Home \ International \ Technology integrated in compact milling machines of the F-Series
Technology integrated in compact milling machines of the F-Series
03/07/2023
Pubblicato da Ettore Zanatta
The new Wirtgen W 100 Fi did a great job in a very confined space. It took only two passes with the 1 m wide milling drum to remove the entire asphalt package.
Small to medium-sized construction sites in inner-city areas often give rise to challenging situations in terms of navigating obstacles and offloading material. In the rehabilitation of an almost 2 m wide cycle lane in Aachen, the new W 100 Fi did a great job in a very confined space. It took only two passes with the 1 m wide milling drum to remove the entire asphalt package. The construction site project was completed in a very short time, allowing the lane to be quickly reopened for cycling traffic.
On the narrow cycle lane, the W 100 Fi compact milling machine from Wirtgen proved both its power and flexibility. The F-Series technology, previously only available for large milling machines, provided support for the operator and made working on the site easier and more convenient.
Optimum visibility of the area in front of the milling drum unit enabled close navigation up to and around objects built into the surface to be milled, with flush milling up to the edges of unpaved verges. Thanks to the milling drum at the rear of the machine, the operator was able to position the start of each cut with ease and precision. The laterally adjustable operator’s platform and the movable roof allowed the machine to approach the lampposts along the route particularly closely and safely from the side. The discharge conveyor with a large slewing angle of 65 degrees to each side made offloading between lampposts and wayside bays much easier. A real benefit for truck transport logistics: material loading in the direction of travel.
