Home \ International \ World premiere for the Liebherr L 507 and L 509 stereoloaders
World premiere for the Liebherr L 507 and L 509 stereoloaders
16/05/2018
Pubblicato da Redazione
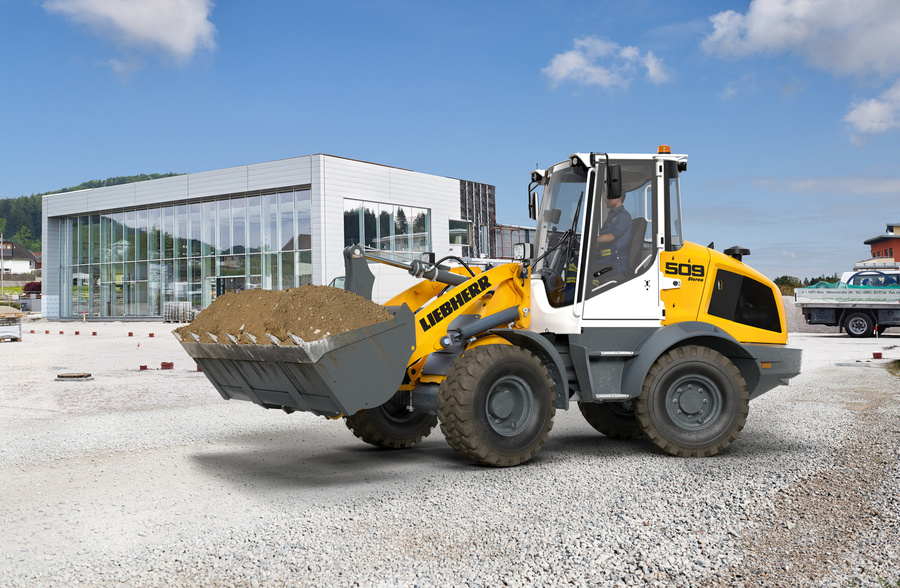
The new Liebherr L 507 and L 509 stereoloaders celebrated their world première at Intermat 2018. This completes the latest stereoloader range, which has a total of four models and features operating weights of 5.5 to 9.2 tonnes
The new Liebherr L 507 and L 509 stereoloaders celebrated their world première at Intermat 2018.
This completes the latest stereoloader range, which has a total of four models and features operating weights of 5.5 to 9.2 tonnes. The stereo steering, which has proved itself over the last 20 years, is at the heart of the Liebherr stereoloaders. Particular to Liebherr, this steering system offers a significantly smaller turning circle than other articulated wheel loaders. The appeal of the new L 507 and L 509 models also lies in the spacious operator's cab and intuitive operation. Thanks to numerous practical innovations, such as the optimised Z-bar linkage, the new models facilitate efficient work on site.
The L 507 and L 509 stereoloaders are two of the largest all-rounders in the Liebherr range of wheel loaders. They boast high levels of productivity when it comes to horticulture and landscaping and when operating in urban environments. On construction sites, they can handle earthmoving and preparatory work. Their powerful hydrostatic driveline ensures optimal performance. Both models are available in a ‘Speeder’ version on request. This version of the wheel loaders can achieve a top speed of 38 km/h, helping operators to save time and to move their stereoloader from one job to the next quickly. Thanks to the efficient exhaust after-treatment with diesel oxidation catalyst (DOC) and diesel particulate filter, the L 507 and L 509 comply with the latest emission standards in this machine class, namely Stage IIIB / Tier 4f.
Versatility thanks to stereo steering and optimised Z-bar linkage
First introduced in 1994 and proving itself ever since, the stereo steering developed by Liebherr still qualifies as unique: it is a perfectly balanced combination of articulated steering and a steered rear axle. This means that it combines the advantages of conventional articulated steering with the advantages of all-wheel steering, resulting in the smallest possible turning circle, which is especially advantageous in confined spaces. The steered rear axle allows Liebherr engineers to reduce the articulation angle of the stereoloaders to 30 degrees. As a result, the centre of gravity remains in the middle of the machine even when transporting heavy loads, increasing overall stability.
