onsite testing of a temporary lifting beam to facilitate assembly of ACC ducting two months later. The requirement for specialist lifting and rigging services has been a constant during a long-term investment programme into new flexible power plants across the country.
Coleman concluded: “The King’s Lynn Power Station is another example of a high profile site committing to exemplary best practices related to lifting and rigging gear, where only experts in the field should be sought for any matters involving installation, periodic inspection, testing, maintenance, and other related activities.”

Ultime notizie di OnSite News
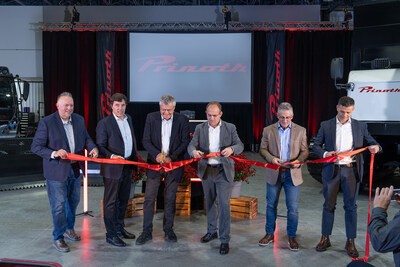
Earthmoving Machinery
25/11/2024
Prinoth Unveils Expanded Production Facility in Granby, Canada
Prinoth held an event to announce the official opening of it...
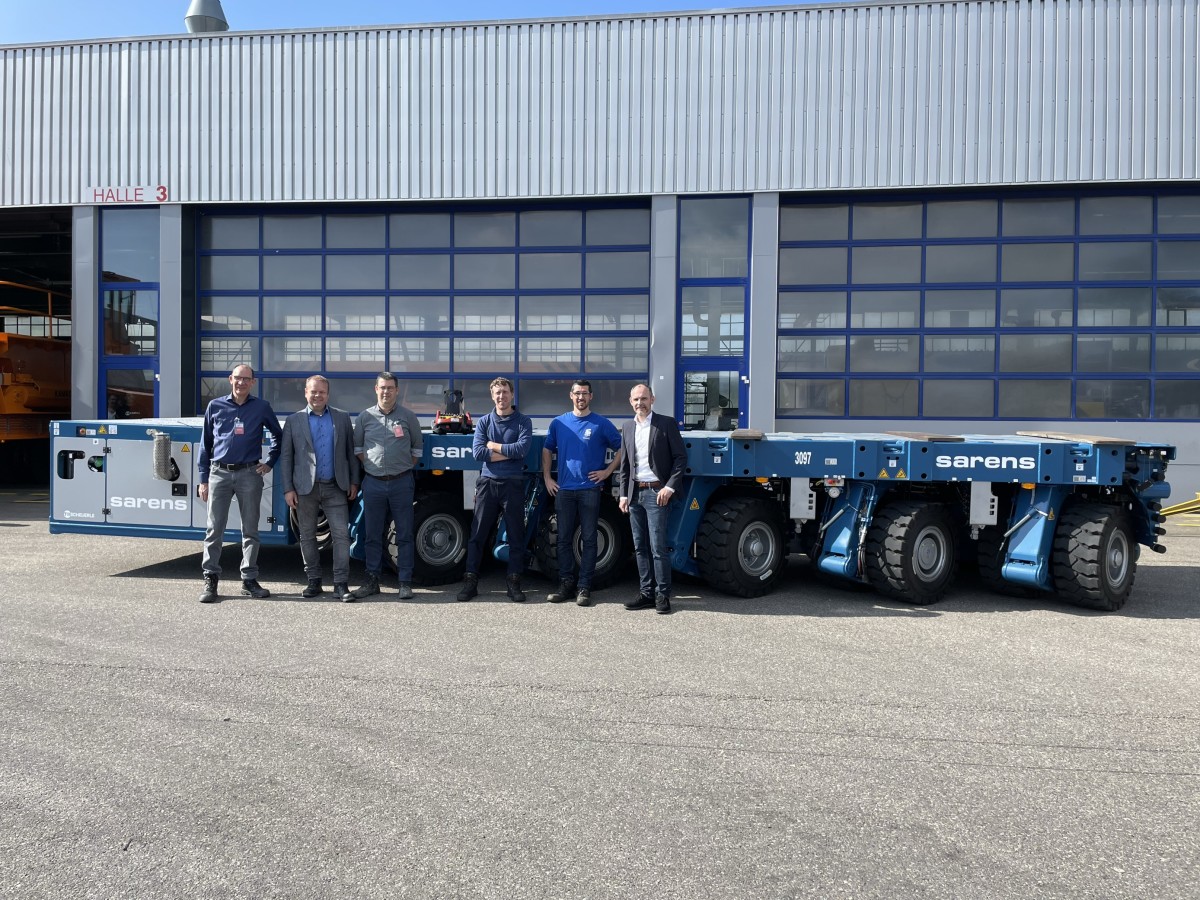
Logistics
22/11/2024
Sarens acquires additional SCHEUERLE SPMT K24 modules
renowned for its expertise in crane rental services, heavy l...