In automatic mode, the innovative Mill Assist machine control system always selects the operating strategy that strikes the best balance between performance and costs. Process optimisation functions automatically adjust the engine and milling drum speeds, the travel drive, the water spraying system, and the machine’s advance speed. By pre-selecting the ECO operating strategy, the operator was able to concentrate entirely on the working environment, steering the machine and offloading the milled material. The semi-automatic Active Conveyor slewing angle control system also helped by reliably aligning the discharge conveyor in the direction of the transport truck when the milling machine had to steer around obstacles in its path.
Working closely with John Deere, an engine was adapted specifically for use in a road milling machine for the first time. The six-cylinder in-line engine runs in an extended speed range. The engine already delivers sufficient torque at engine speeds of 1,200 rpm, achieves maximum torque at 1,500 rpm, and offers a very wide working speed range of between 1,200 and 2,100 rpm. All in all, this guarantees lower fuel consumption and fast, productive work, even at maximum milling depths.
Thanks to the compact dimensions of the W 100 Fi, it was easy to transport the milling machine to the job site in Aachen. Another advantage lies in the ease of access for servicing work. All service and maintenance points are conveniently located within reach from the ground, and the new, ergonomically designed footstep considerably increases operator comfort. The Wirtgen compact milling machines of the F-Series represent a new generation of economical and sustainable cold milling machines for a wide variety of applications on small to medium-sized construction sites.

Ultime notizie di Wirtgen Macchine
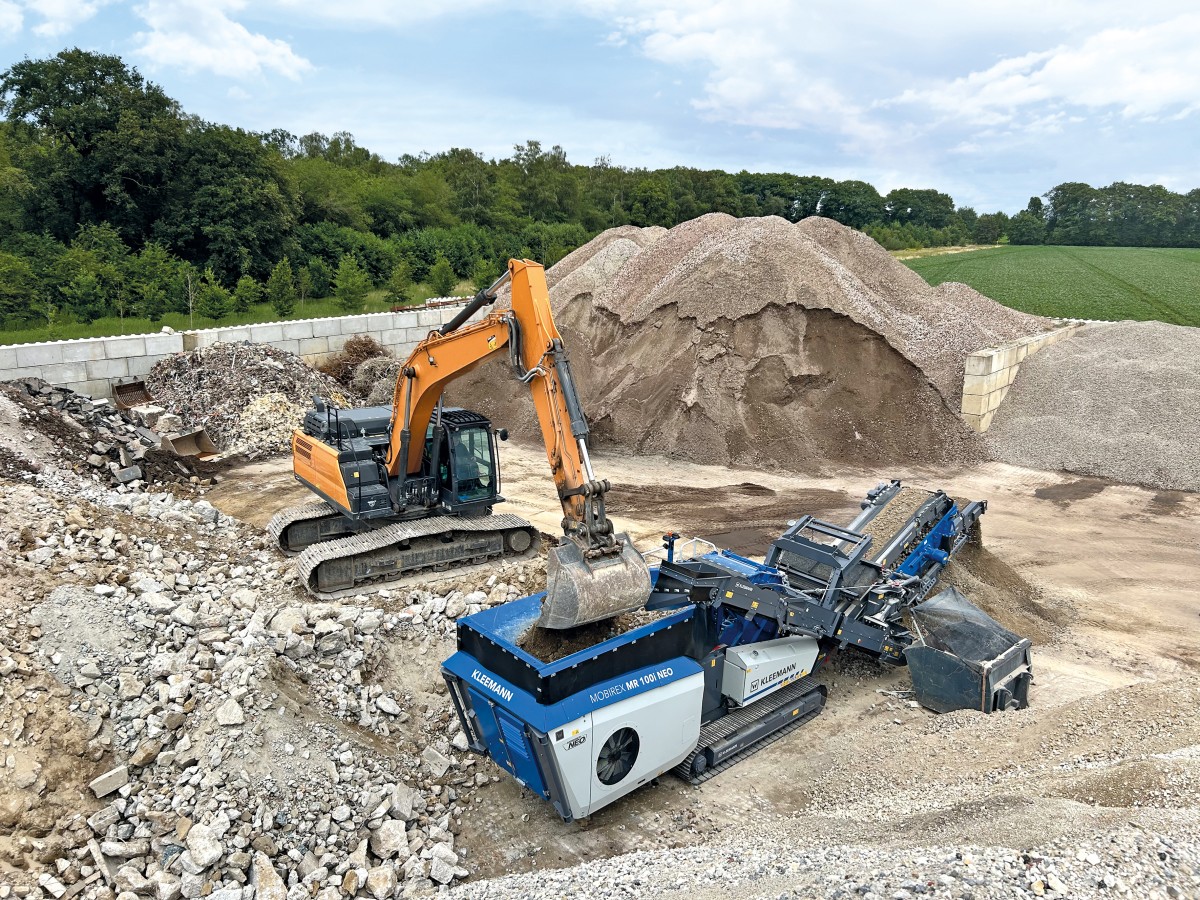
Earthmoving Machinery
21/11/2024
Kleemann: New compact crusher used for recycling
Impact crusher MOBIREX MR 100i NEO impresses during operatio...
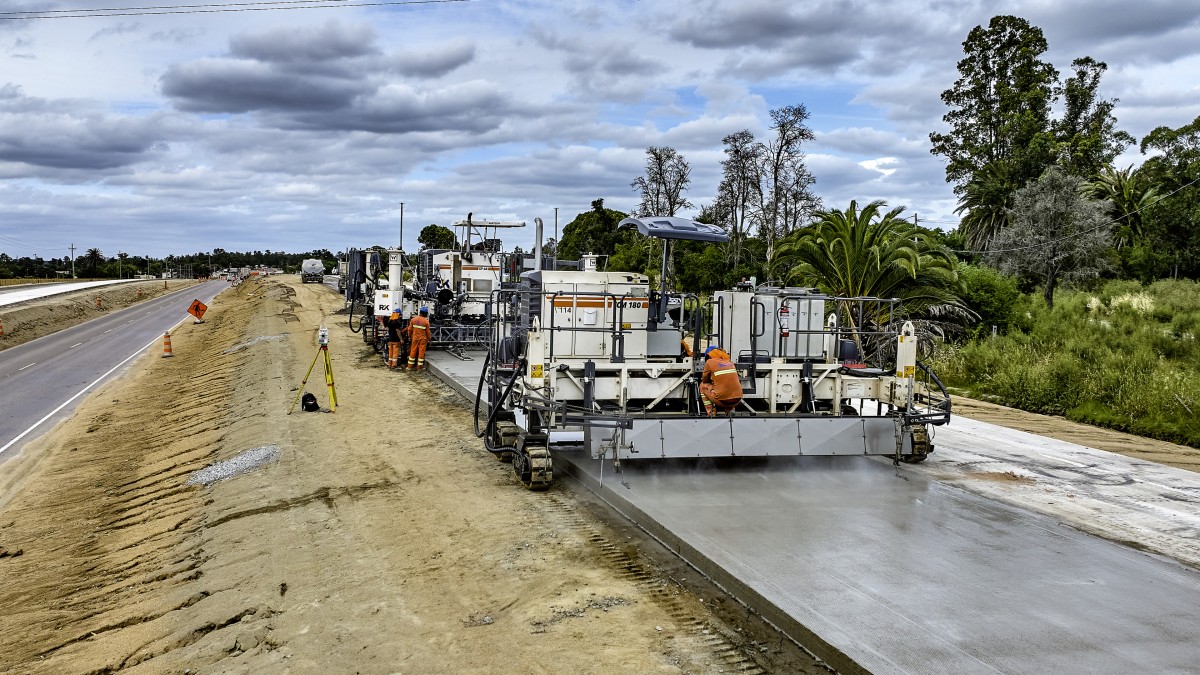
Road Machinery
04/11/2024
Wirtgen: Widening of the Ruta 5 highway from Montevideo to the Brazilian Border
Efficient concrete paving solutions from Wirtgen ensure the...
