Home \ International \ Wirtgen W 200 rehabilitates Brazil’s congested road network
Wirtgen W 200 rehabilitates Brazil’s congested road network
20/08/2018
Pubblicato da Redazione
With precision milling results and flexible deployment options, the Wirtgen large milling machine put in a convincing performance in the rehabilitation of two main traffic arteries between São Paulo and Brazil’s
With precision milling results and flexible deployment options, the Wirtgen large milling machine put in a convincing performance in the rehabilitation of two main traffic arteries between São Paulo and Brazil’s largest port.
Job for a W 200 in the Brazilian uplands
The Anchieta-Imigrantes motorway system is the main link between the metropolitan region of São Paulo and the port of Santos, the largest port in Brazil and the busiest in Latin America. Construction of the Anchieta motorway began in 1947, with Imigrantes following at the start of the 1970s. Today the Anchieta handles mainly heavy goods traffic – 95 % of its daily traffic consists of trucks – while cars predominantly use the Imigrantes. Now the two motorways are being rehabilitated over a total length of 300km. The removal of the surface and binder course was handled by a Wirtgen large milling machine of type W 200.
Precise and economic milling
The high proportion of heavy-goods vehicles and the significant traffic density place enormous strain on the asphalt surfaces, making regular maintenance vital. The contract for the current job was won by the Baixada Santista Consortium. The construction company CR Almeida, which is part of the consortium and responsible for the milling, worked alternately on both roads – northbound and southbound. While the W 200 milled the Anchieta motorway, which was closed completely, traffic was diverted to the Imigrantes motorway.
Milling rate up
For this mammoth project, CR Almeida is using the efficient W 200 large milling machine, which runs in continuous operation 24 hours a day during the rehabilitation work. This is where the powerhouse can really put its enormous capabilities to the test.
That’s because the W 200, with its powerful engine delivering a maximum power of 410 kW, is specially configured for high area outputs – whether on large sites or in confined spaces. The manoeuvrability of the large milling machine particularly proves its worth in the very narrow defiles that snake their way through the Brazilian uplands 40 km south of São Paulo, so that the W 200 was able to mill both road surfaces over a width of 2 m and to a depth of 8 cm rapidly and precisely in one operation.
Operating costs down
Milling machine operator Janderson de Souza Mota emphasises the ease of handling offered by the WIDRIVE machine control system, which links the most important machine functions together: “While the engine, for instance, sets the operating speed automatically when the milling process is started, it automatically returns to its idling speed when milling is finished. This allows us to reduce not only fuel consumption but also noise emissions.” What is more, the water required for cooling the cutting tools is regulated as a function of the engine load and milling speed. The load-dependent sprinkler unit allows a water saving of up to 20 %. “For us that means we need to fill up less water, but the service life of the cutting tools is still longer,” says the site Manager Cleiton Farias de Jesus, delighted with the much lower downtimes.
Transport made easy
With the milling work on the Anchieta motorway having been completed faster than anticipated that day, the W 200 even made up time before it was to begin its scheduled night-time job on the Imigrantes motorway. So, without hesitation, Cleiton Farias de Jesus and his team stopped at Cubatao, just a few kilometres away, in order to mill a strip a few hundred metres long over a working width of 2m, but this time to a depth of 28 cm. “The site is on the way, and the fact that we can load and unload the W 200 quickly and easily enabled us to fit this little job in today.”
The folding loading belt, for instance, shortens the transport length of the large milling machine, so that it can be transported even on light low-bed trucks with a low overall weight. The weather canopy can also be folded in hydraulically for onward transport. Site Manager Cleiton Farias de Jesus says: “Ease of transport is a decisive criterion and makes the logistics a whole lot easier. This way, we can move quickly from one job to the next and always make optimum use of the W 200’s capacity.”