Equipments
21/11/2024
SITECH partners with Royal Engineers to create poppy and demonstrate tech offering
The demostration involved creating a ground-level poppy desi...
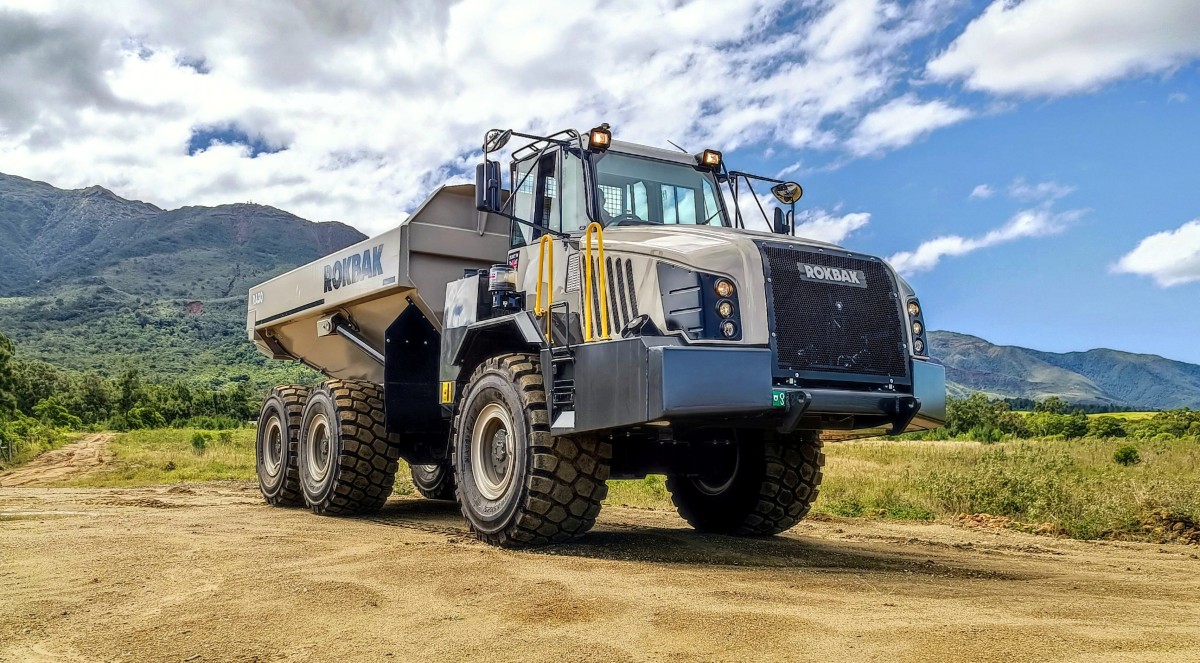
Earthmoving Machinery
20/11/2024
Strong and stable RA30 trucks carry the weight at New Caledonian mine
Three Rokbak RA30 trucks are delivering exceptional durabili...