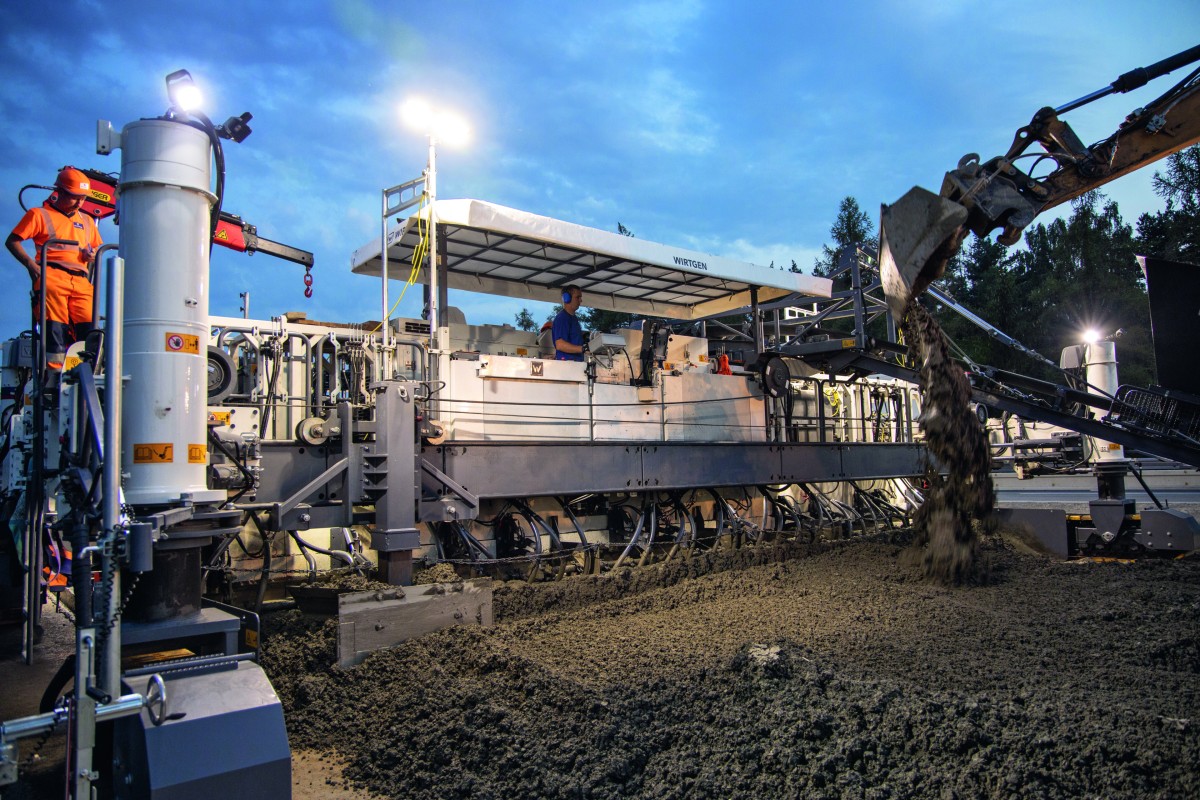
Road Machinery
31/10/2024
Wirtgen: Concrete paving with inset slipform pavers
Wirtgen has been offering machines for inset slipform paving...