Ultime notizie di Wirtgen Macchine
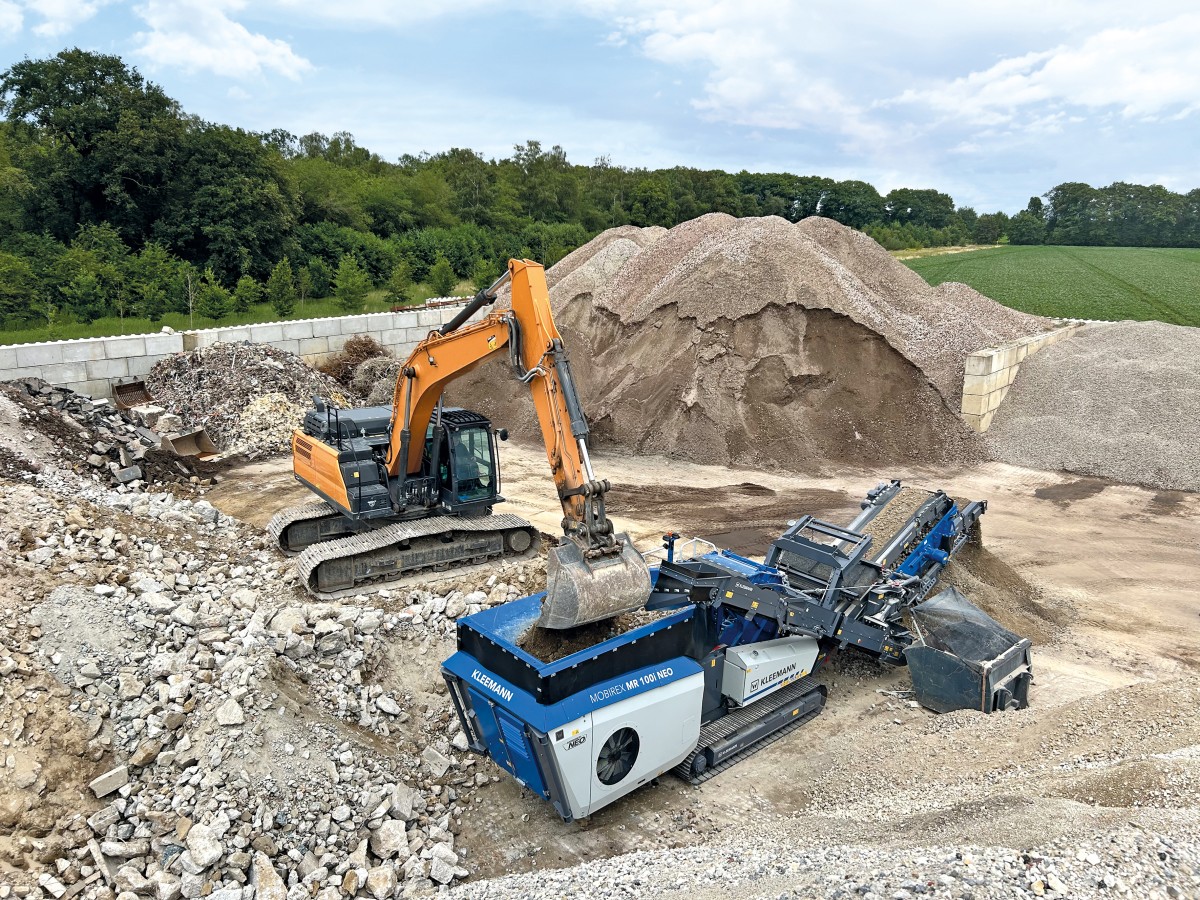
Earthmoving Machinery
21/11/2024
Kleemann: New compact crusher used for recycling
Impact crusher MOBIREX MR 100i NEO impresses during operatio...