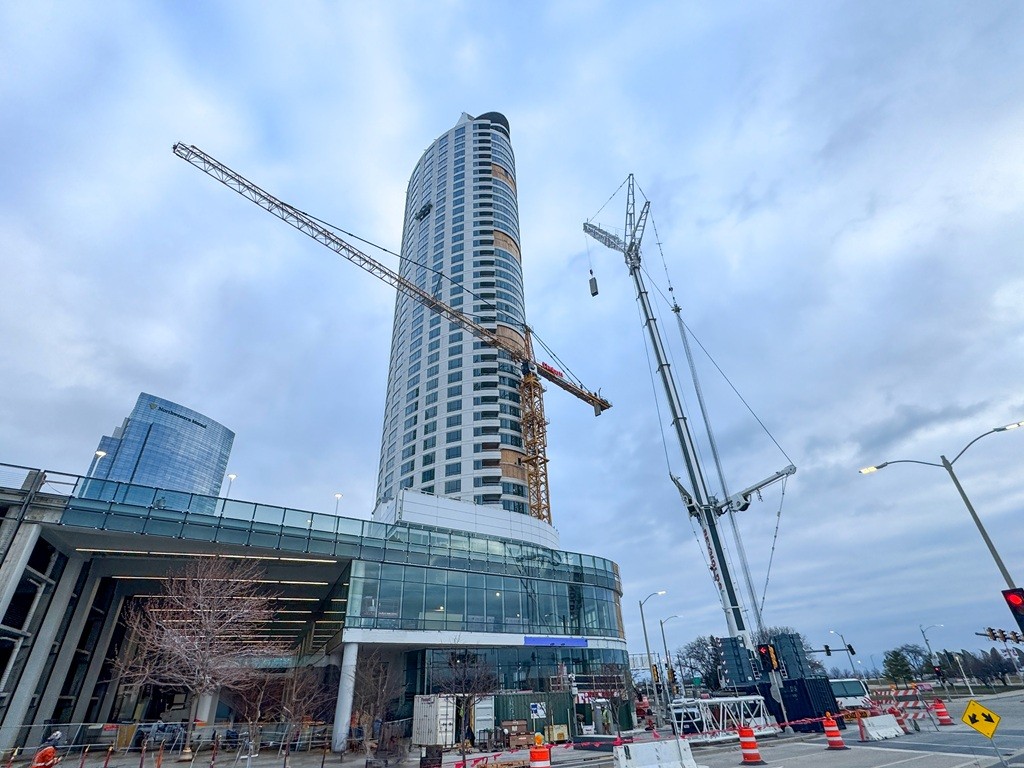
Lifting
20/11/2024
Tadano AC 7.450-1 Performs Double Duty in Wisconsin
A cost-saving and versatile solution was already on site - a...
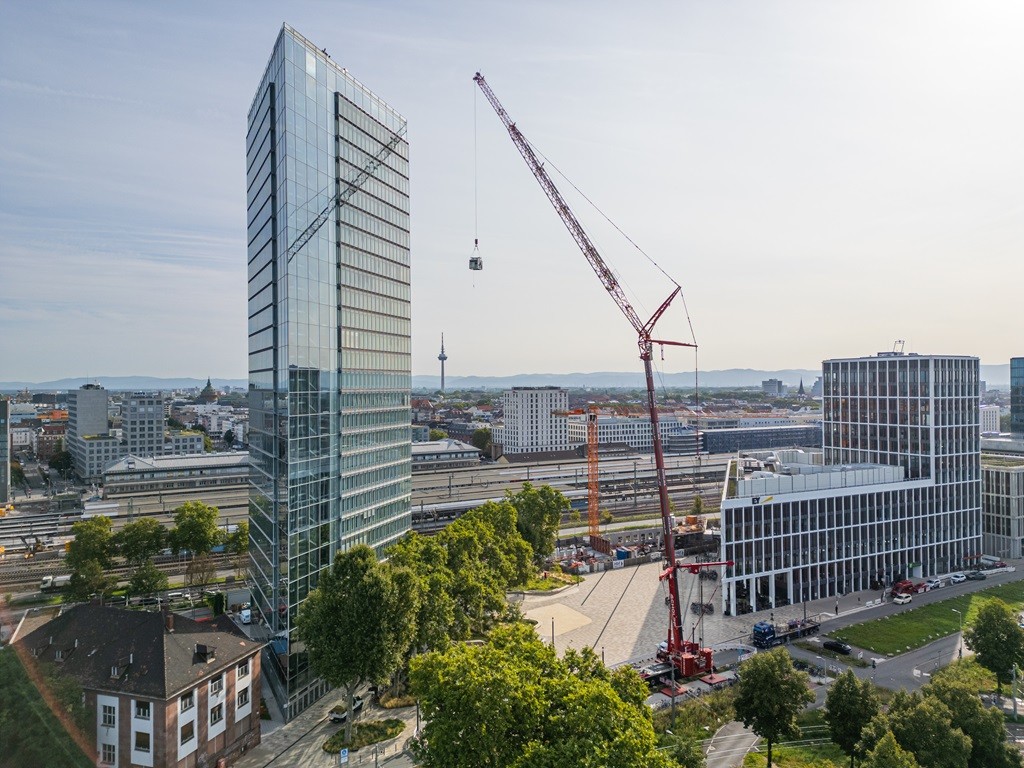
Lifting
11/11/2024
Tadano AC 7.450-1 all terrain crane for the Victoria Tower in Mannheim