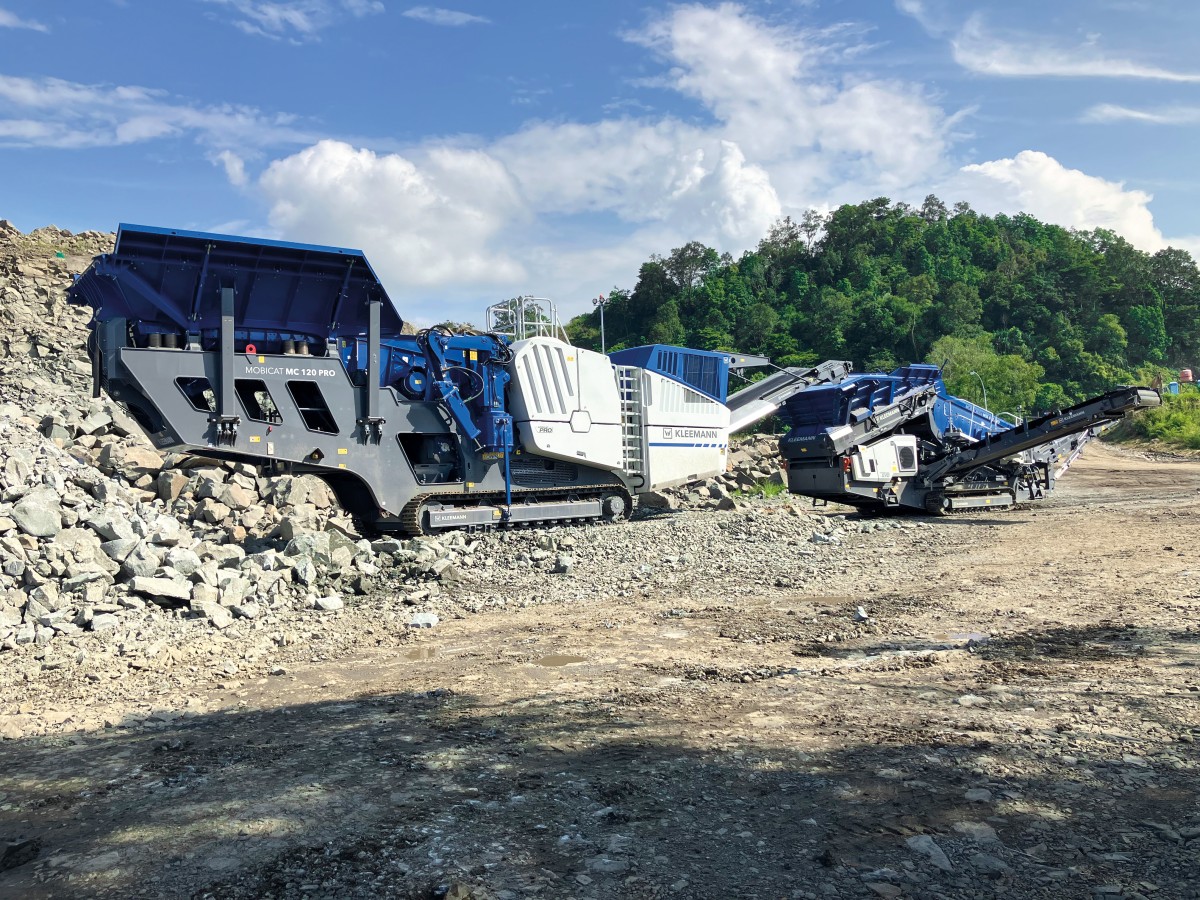
Earthmoving Machinery
28/10/2024
Kleemann: Andesite processing in Indonesia
A MOBICAT MC 120 PRO and a MOBISCREEN MSS 802 EVO are deploy...