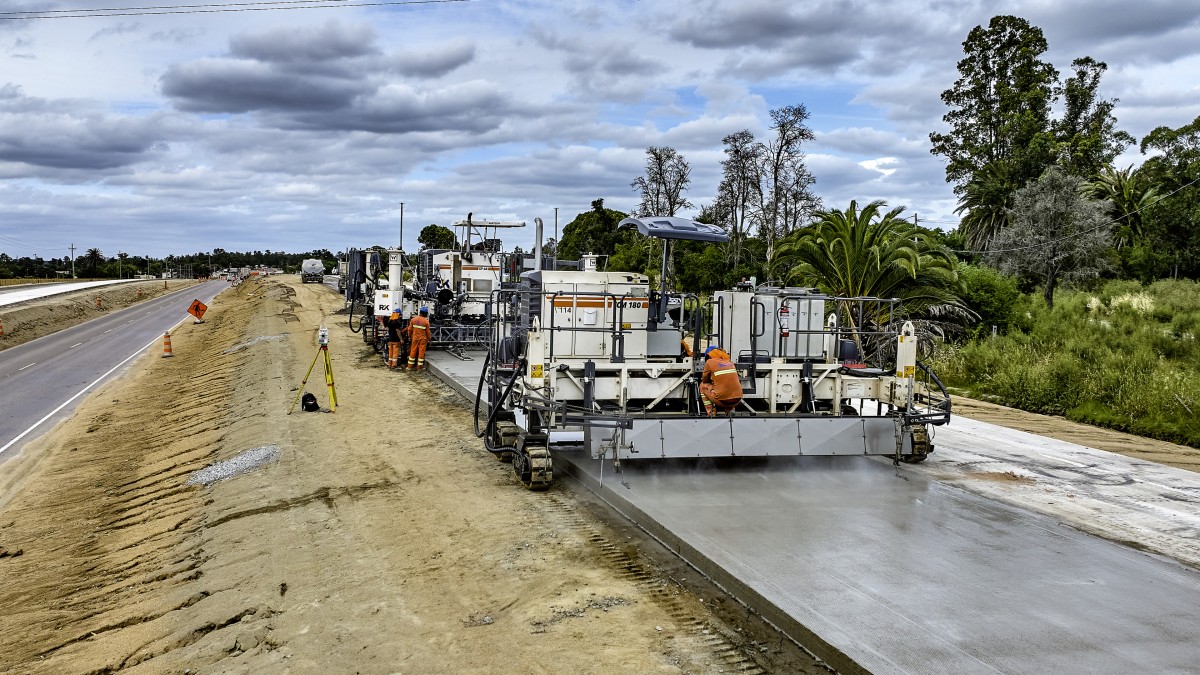
Road Machinery
04/11/2024
Wirtgen: Widening of the Ruta 5 highway from Montevideo to the Brazilian Border
Efficient concrete paving solutions from Wirtgen ensure the...
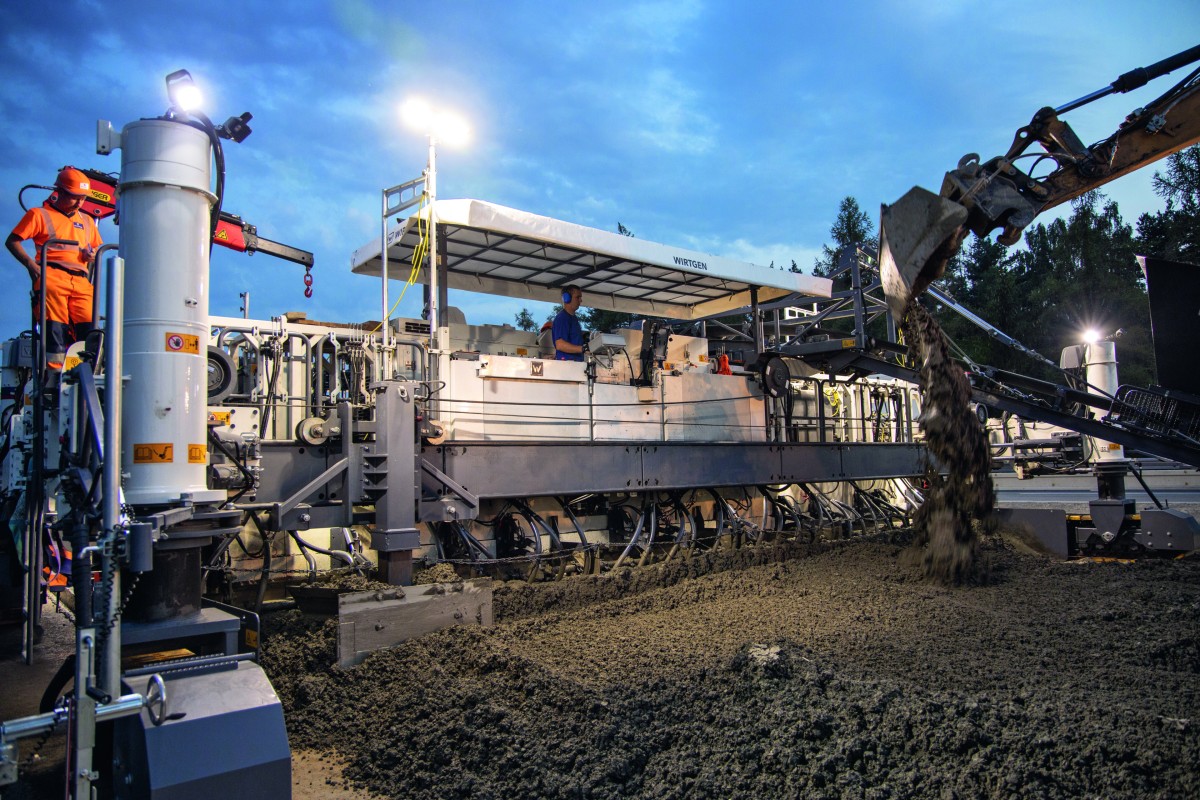
Road Machinery
31/10/2024
Wirtgen: Concrete paving with inset slipform pavers
Wirtgen has been offering machines for inset slipform paving...