Tadano AC 7.450-1 all terrain crane lifts cooling unit to to...
Altri International
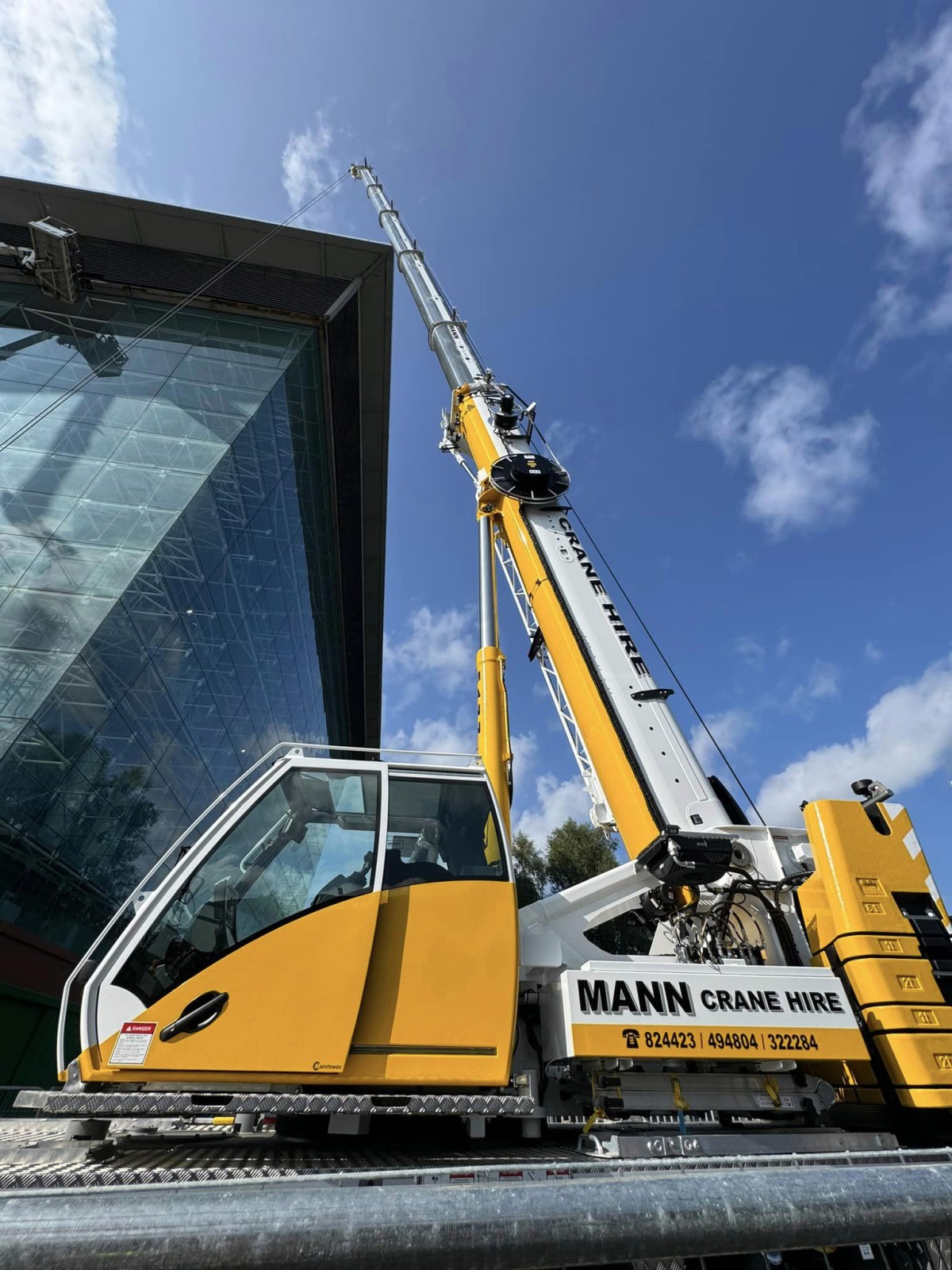
International
25/11/2024
New Grove GMK3060L-1 drives busy schedule for Mann Crane Hire
• Mann Crane Hire selected the GMK3060L-1 for its class-lead...
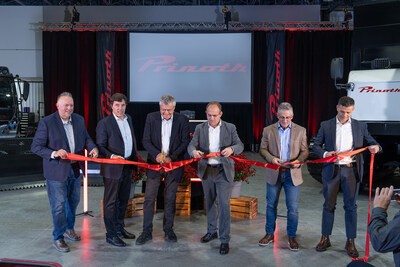
International
25/11/2024