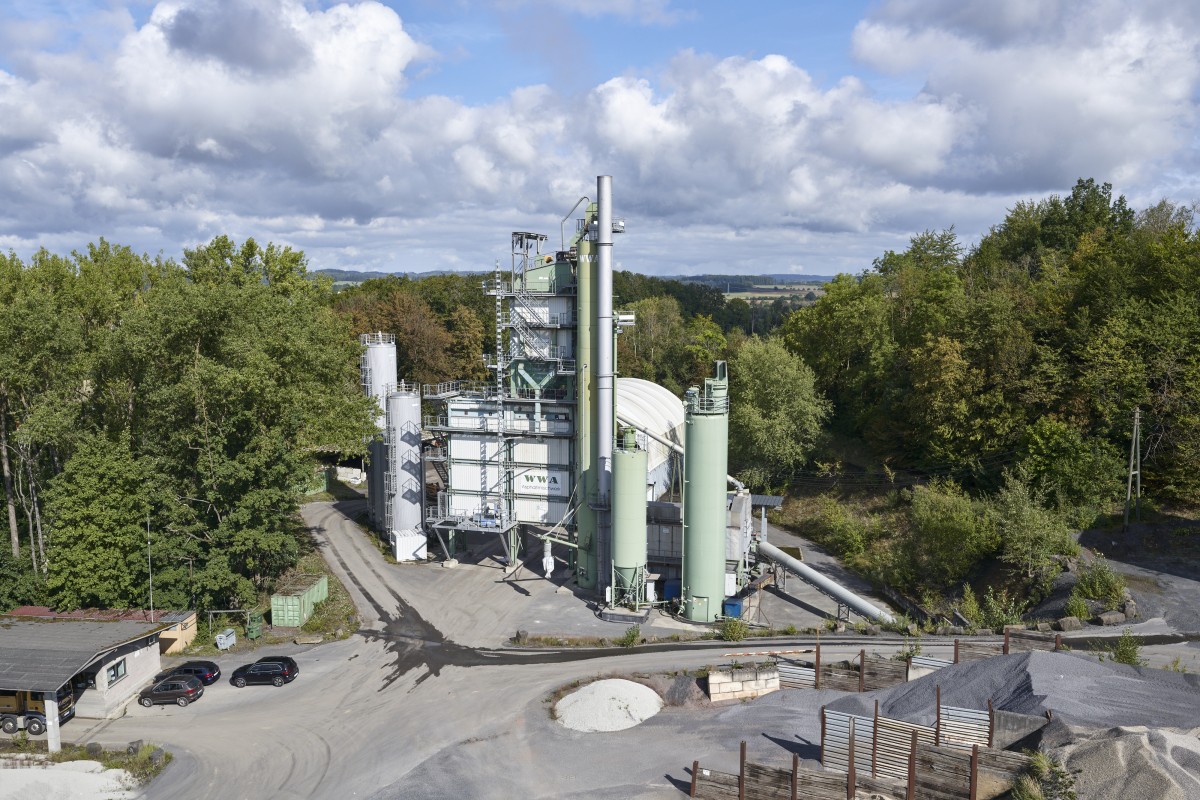
Earthmoving Machinery
24/10/2024
Benninghoven's REVOC system proven in practice
The REVOC Retrofit solution has been installed at an existin...
Road Machinery
01/10/2024
The Wirtgen Group at Paving Expo 2024
The Wirtgen Group presents groundbreaking technologies at Pa...
Altri International
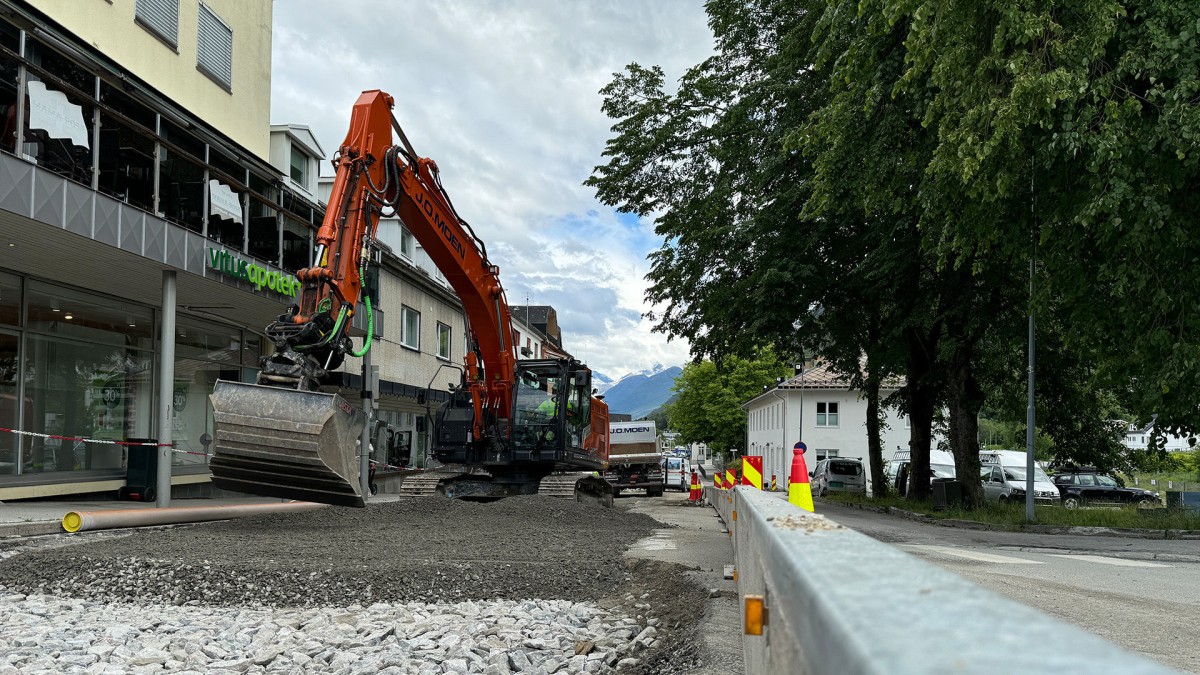
International
28/11/2024
Hitachi's Zaxis-7 excavator is a favourite for Norwegian family-business
Norwegian family business JO Moen AS has added a ZX225USRLC-...