Numerous optimisations characterise the Z-bar linkage of the new stereoloaders. The powerful lift arm combines high breakout forces below with vast holding forces up above. Liebherr has improved the parallel guide system for operation with a loading fork. Machine operators can therefore work efficiently and economically with the widest range of attachments. The newly-designed, slim hydraulic quick hitch, which enables a clear view of the equipment, provides assistance when the attachments are being replaced. The Liebherr High Lift arm is available for the L 509 on request. This longer version of the lift arm provides increased reach and increases the dump-over height by approximately half a metre.
Safe working thanks to easy operation and high levels of comfort
To promote work efficiency, Liebherr stereoloaders combine comfort and safety in a single machine. The compact design ensures stability and makes it easier for the machine operator to have a clear overview of the wheel loader and its surroundings. The proven articulated oscillating bar also provides advantages when it comes to comfort and safety. It compensates for uneven ground and provides balanced overall stability and tipping stability when crossing obstacles. This ensures efficient and safe loading procedures, even on rough terrain. What's more, the automatic self-locking differentials increase traction. Consequently, even inexperienced machine operators can work safely and efficiently using the Liebherr stereoloaders.
The L 507 and L 509 stereoloaders feature one of the most spacious operator's cabs in this machine class. Liebherr has installed the popular operator's cab from the larger L 514 and L 518 stereoloaders in both the L 507 and L 509. In addition to the large interior, the uncluttered cockpit also impresses, thanks to its clear layout. Generous glass surfaces improve visibility on all sides. All controls, such as the Liebherr control lever integrated into the driver's seat as standard, are convenient to use. Working and driving functions are self-explanatory and can be learnt intuitively. These measures increase safety, particularly if several different machine operators work with the same wheel loaders. Additional clever solutions in the cab include the vent window that can be opened by 180 degrees and the height-adjustable display.
Intelligent solutions for cooling systems and servicing
As with all Liebherr wheel loaders, the cooling system in the new stereoloaders is located directly behind the operator's cab. This is the cleanest position on the wheel loader, reducing the level of dirt or dust. The on-demand cooling system in the L 507 and L 509 models draws in the air at the sides and guides it through the engine compartment. The engineers can therefore ensure consistent cooling performance and machine availability increases. Additional protective measures, such as a reversible fan drive, fluff screen and a coarse-meshed radiator grille, are available on request for particularly dust-intensive applications.
Intensive long-term endurance tests demonstrate the durability of the new stereoloaders. Liebherr produces key components in-house or in close collaboration with premium manufacturers. The machines have practical details that facilitate any necessary maintenance and service. A quick walk around the wheel loader is all that is needed to see check points and fluid levels. The entire engine compartment is accessible by opening the engine hood. Maintenance points can be accessed safely and easily from the ground. As a result, operators save time and productivity increases.

Ultime notizie di Liebherr EM-Tec Italia
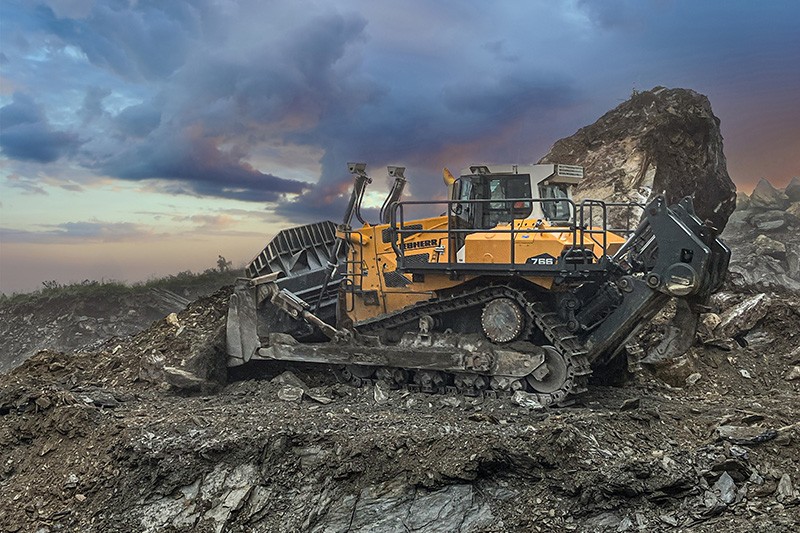
Earthmoving Machinery
22/10/2024
Hollaus company puts Liebherr to the test in reservoir construction
Equally impressive is the tremendous ripping and pushing per...