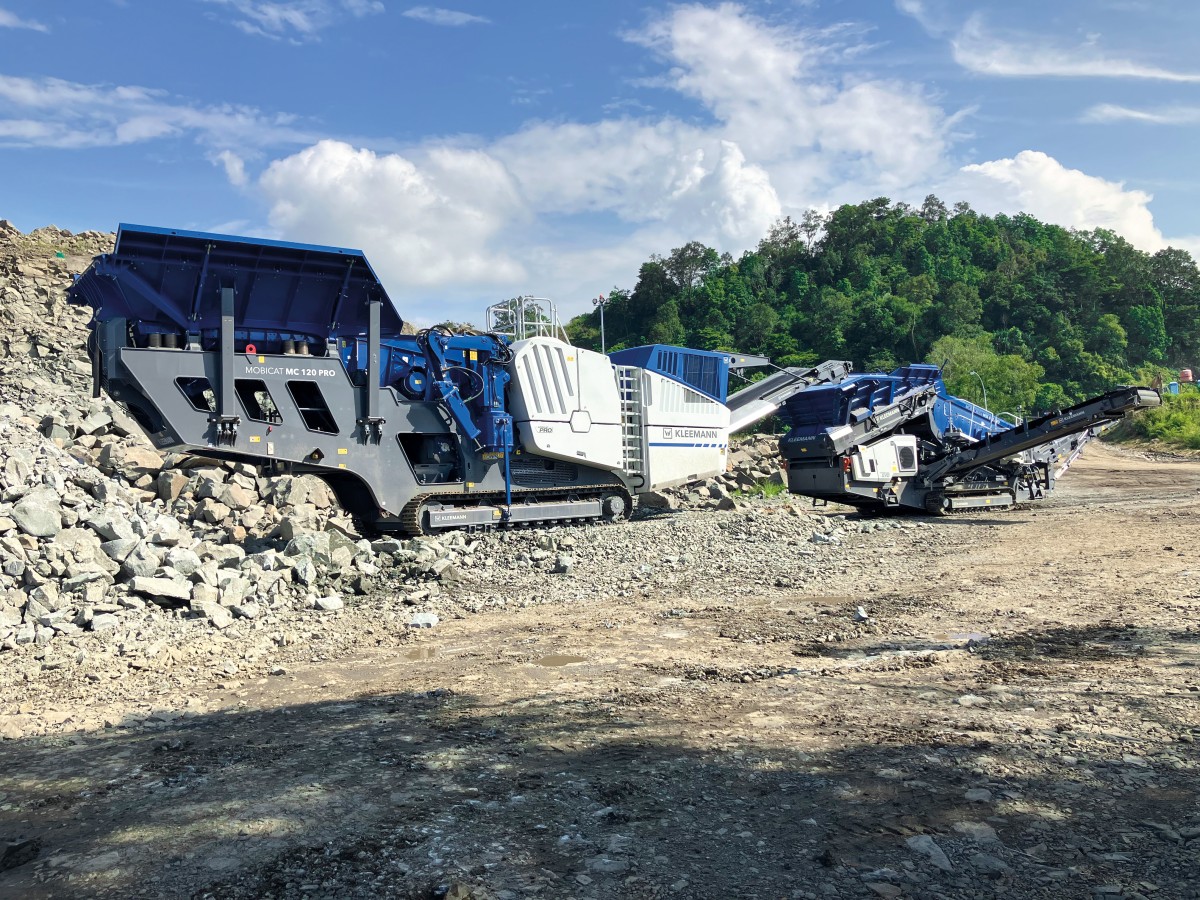
Earthmoving Machinery
28/10/2024
Kleemann: Andesite processing in Indonesia
A MOBICAT MC 120 PRO and a MOBISCREEN MSS 802 EVO are deploy...