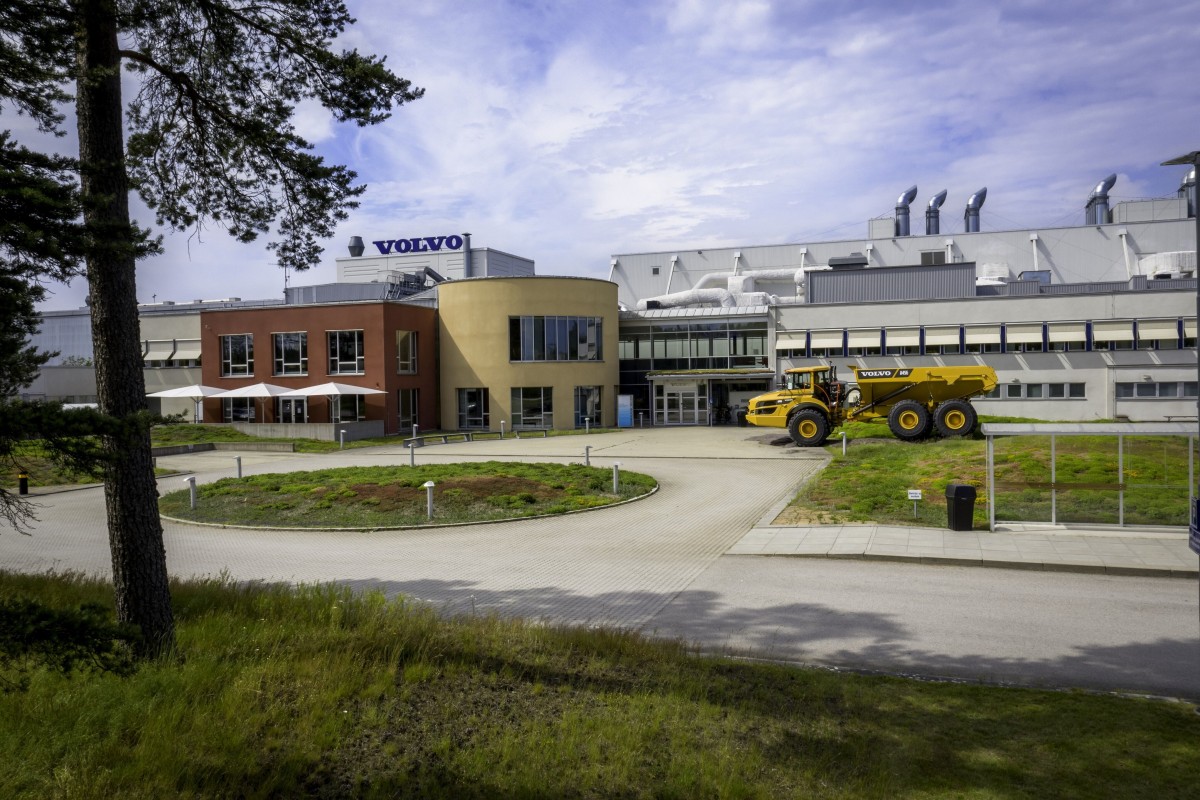
International
27/11/2024
Home of Volvo Construction Equipment’s pioneering articulated haulers advances to Climate Efficient Site
As one of the construction industry’s most active drivers of...