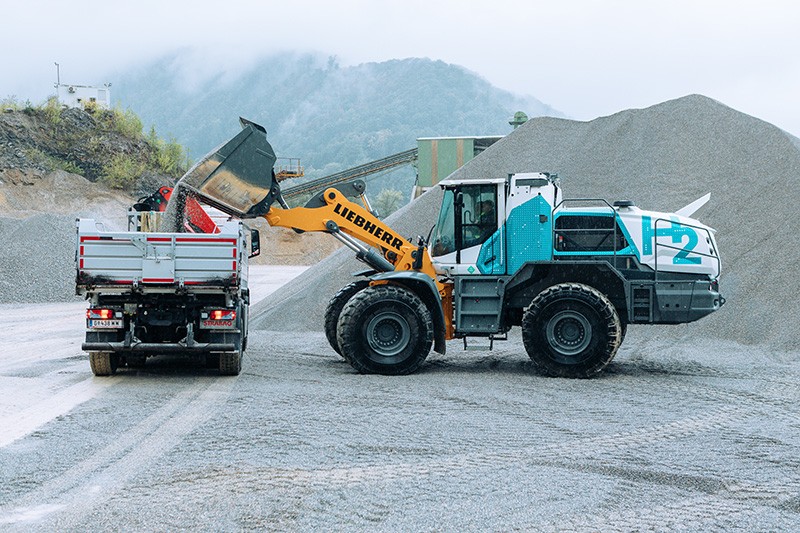
Earthmoving Machinery
18/10/2024
Liebherr and STRABAG test hydrogen wheel loader
Together with STRABAG, Liebherr is taking important steps to...
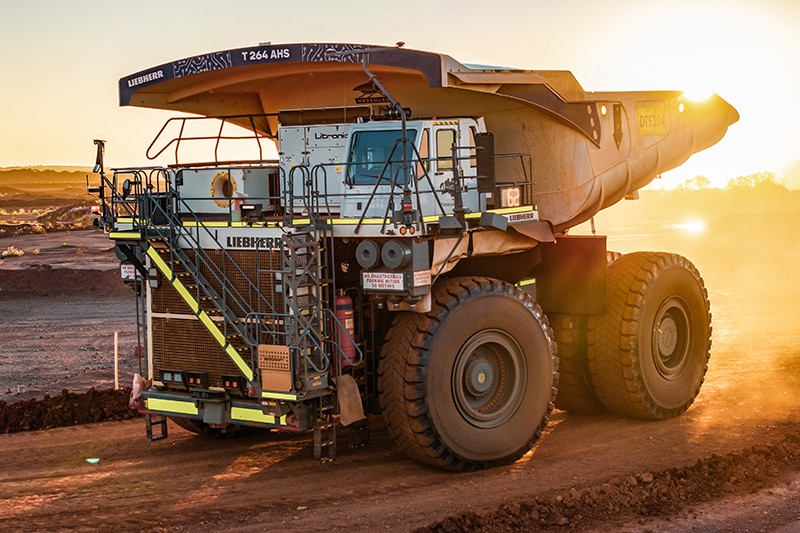
Earthmoving Machinery
07/10/2024
Liebherr’s expanded technology portfolio for integrated operations
Liebherr presented its updated and expanded technology portf...