Prinoth Unveils Expanded Production Facility in Granby, Canada
Prinoth held an event to announce the official opening of it...
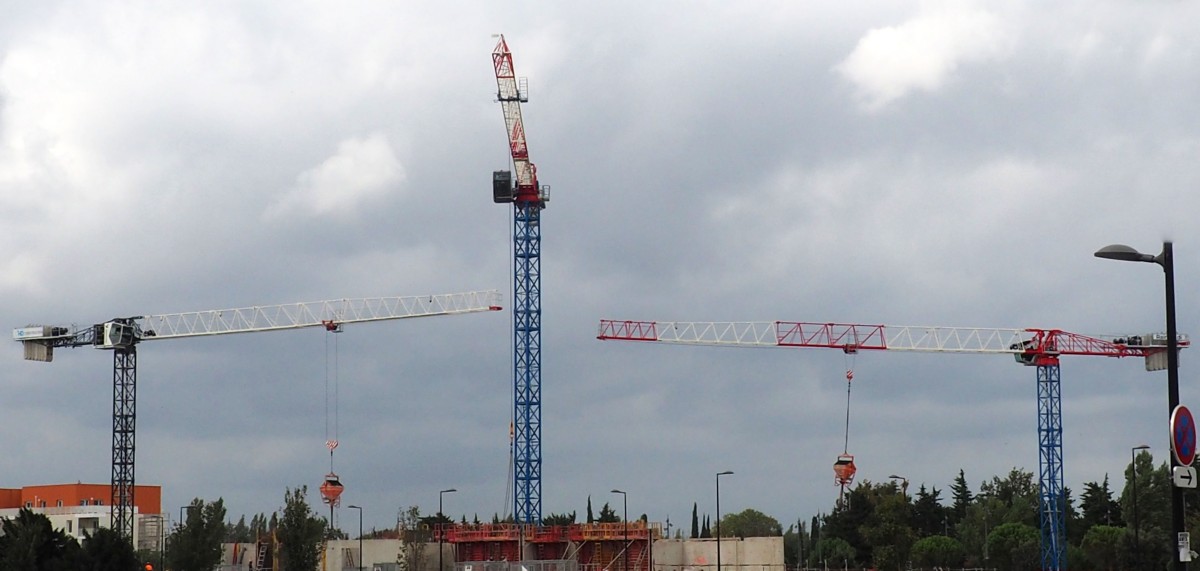
International
23/11/2024
GPMat International takes delivery of two Raimondi T147s residential development in the South of France
- Official agent of France expands its product lineup with t...