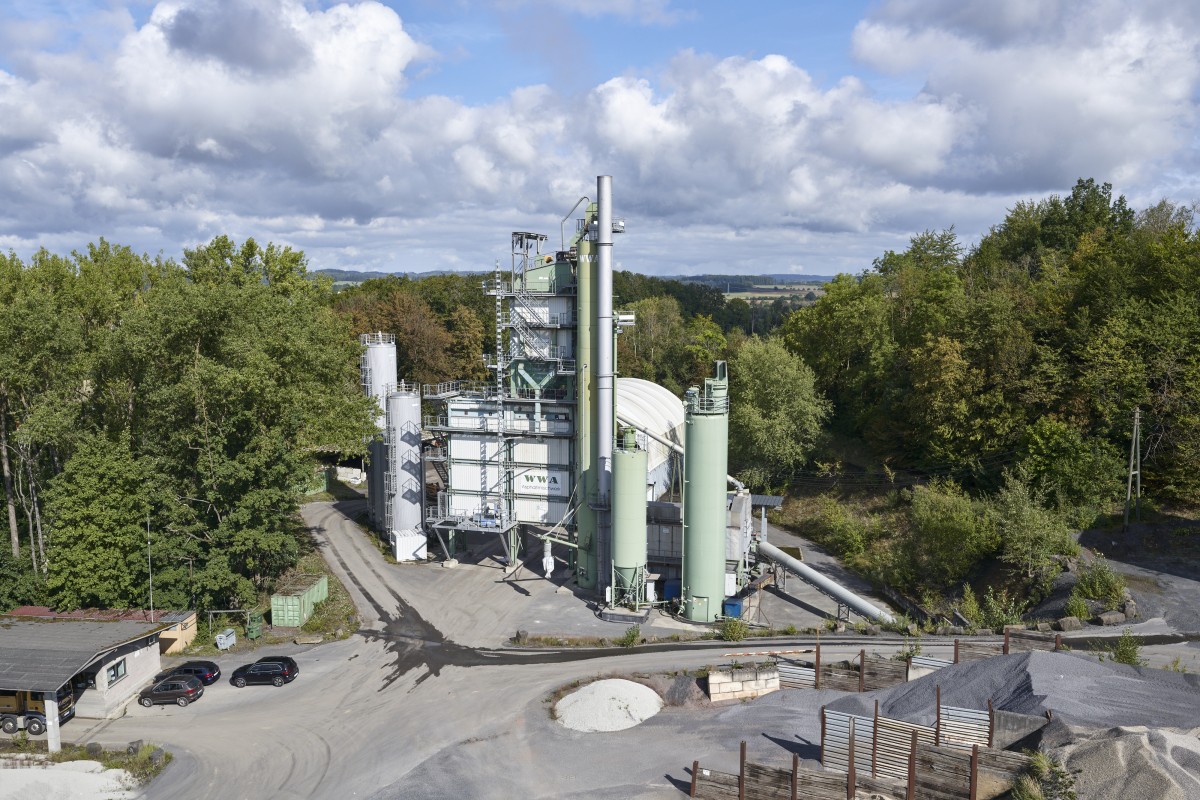
Earthmoving Machinery
24/10/2024
Benninghoven's REVOC system proven in practice
The REVOC Retrofit solution has been installed at an existin...
Road Machinery
01/10/2024
The Wirtgen Group at Paving Expo 2024
The Wirtgen Group presents groundbreaking technologies at Pa...