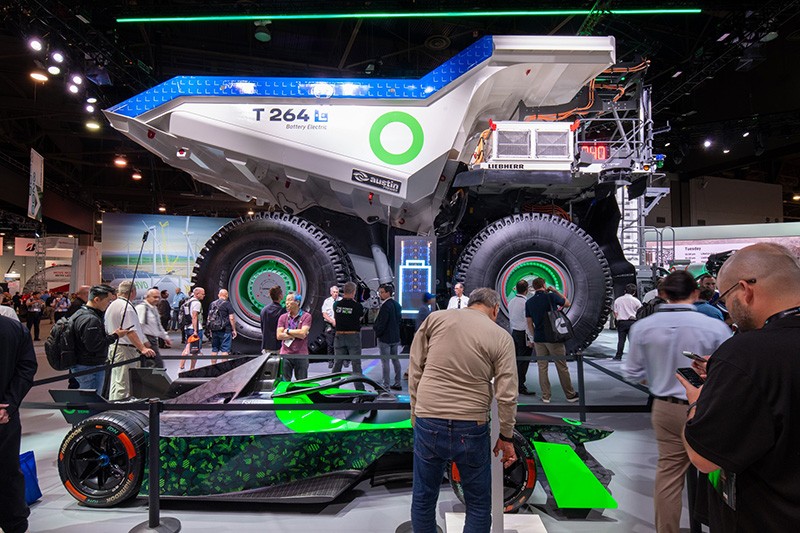
Earthmoving Machinery
27/09/2024
Liebherr presented its latest mining technology at MINExpo 2024
During the exhibition, Liebherr unveiled its autonomous batt...

Earthmoving Machinery
11/09/2024
High efficiency and power output: Liebherr crawler dozer PR 776
Spanish construction company AMM invests in Liebherr Crawler...
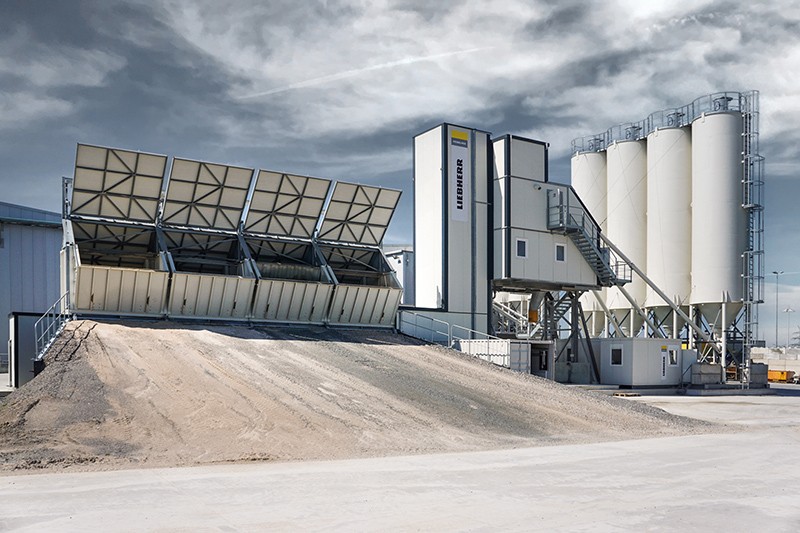
Earthmoving Machinery
02/09/2024
Liebherr-Mobilmix supplies quality concrete for the wind industry
Enercon Emden originally purchased a Liebherr Kombimix 2.25...