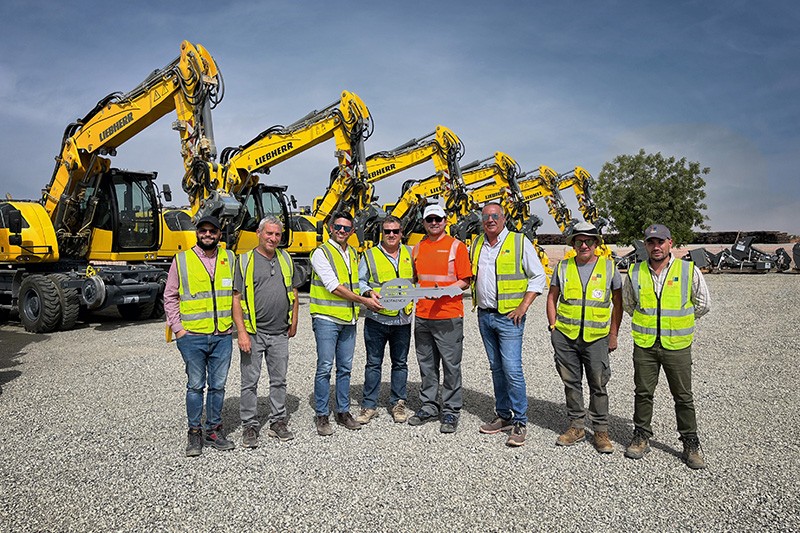
International
26/11/2024
Mota-Engil orders 10 Liebherr railroad excavators for a major project in West Africa
The Portuguese construction company Mota-Engil has once agai...
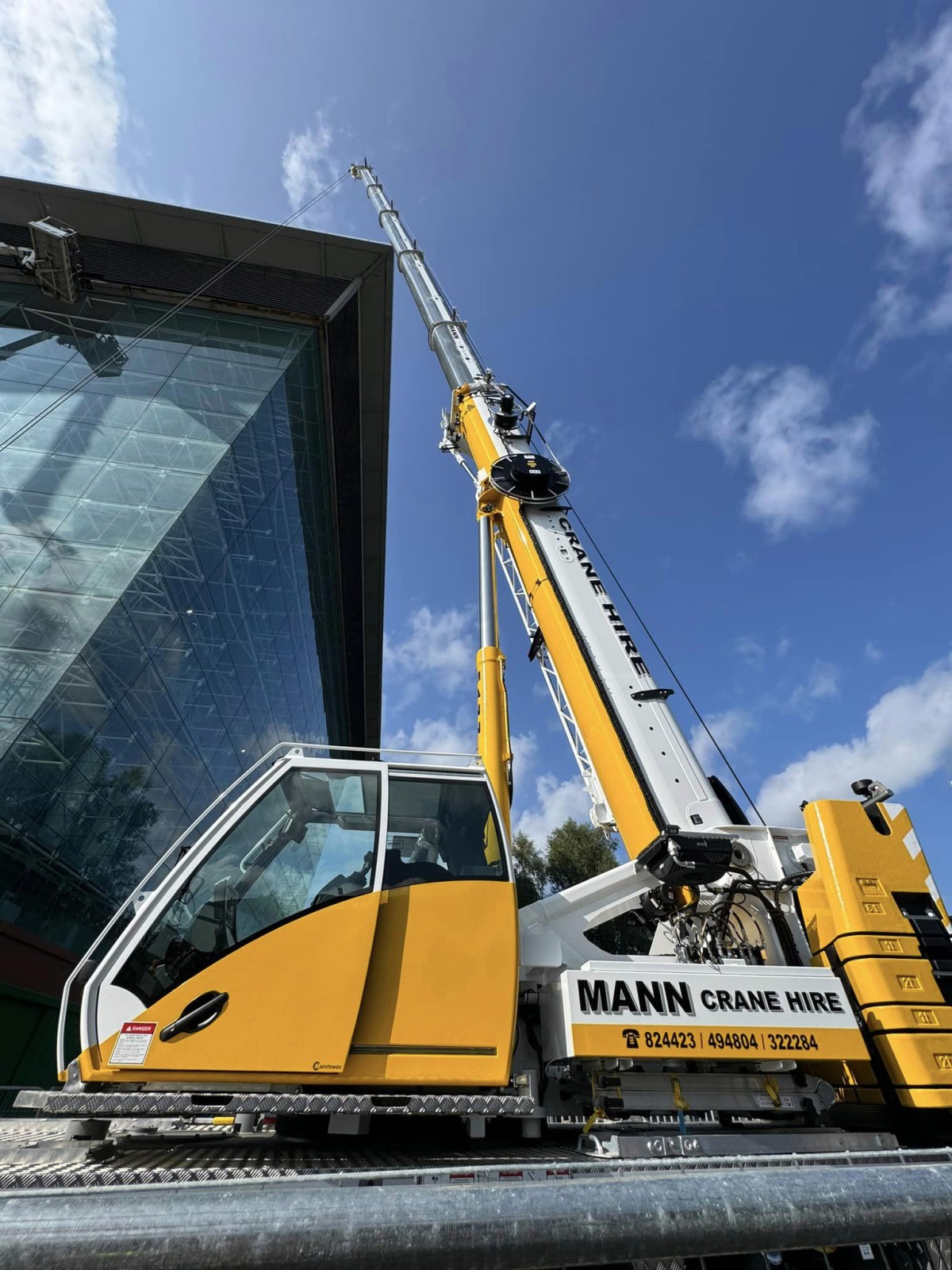
International
25/11/2024
New Grove GMK3060L-1 drives busy schedule for Mann Crane Hire
• Mann Crane Hire selected the GMK3060L-1 for its class-lead...