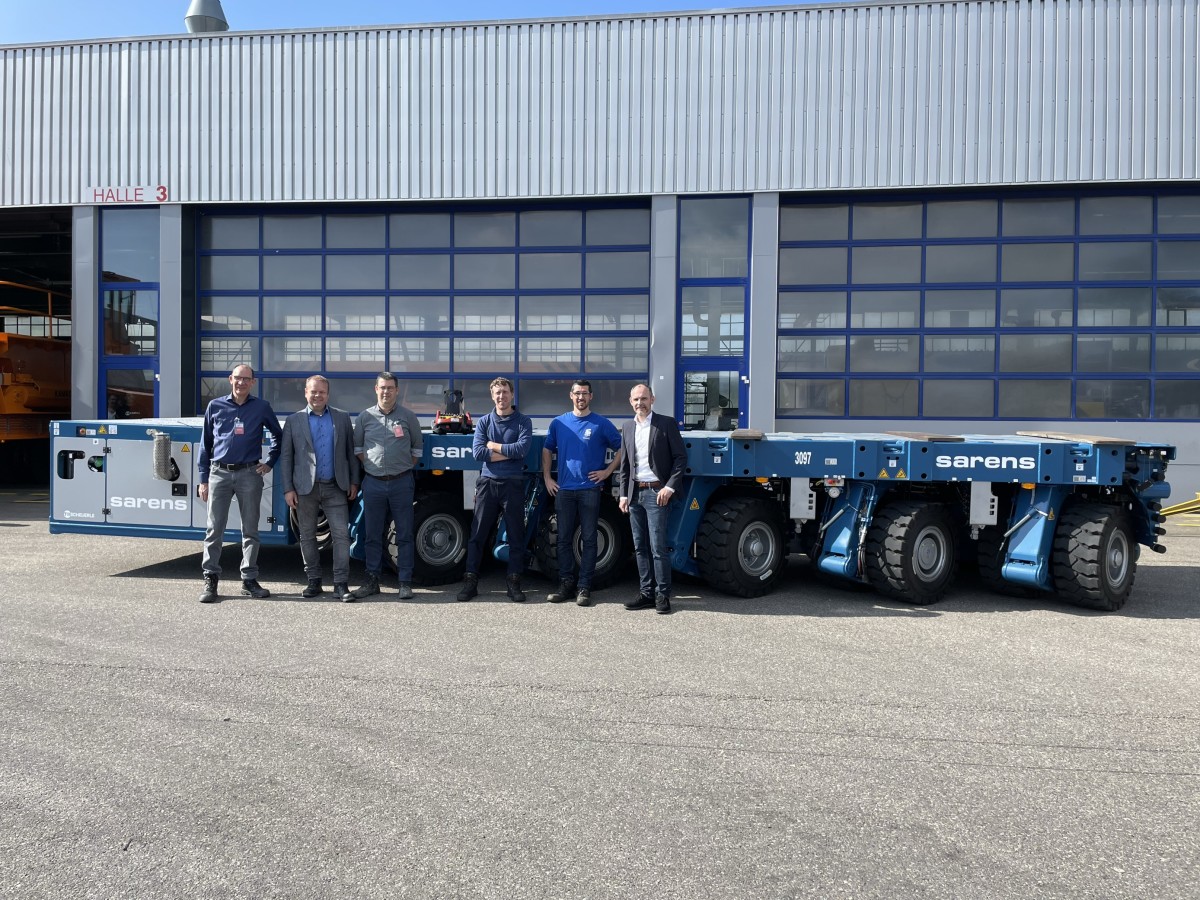
International
22/11/2024
Sarens acquires additional SCHEUERLE SPMT K24 modules
renowned for its expertise in crane rental services, heavy l...