Altri International
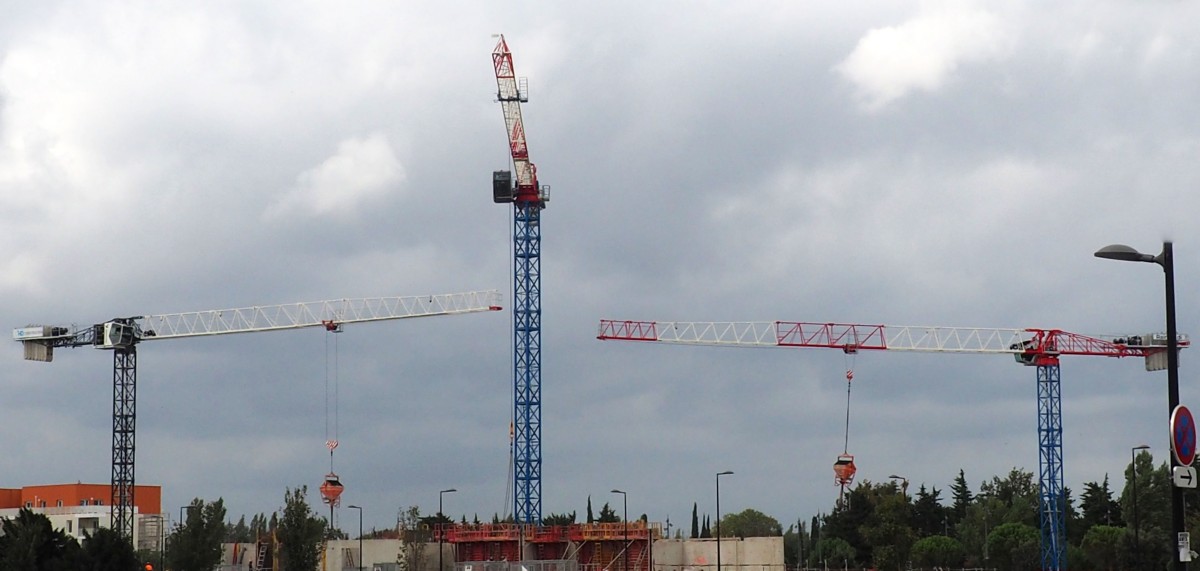
International
23/11/2024
GPMat International takes delivery of two Raimondi T147s residential development in the South of France
- Official agent of France expands its product lineup with t...
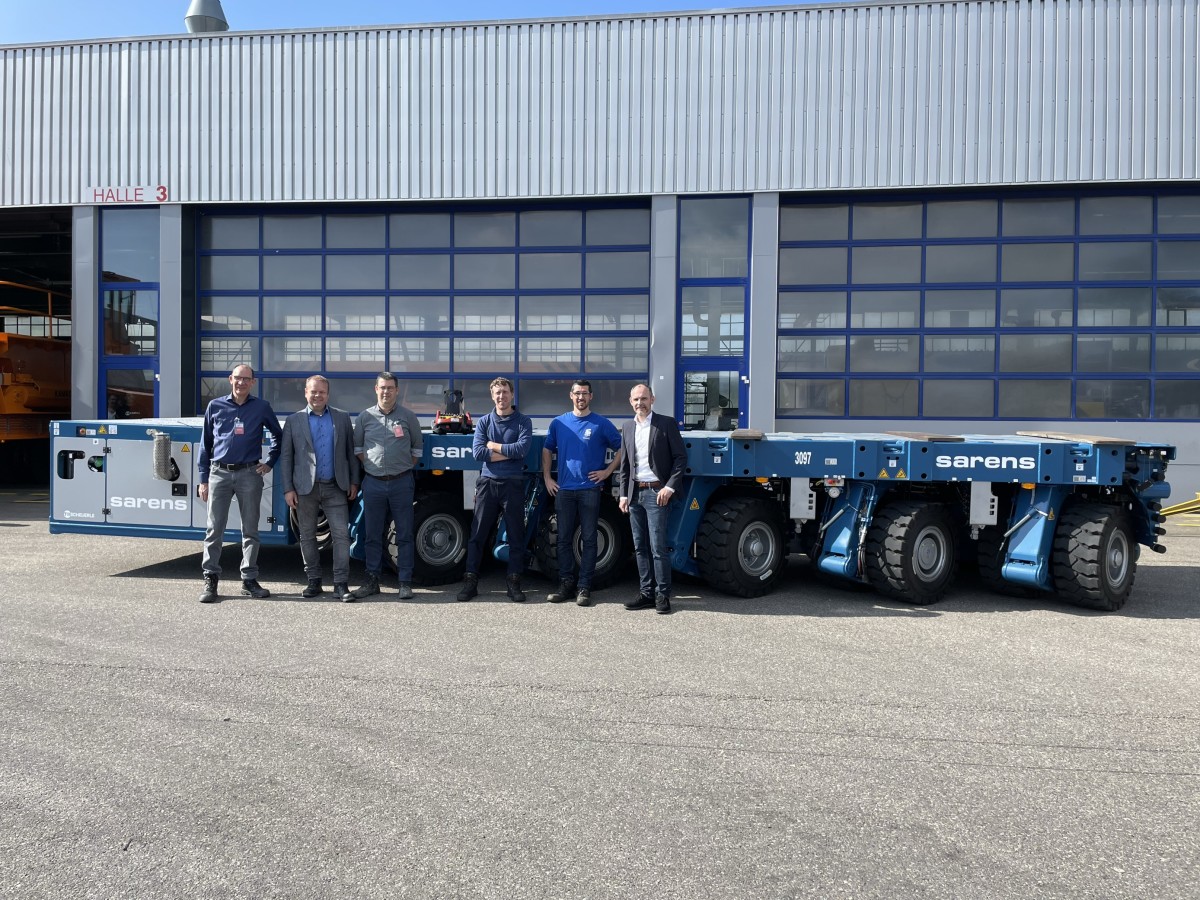
International
22/11/2024
Sarens acquires additional SCHEUERLE SPMT K24 modules