Altri International
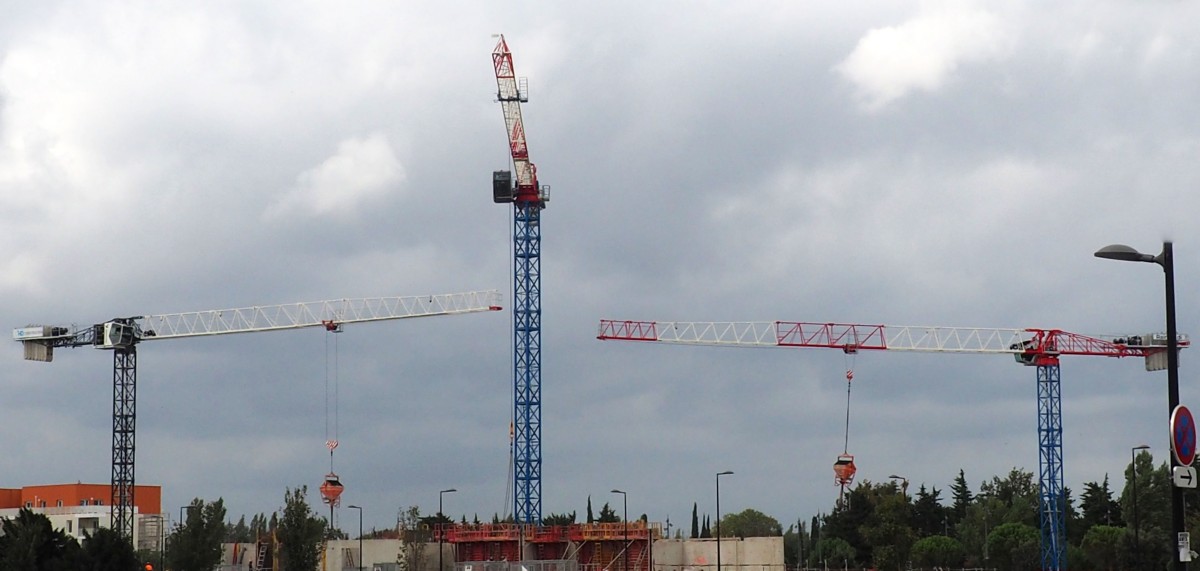
International
23/11/2024
GPMat International takes delivery of two Raimondi T147s residential development in the South of France
- Official agent of France expands its product lineup with t...
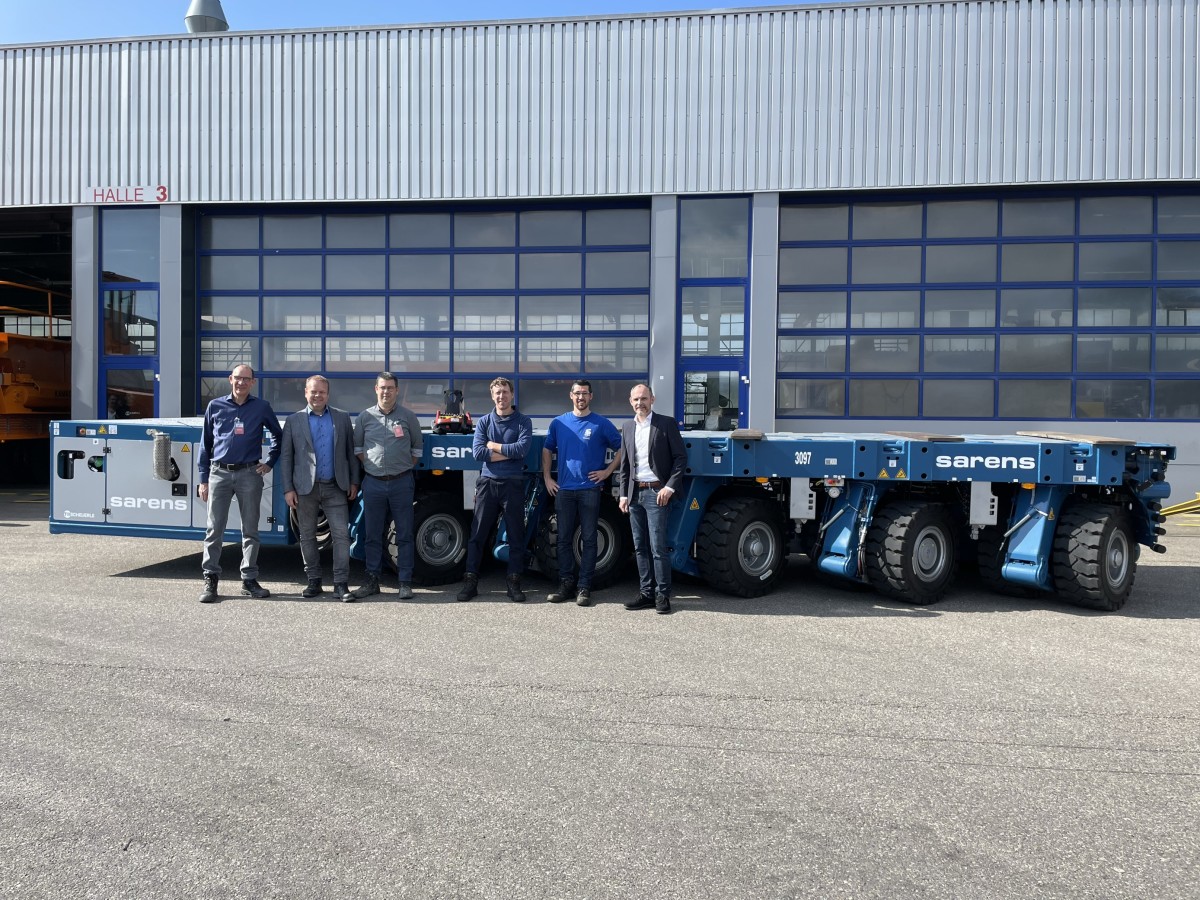
International
22/11/2024
Sarens acquires additional SCHEUERLE SPMT K24 modules