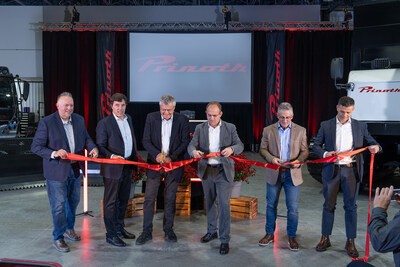
International
25/11/2024
Prinoth Unveils Expanded Production Facility in Granby, Canada
Prinoth held an event to announce the official opening of it...
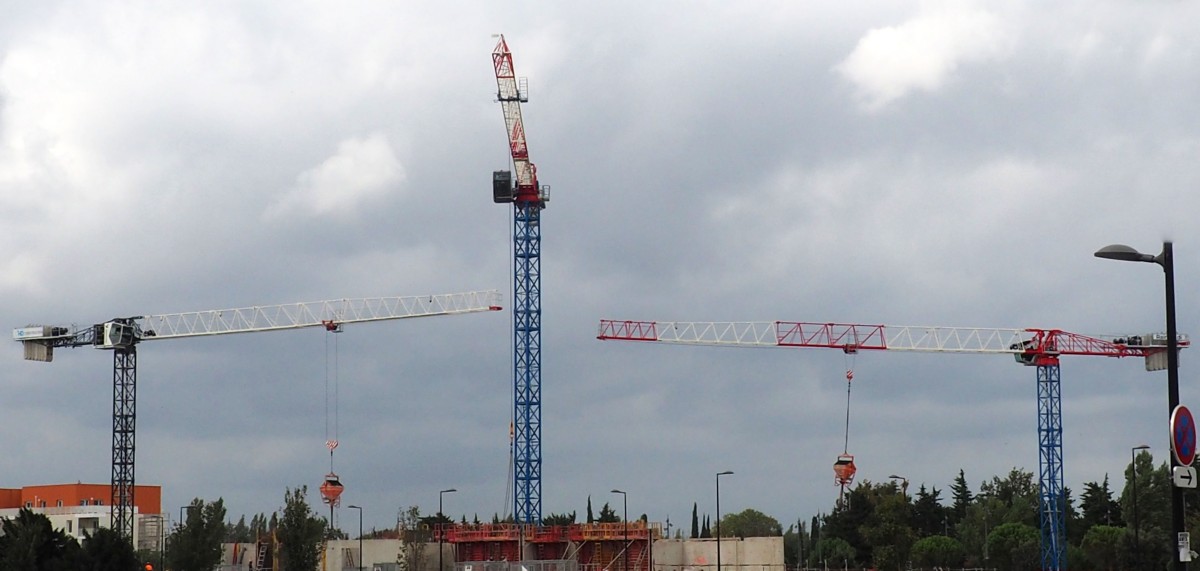
International
23/11/2024
GPMat International takes delivery of two Raimondi T147s residential development in the South of France
- Official agent of France expands its product lineup with t...