renowned for its expertise in crane rental services, heavy l...
International
22/11/2024
Five WOLFF cranes modernize Oslo’s Ulven district
With a total of five WOLFF cranes of type 7534.16 Clear, Wol...
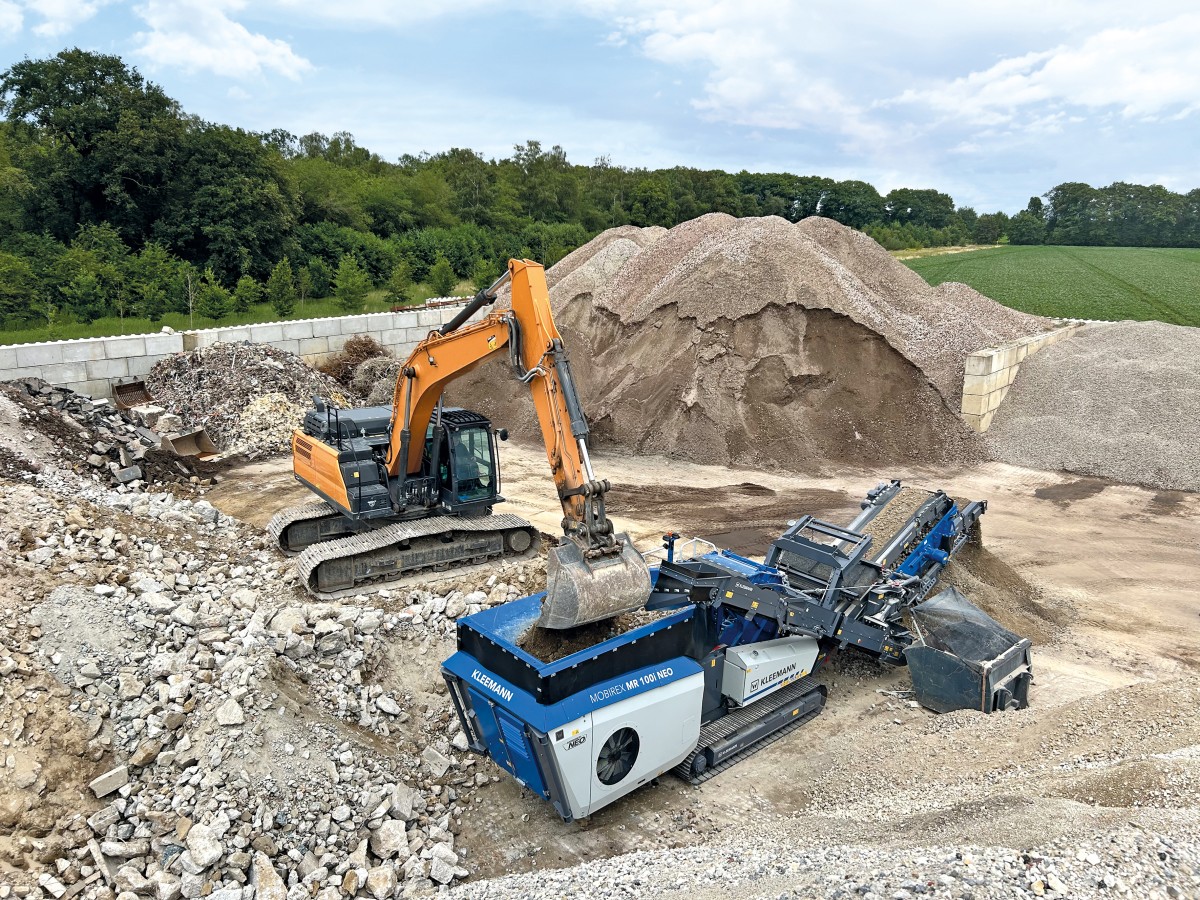
International
21/11/2024
Kleemann: New compact crusher used for recycling
Impact crusher MOBIREX MR 100i NEO impresses during operatio...