renowned for its expertise in crane rental services, heavy l...
International
22/11/2024
Five WOLFF cranes modernize Oslo’s Ulven district
With a total of five WOLFF cranes of type 7534.16 Clear, Wol...
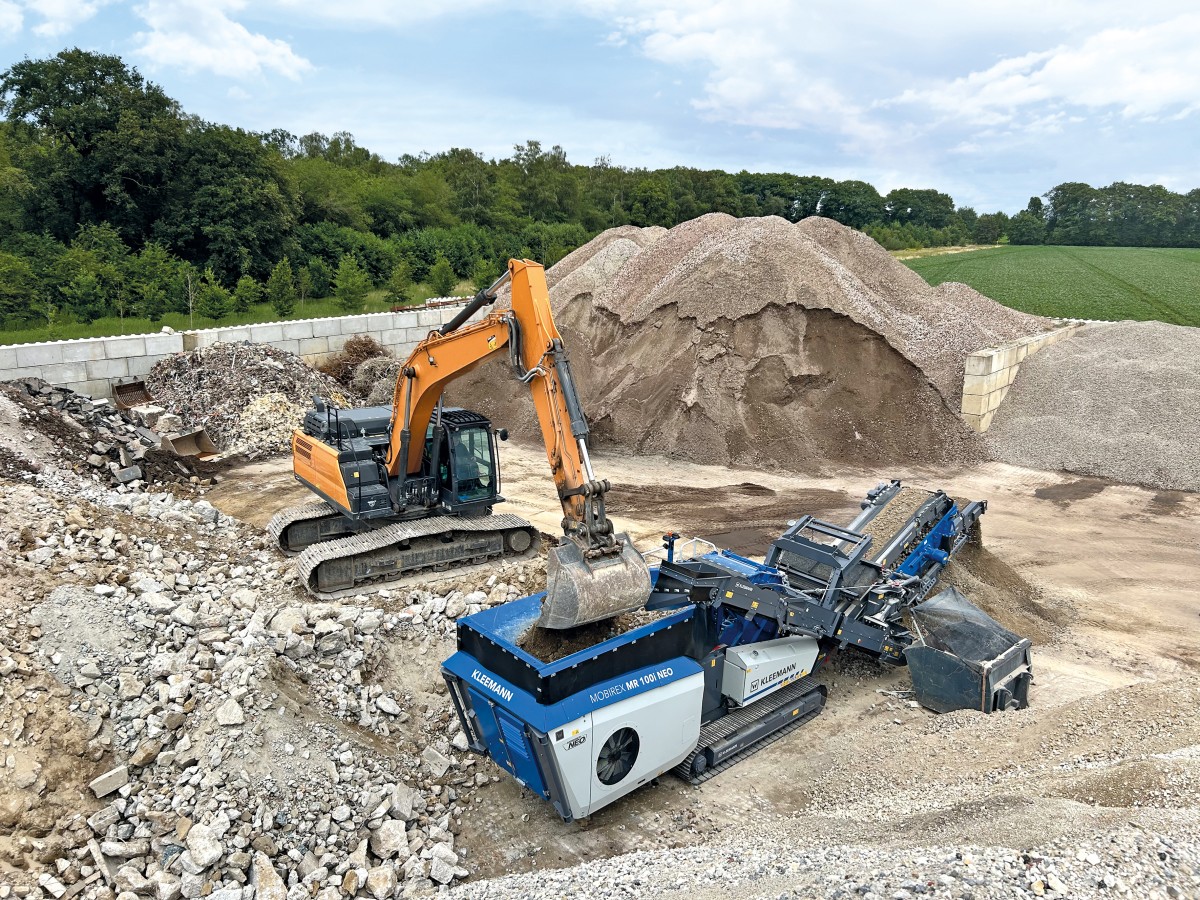
International
21/11/2024
Kleemann: New compact crusher used for recycling
Impact crusher MOBIREX MR 100i NEO impresses during operatio...