International
22/11/2024
Five WOLFF cranes modernize Oslo’s Ulven district
With a total of five WOLFF cranes of type 7534.16 Clear, Wol...
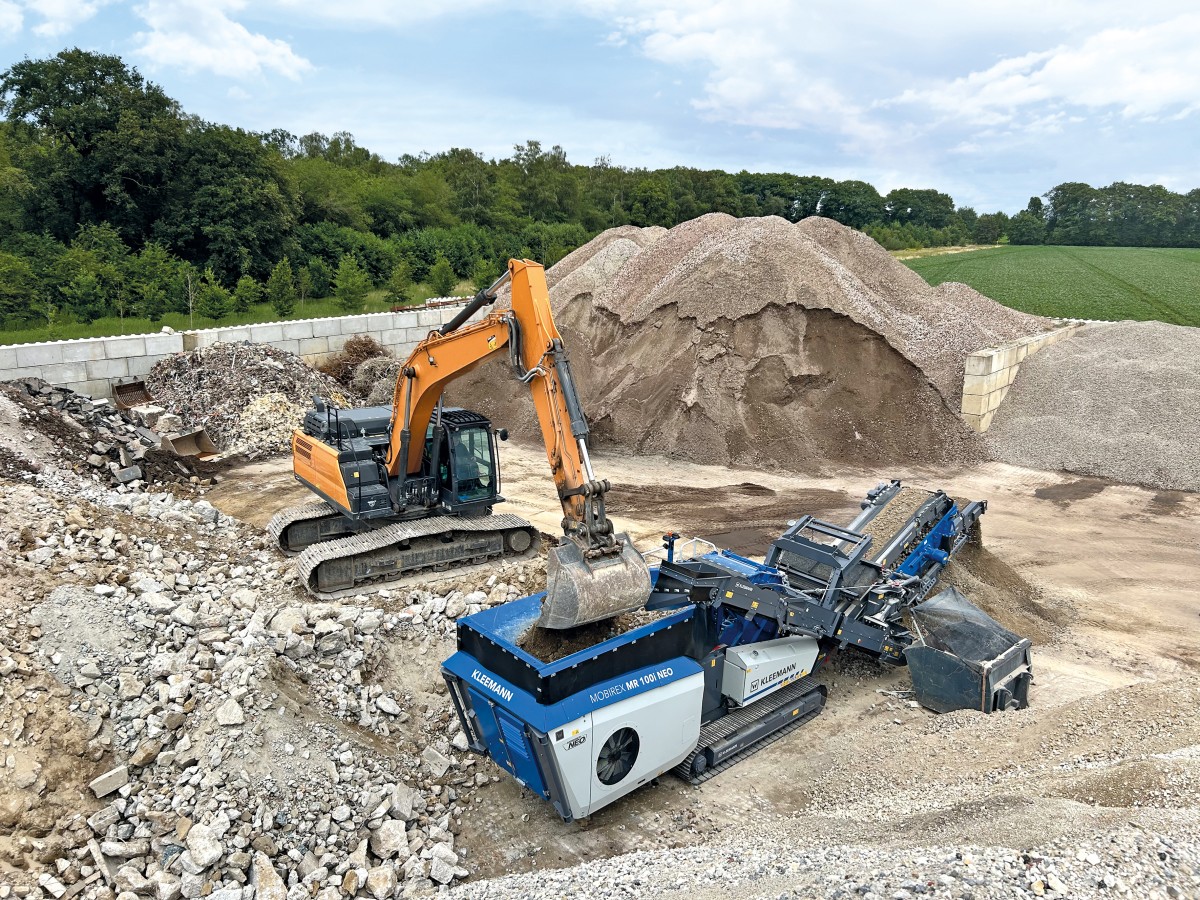
International
21/11/2024
Kleemann: New compact crusher used for recycling
Impact crusher MOBIREX MR 100i NEO impresses during operatio...