International
21/11/2024
SITECH partners with Royal Engineers to create poppy and demonstrate tech offering
The demostration involved creating a ground-level poppy desi...
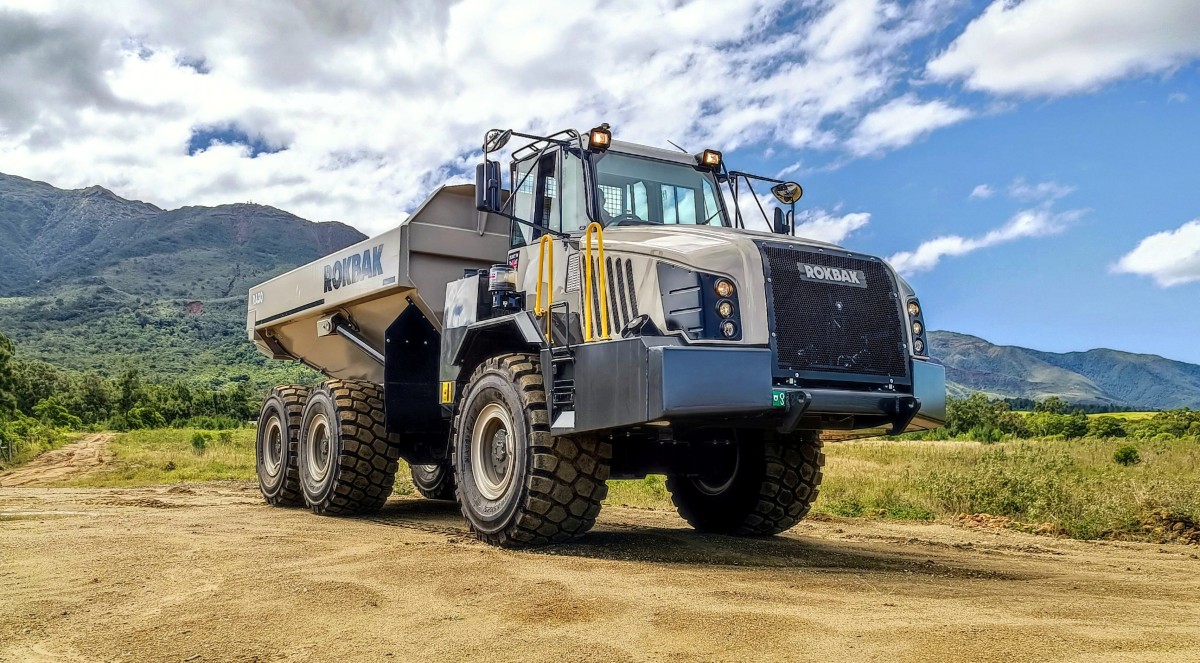
International
20/11/2024
Strong and stable RA30 trucks carry the weight at New Caledonian mine
Three Rokbak RA30 trucks are delivering exceptional durabili...