International
21/11/2024
SITECH partners with Royal Engineers to create poppy and demonstrate tech offering
The demostration involved creating a ground-level poppy desi...
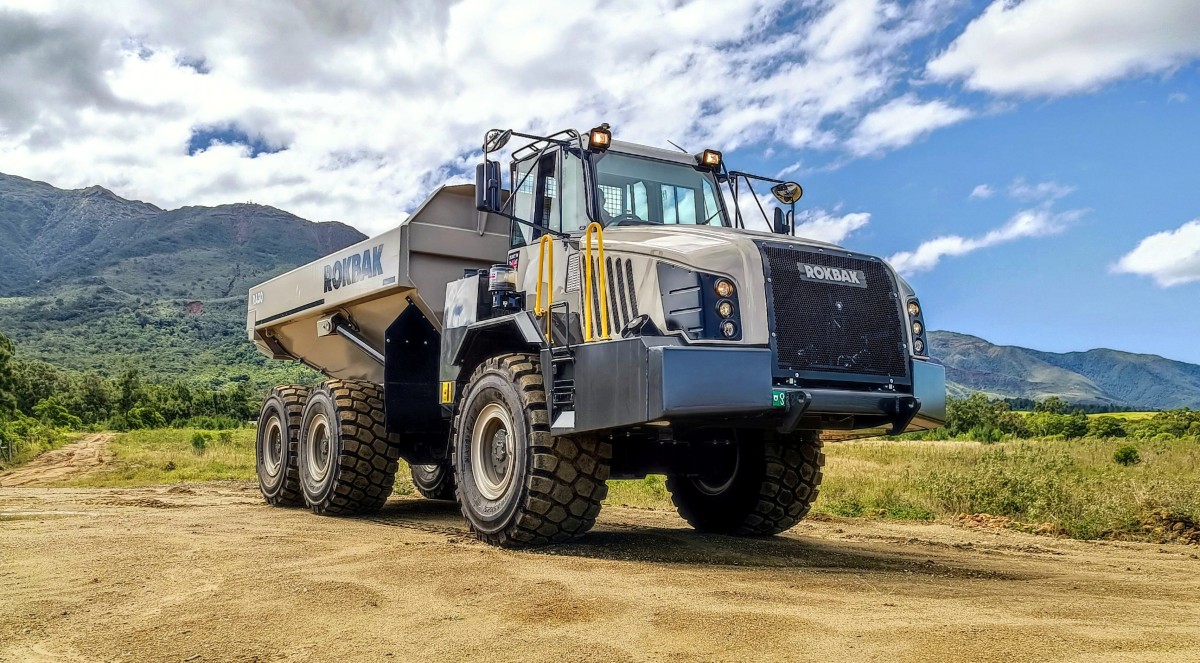
International
20/11/2024
Strong and stable RA30 trucks carry the weight at New Caledonian mine
Three Rokbak RA30 trucks are delivering exceptional durabili...